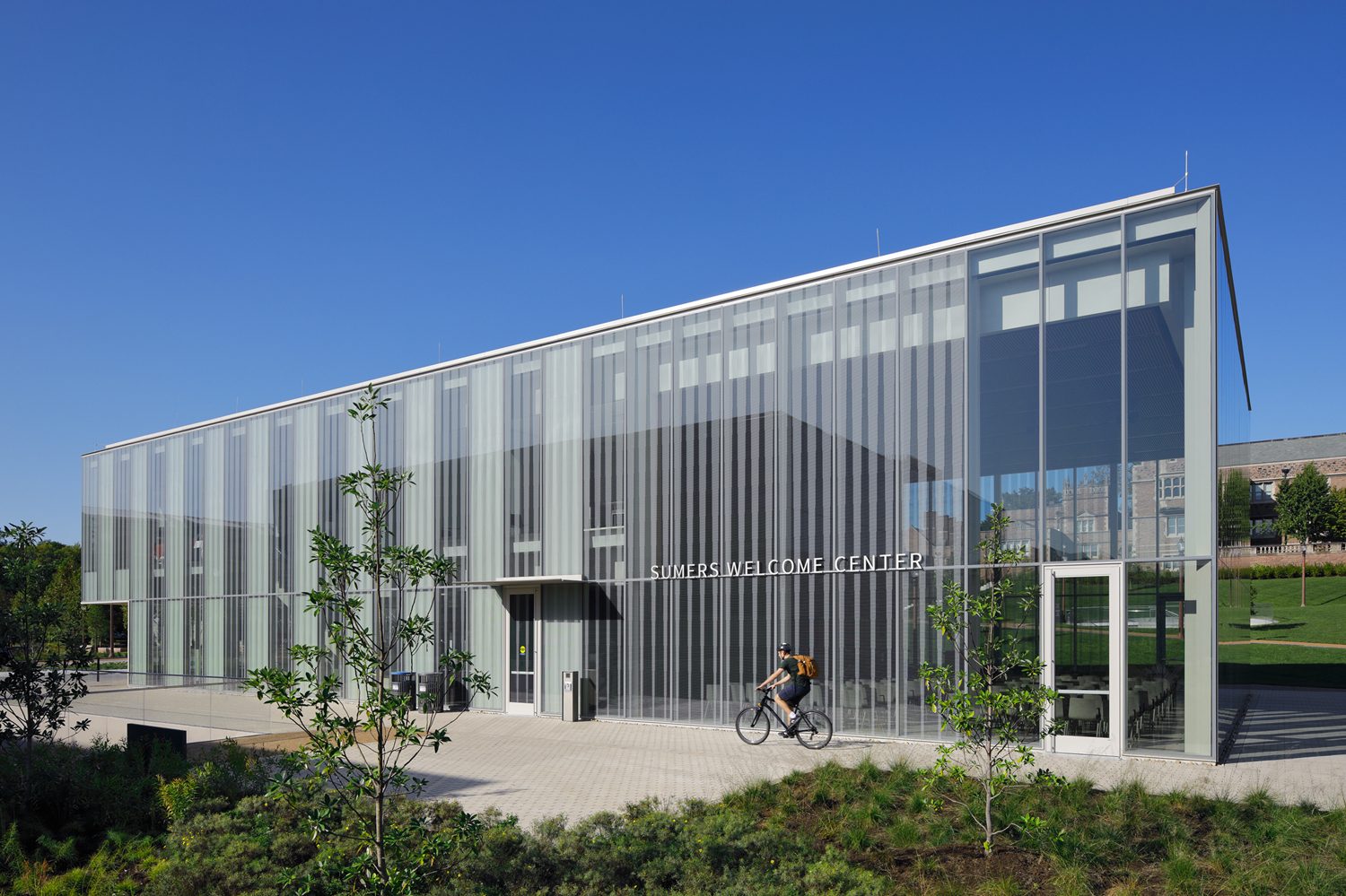
Collaboration is key to installing a proper high performance, weather-resistant curtain wall. By Michael Smalley
Weather-Resistant
Curtain Wall Systems
Curtain walls are one of many methodologies used to affix glass to a building exterior, and are a vitally important component of many modern building projects.
In addition to the aesthetic value it provides, a curtain wall’s primary function is to prevent water and outside air from penetrating the building. A properly built and well-kept curtain wall system will resolutely resist all seasonal weather conditions and keep the building’s interior dry, insulated and comfortable for many decades.
Curtain walls operate as a singular entity, meaning there’s nothing else keeping that area of the building watertight. Given this important function, the stakes are high when it comes to the successful installation of curtain wall systems.
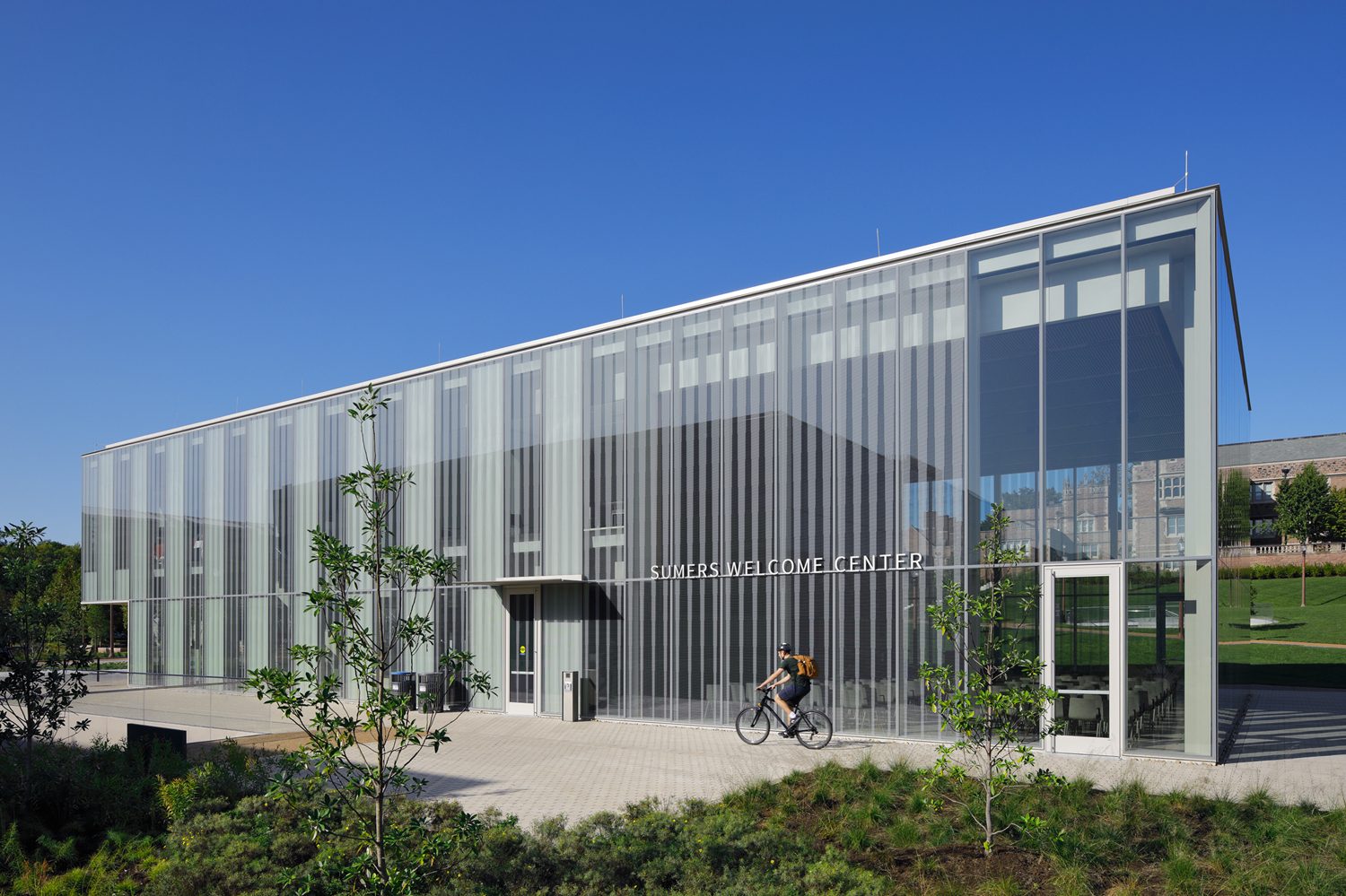
Washington University of St. Louis, East End Enhancements Project. Photo credit Debbie Frankie
Never the Same Thing Twice
Every building project is unique in its own ways. The same truth applies to curtain walls in that no two jobs are quite the same. The inherent challenge of curtain wall installation is having to attach the framing system to an imperfect object like concrete slabs or steel.
Early collaboration among the entire project team is key to meeting this challenge. Getting all stakeholders on the same page is beneficial to understanding the specific requirements of the job and ensuring the curtain wall system being utilized can accommodate the required performance criteria.
A team lacking collaboration may be inclined to select a cheaper curtain wall system that ultimately does not make sense. For example, let’s say a building has an allowable floor-to-floor deflection of 1½ inches, but the curtain wall system being used can only accommodate one inch. If the building ends up deflecting the full 1½ inches, as the performance criteria says it should, then that will lead to water intrusion and a system failure. Improper installation puts primary caulk joints in jeopardy and creates extra wear and tear on perimeter hardware. In principle, placing maximum strain on the materials will lead to premature breakdown and a shorter lifespan than they would have under normal stress or capacity.
This all speaks to why it’s imperative to bring all the project partners together early in the process to properly verify building requirements, system specifications, and make sure the appropriate materials are ordered to get the job done right.
There are two primary options when it comes to selecting curtain walls. A custom curtain wall system originates from domestic fabricators and provides a baseline framework which can be customized based on aesthetics or the performance requirements of a project.
The other option is to purchase a curtain wall system directly from a retailer, including all the parts and pieces that comprise the unit, and assemble it in house. This non-custom option is viable only if the project partners can ensure the stock system will meet the performance criteria.
But in many cases, a custom system is necessary to meet performance criteria and must be planned in such a way that is buildable, sequential and functional. It once again highlights the importance of collaborating before and leading up to installation which requires the careful logistical coordination of significantly large pieces of material.
Project collaboration is achieved through a simple process. The team must first review the criteria of the building, identify and understand the capabilities and limits of the curtain wall system, and align the proper components based on that information. Performance components can be easily evaluated by measuring elements such as thermal performance, dew points, condensation, and glass deflection.
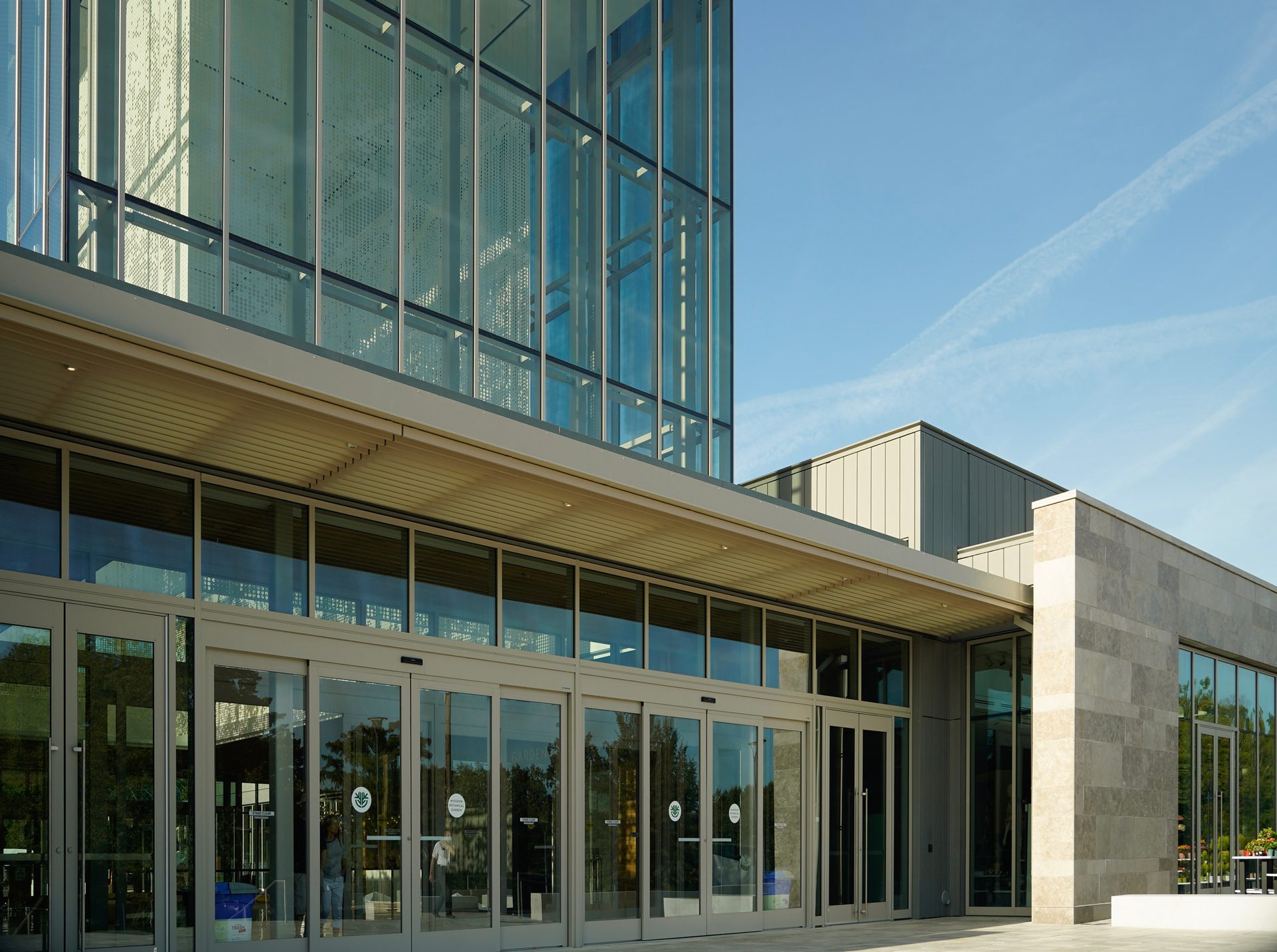
Missouri Botanical Garden, New Visitor Center.
Quality is Key
The constructability of a project is contingent on the quality of collaboration and knowledge sharing among the team. That includes selecting a field glazed or pre-glazed system that’s ideal for the job.
A field-glazed curtain wall system can also be referred to as a cassette wall system, which utilizes an all-aluminum framework that houses the glass units. The glass is placed in the frame on site prior to caulking, tiling and performing related work.
Choosing a pre-glazed system can be ideal for some applications but impractical for others. The wrong system could limit access to certain areas on the building. Scaffolding, crane size, schedule constraints and on-site storage capacity can all create limitations and complicate installation, whereas a pre-glazed system may eliminate some of these constraints and make for a more seamless installation.
It’s important to note that not every curtain wall subcontractor has the ability or means to install a pre-glazed system, depending on the scale of the project. This is a specialized endeavor, and companies may not have relationships with industry partners who can fabricate these types of units.
Glazing installation is arguably the most important part of the curtain wall unit when it comes to weather tightness. Pre-glazed units can be beneficial from a quality control standpoint because the crew during installation is having to contend with windy conditions dozens of stories above ground. These uncontrollable factors can affect the ease of installation and are oftentimes why pre-glazed units are the best option to deliver a strong final product.
Designed With Precision
Because curtain wall systems are designed to move and flex, they have built-in drainage and ventilation capabilities to divert water. Another common curtain wall system is a pressure-equalized system, which simulates internal building pressure to keeps water at bay. Glass, gaskets and seals are also critical to the overall water tightness of the building.
Perimeter seals are one of the most critical points of any curtain wall system. Whether it’s a caulk joint or an engineered transition assembly, using the right product according to the manufacturer’s recommendations will assure a successful installation. The project group should have a plan for testing water tightness and quality control in general which can be achieved through mock-up testing and field testing techniques.
Additionally, these systems should be monitored over time to address long-term maintenance concerns. Caulk joints are the major maintenance item, especially the primary joints that are directly exposed to the elements. Inspecting primary and secondary seals annually is a best practice that will go a long way toward maintaining overall curtain wall system integrity over the long term.
Opening image: University of Missouri, Nextgen Precision Health Institute. Photo credit Michael Robinson.
Michael Smalley is the director of pre-construction at IWR North America, one of the longest-standing contractors in the nation, specializing in building enclosures since 1895. He has worked for IWR for more than 10 years, serving there previously as Director of Business Development and Preconstruction Manager. Smalley is a graduate of Missouri State University where he earned degrees in construction management and real estate finance, and since 2015 has served as a board member for the Building Enclosure Council of St. Louis. For more information, contact msmalley@iwrna.com.