An overview of the benefits and properties of a growing, alternative product. By Nicholas Benecke and Jason Wigboldy
Mass Timber
in North America
E Pluribus Unum—out of many, one. This phrase is an analogy for what mass timber is. Take many small pieces of wood, bond them together into a massive element that can span greater distances and be more fire resistant than the individual pieces. Soon you can have a building up to 18 stories tall, made of the most low-tech “carbon fiber” the world has ever seen.
Mass timber was invented in Europe in 1994, initially conceived as cross laminated timber, which is in essence plywood made from flatwise 2x6 pieces instead of thin veneers. Thirty years later, the term mass timber has enveloped already existing construction methods, such as dowel laminated timber and nail laminated timber. New variations, such as mass plywood panel, were also added.
About 10 years ago, mass timber made landfall in the United States. Initially seen as a niche design idea, it flew under the radar of most architects. For the past six years, the number of mass timber projects has been doubling every two years and analysts expect it will continue to do so, until it is a multi-billion-dollar industry.
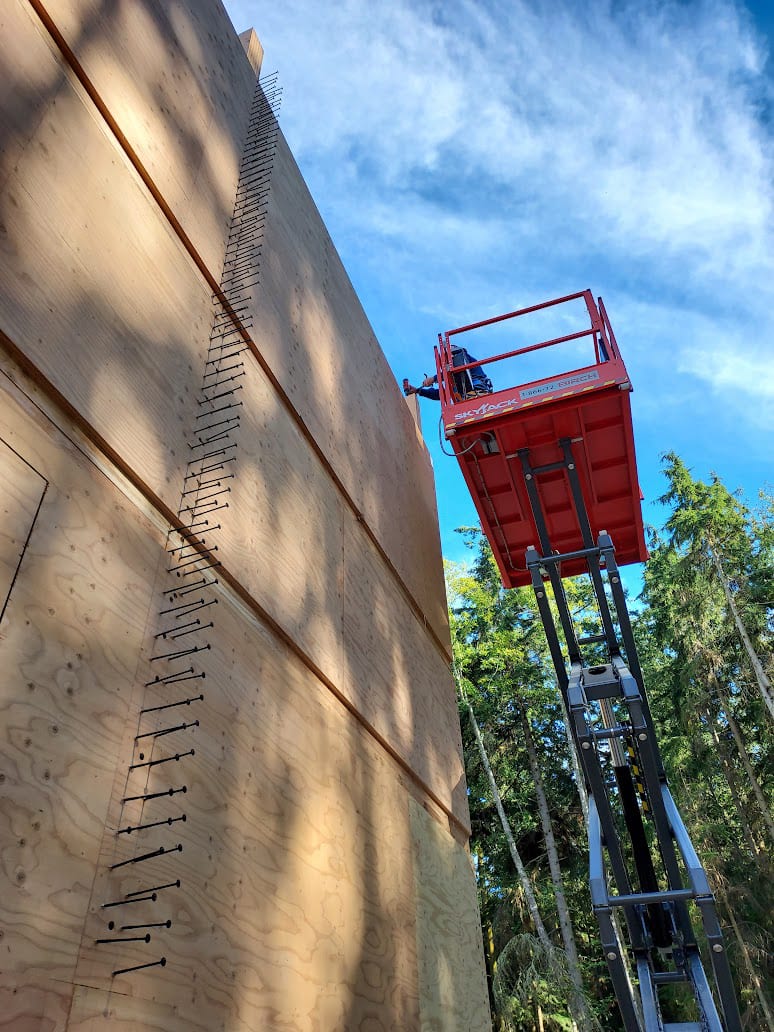
Mass Plywood Panel posts, beams, floor and wall panels—along with SPAX PowerLag screws—are used to construct a Mass Timber structure on Whidbey Island, Wash.
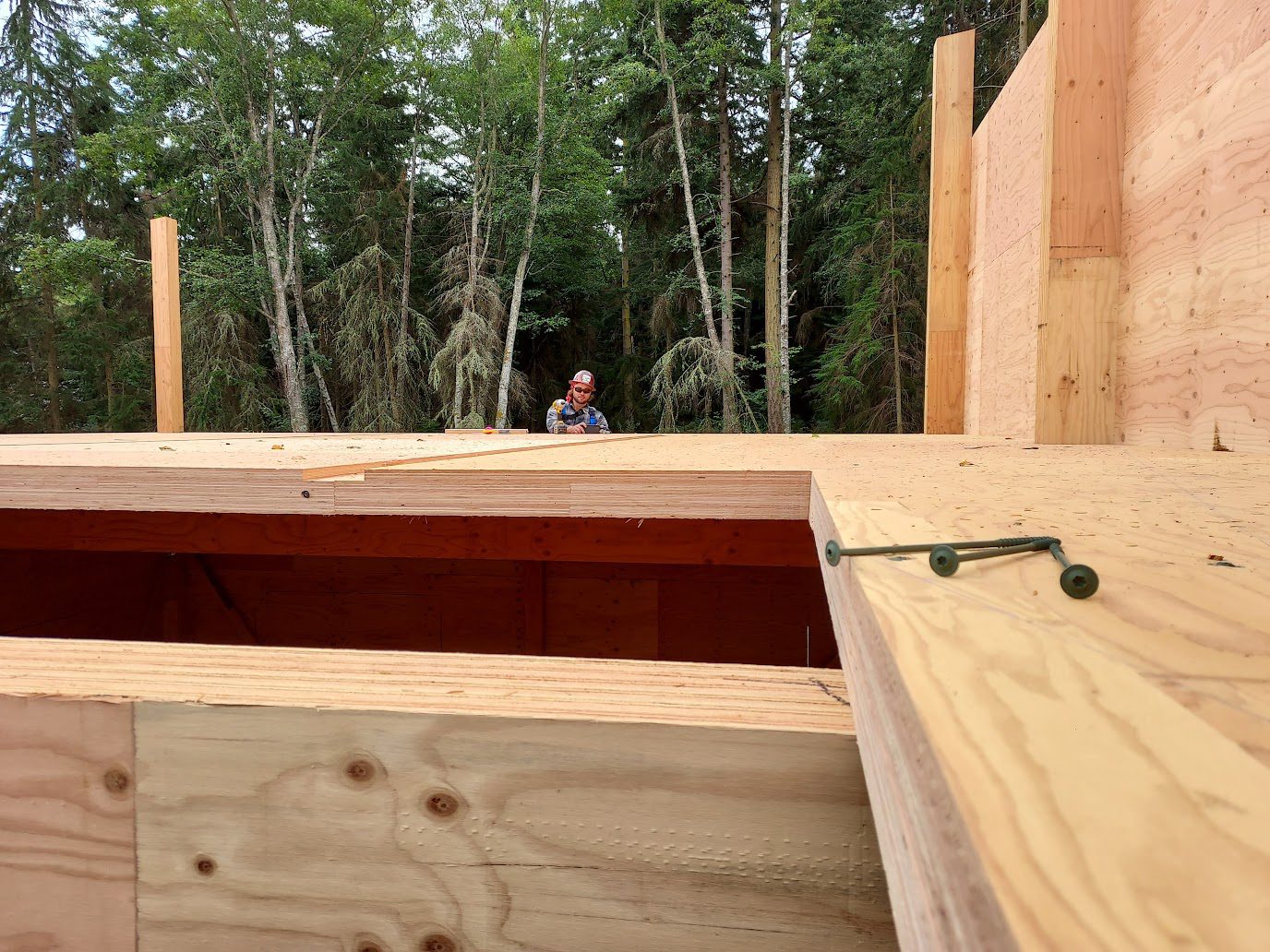
The new STEM Teaching & Learning Facility at Michigan State University has won top honors and awards for the bold Mass Timber design.
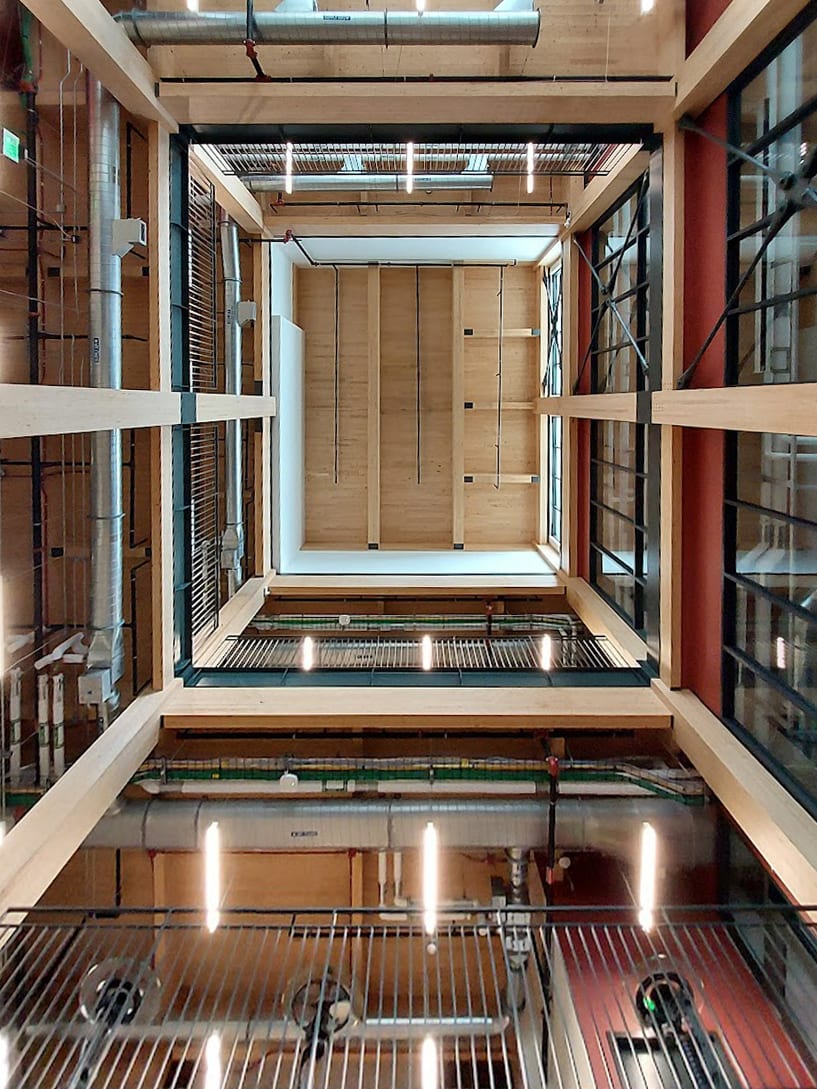
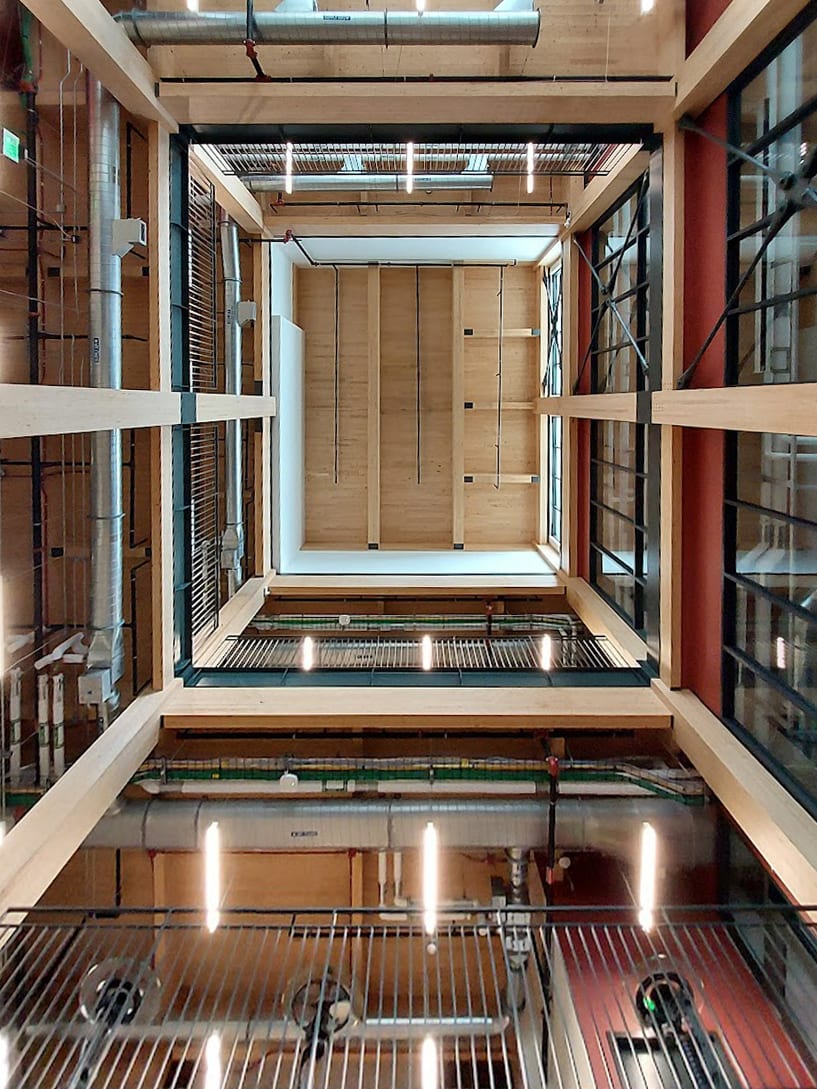
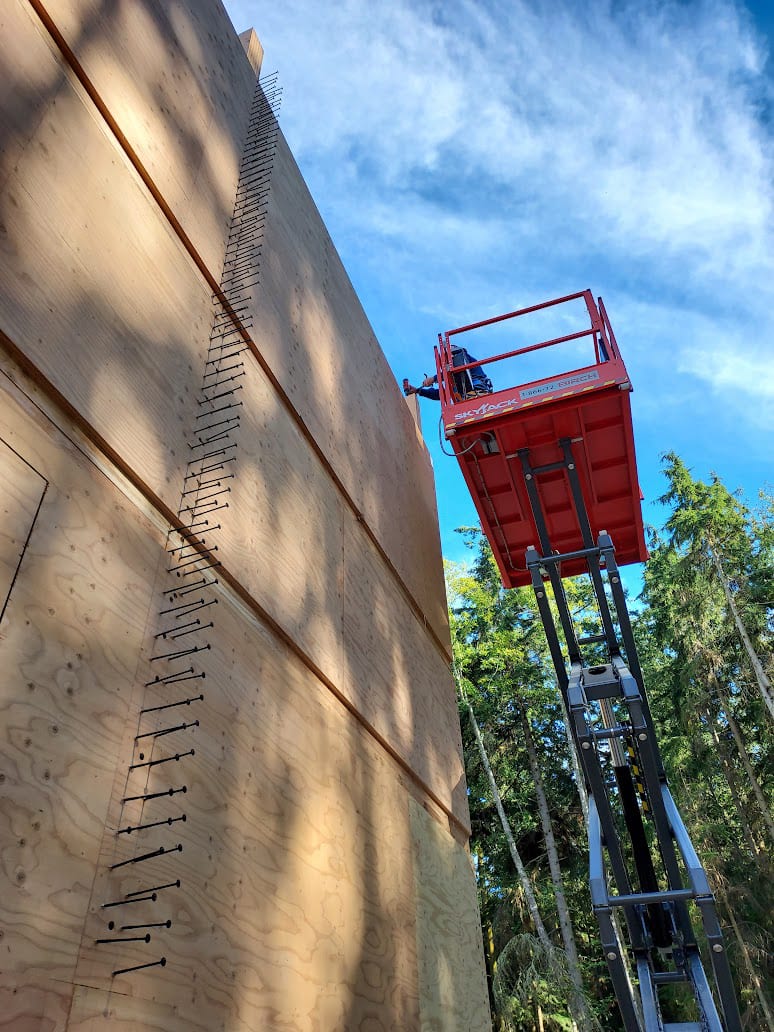
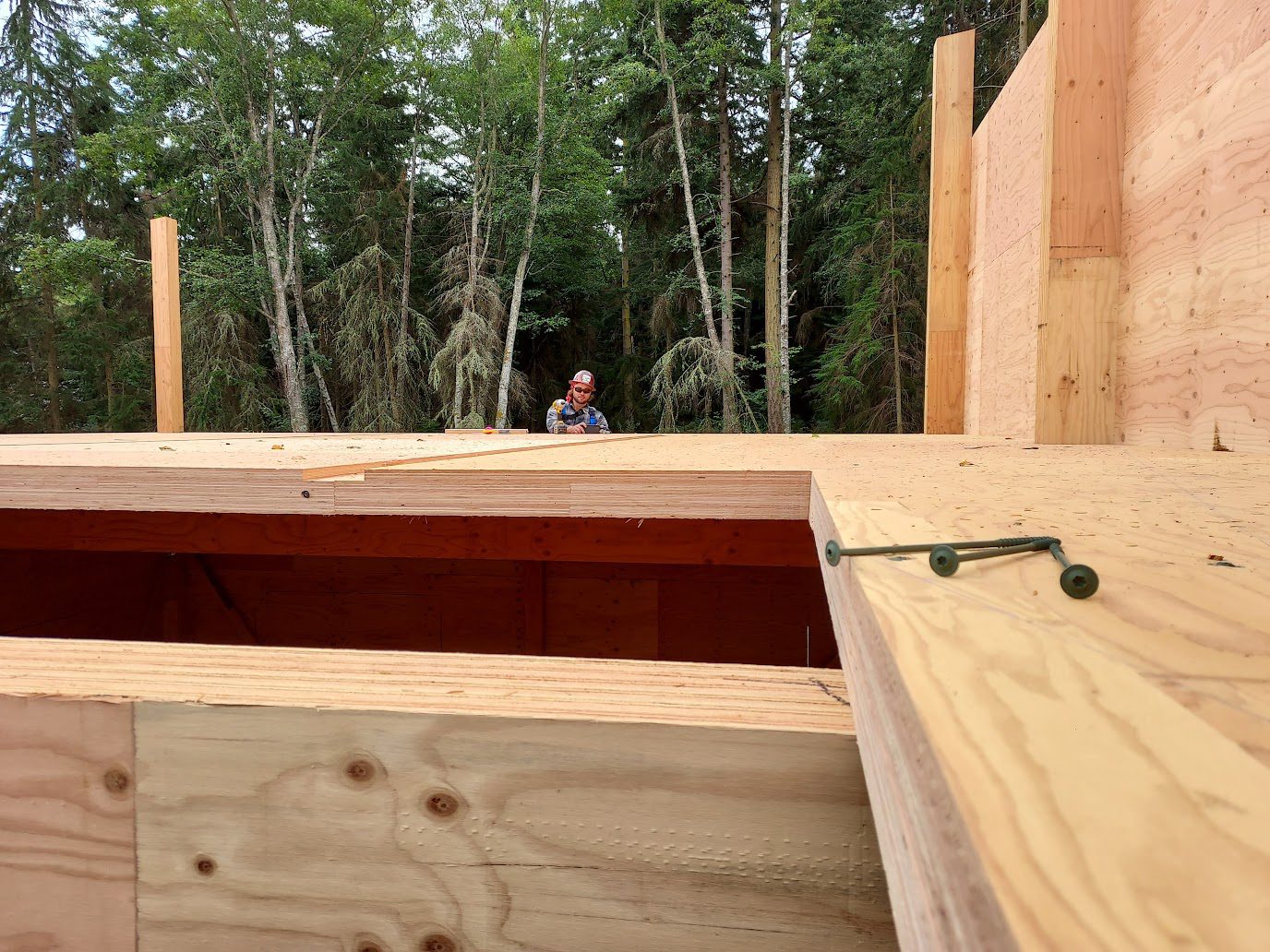
A Growing Demand
There are approximately 15 companies that currently manufacture mass timber material in North America, and the number is growing fast to keep up with rapidly growing demand. In fact, the most significant bottleneck throttling the growth of actual projects coming to fruition in North America is not the lack of demand for mass timber, but rather the ability to design, laminate, and fabricate the panels, beams, and components used to construct entire buildings.
Mass timber is a reinvention of a construction technique that combines the virtues of natural building materials with modern technology. Whether CLT wood floor panels on a concrete or steel framework—or even the framework itself—mass timber can be woven into the design of most structures and provide the natural beauty and biophilic benefits provided by wood. In short, mass timber components and design can supplement, if not entirely replace, building systems otherwise typically designed from concrete and steel.
The material provides significant advantages:
- It is light: roughly half the weight of reinforced concrete that reduces the foundational footprint and super-structure requirements and cost;
- It is strong: A similar strength to weight ratio as steel;
- It is fast: A five-man crew can build a floor a day on a multi-family building;
- It is sustainable: It stores carbon instead of releasing it, and;
- It is renewable: America forests are growing and have an excess of supply, so when a factory on the other side of the world belches out some carbon dioxide, a tree in America can catch it and make it available for the American construction industry by way of naturally grown and sustainably forested wood products.
Water is the greatest enemy of Mass Timber structures. Building envelope fasteners, such as Grip-Deck TubeSeals capable of self-sealing, are important to keep water from leaking through the air barrier.
Screws with specific diameters, thread styles and lengths, are utilized in the design of a mass timber structure.
Pros and Cons
However, every construction material has strengths and weaknesses. Expose concrete to heat or tension and it can fail. Expose steel to fire or salt water and it can fail. Mass timber is no different. Unplanned exposure to fire and water can also lead to failure; however, mass timber can be built to stand the test of time with modern design techniques and attention to detail. The connections required to secure beams to posts and floor panels to beams require specifically engineered and tailored solutions. Large diameter specialty screws are used in abundance throughout, with screw designs contributing in important ways to the overall structural integrity of the building. Fully threaded screws are designed to provide maximum engagement of the screw with the wood fibers along the entire shank length, while partial thread screws are installed to clamp two pieces together. The sequence, spacing, diameter, length, and head style of the screws all need to be considered during the design process.
When it comes to durability, mass timber structures need to be protected during construction as well as for the life of the building. This protection requires robust building envelope design that accounts for thermal performance as well as air and water penetration resistance.
Perhaps the greatest enemy of mass timber is water. Keeping water from penetrating through the air and weather barrier is most easily accomplished with intelligent cladding attachment solutions that are capable of self-sealing when attaching cladding through the layer of continuous insulation, through the air and weather barrier, and into the substrate. Only a few screw manufacturers in the world truly understand mass timber building systems and applications, and these systems need to be optimized to make you work better, faster and stronger.
Construction accounts for almost half of global greenhouse emissions, and mass timber is considered to be the single most relevant technology to bring global greenhouse emissions under control. It is simply a high-tech version of the oldest, most user-friendly and most reliable building material in the history of humanity—wood.
Opening image: CLT wall panels are dropped into place by a crane. Photo courtesy of SmartLam.
Nicholas Benecke is the sustainability engineer for Altenloh, Brinck & Co. Currently, he is doing consultation work out of Germany, as part of Altenloh’s strategic Mass Timber team, bringing European fastening technologies to the burgeoning American market.
Jason Wigboldy is director of product development and engineering for Altenloh, Brinck, & Co US Inc., leading development projects for both the Trufast and SPAX brands of fasteners. For more information, email jwigboldy@trufast.com.