Enabling a Greener Future by Minimizing Embodied Carbon in Exterior Wall Systems
Utilizing low embodied carbon materials in building retrofits to reduce harmful greenhouse gas emissions. By Teal Rooks
According to a 2023 report published by the Rocky Mountain Institute titled “Transforming Existing Buildings from Climate Liabilities to Climate Assets,” the United States has more than 97 billion square feet of commercial buildings and 244 billion square feet of residential buildings, and 80 percent of them will still be in service by 2050. In fact, many of them will still be here in 100 years. The same report states that the existing global building stock is responsible for 28 percent of the world’s carbon emissions, highlighting the importance of making significant upgrades to the structures that are already here.
Any discussion about global climate change requires an analysis of total carbon emissions. For the construction industry, there are two types of carbon that need to be considered: operational carbon and embodied carbon.
Operational carbon is the amount of carbon that is released during the in-use phase of a building. According to UL², this includes the use, management, and maintenance of a product or structure. Architects, designers, contractors, and building owners are calculating the operational carbon generated by a building when they determine its anticipated energy efficiency over time.
Embodied carbon is the carbon emitted during the processes that take place prior to and during the actual creation or retrofit of a building, including the “extraction of raw materials, manufacture and refinement of products, transport, the building phase of the product or structure, and the deconstruction and disposal of materials at the end of life.”
While operational carbon is a critical consideration in the climate change conversation, it should not be the sole focus. The embodied carbon of building materials and construction practices must also serve as focal points for the industry. If done right and in a timely fashion, the positive impacts will be felt globally.
The building envelope plays a major role in the energy efficiency and performance of a structure. Exterior wall systems, like any other product, require raw materials to create and command time and effort to transport and install. Therefore, they have an impact on both the operational and embodied carbon of a building. This must be considered when specifying them for a structure.
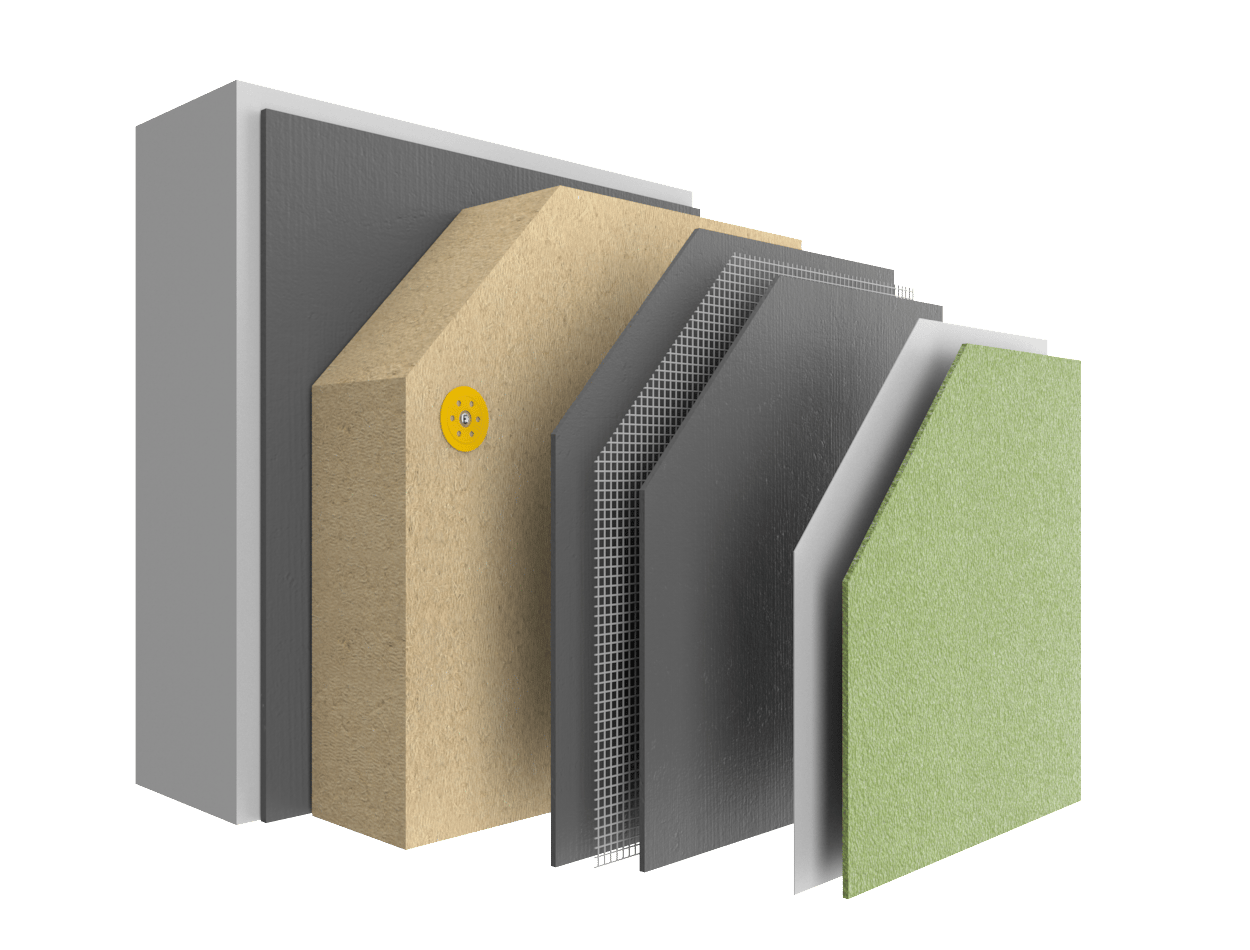
Climate-neutral external thermal insulation composite system with renewable insulation material. Using timber removes carbon dioxide from the atmosphere as it grows, and the growth phase significantly exceeds the carbon dioxide emitted during the manufacturing process, reducing the carbon footprint.
*System is currently not available in North America
Embodied Carbon in Building Materials
The embodied carbon of a building material can be broken down into four categories: production, transportation, installation, and disposal. To meet global carbon reduction goals, building materials manufacturers can have the greatest impact on the equation by focusing on production.
The process starts before production even begins on the manufacturing plant floor, because the handling of the raw materials that are used to make building products plays a key role. Therefore, it is important for manufacturers to source sustainable raw materials. For example, are raw materials coming from a source close to the manufacturing plant? The closer to the source, the less carbon expended to transport them. Is the manufacturing facility recycling packaging, diverting waste away from landfills, or sourcing energy from renewable sources? All these measures can effectively decrease the embodied carbon in a product.
Some manufacturers are applying these very concepts to their manufacturing practices to effectively reduce the embodied carbon within their products and systems.
Exterior Wall Systems: Where Can We Reduce?
Generally speaking, structural materials, such as reinforced concrete are ranked at the top of embodied carbon contributors for a building. But when it comes to non-structural exterior wall systems, such as EIFS, insulation generates the greatest amount of embodied carbon, making it the focus for efforts to reduce embodied carbon in these systems.
RMI reports: “Manufacturers can consider ways to substitute various materials in their current product lines to achieve carbon storage. For example, EIFS is commonly used in retrofits. In Europe, carbon-storing EIFS with wood fiber insulation is available. Similarly, North American EIFS manufacturers could offer a similar product by replacing rigid foam or mineral wool with wood fiber. Offering carbon-storing EIFS in North America is now more viable, because the first U.S.-based wood fiber insulation manufacturer is opening in Maine in 2023.” It is important to understand, however, that the referenced wood fiber insulation is an ASTM E84 Class B material for fire protection and should only be used where Class B materials are permitted.
Choosing these greener insulation options can help reduce the embodied carbon of the overall exterior wall system. Wood fiberboard insulation or cork board insulation are both carbon-storing for the duration of their lives and have no net emissions, reducing the overall environmental impact of an exterior wall system.

RMI Report compared the embodied carbon emission of the components of five different retrofit assemblies – this data can be used to pinpoint components that would benefit from redesign efforts to lower embodied carbon.
https://rmi.org/insight/transforming-existing-buildings-from-climate-liabilities-to-climate-assets/
Deep Energy Retrofits: Making the Most of Existing Buildings
With existing global building stock being responsible for 28 percent of the world’s carbon emissions, deep energy retrofitting is at the top of the priority list for reducing carbon and greenhouse gas emissions in the construction arena. By retrofitting an existing building over constructing a new one, the embodied carbon on a given project has already been reduced by 50 to 75 percent. It is the easiest and most effective way to minimize embodied carbon. Deep energy retrofits offer all the benefits of reducing operational carbon and have a significant impact on embodied carbon by simply being a retrofit.
The RMI report states that the best deep energy retrofits are “akin to putting a sweater, hat, and windbreaker on the exterior of a building.” The report includes two retrofit case studies in the Boston area: a six-story brick building and a two-story wood-framed building. Both retrofits used insulation materials that rank in the mid-range for embodied carbon. Even when sourcing a mid-range embodied carbon material, the study found that the embodied carbon needed for the deep energy retrofits would be offset by the operational emissions reductions in less than four years. After those four years, the buildings’ negative impact with regard to carbon emissions becomes significantly less than its pre-retrofit era. In short, using more sustainable materials can have a sizable impact on a building’s overall carbon footprint in a relatively short period of time.
The Boston buildings are just two examples, but they both demonstrate how effective carbon-friendlier materials are for retrofit construction, particularly at the building envelope level. Conducting these types of retrofits across thousands of residential and commercial buildings throughout the world would have a substantial impact on climate change goals. It would help meet the sustainability targets that the industry has established for 2030 and 2050.
Insulation is not the only area of the building to examine, however. Making strategic selections for accompanying building materials and choosing sustainable systems for the entire retrofit can shorten the amount of time it takes to offset the carbon used during its construction. Other areas include the entire retrofit wall assembly, new windows and doors, and new roofs (both roofing materials and insulation), HVAC systems, lighting, and more.
According to RMI, this is the ultimate goal: “By combining low-embodied-carbon materials and carbon-storing materials with retrofits that dramatically reduce operating emissions, existing buildings and neighborhoods can be transformed from carbon emitting to carbon storing.”

Environmental Product Declarations (EPDs) provide a means of measuring the overall lifecycle impact of a product and the information to compare different materials and choose the best product fit for their environmental goals.
https://www3.stocorp.com/l/60712/2023-05-31/n3zbdm
Environmental Product Declarations
According to the International EPD System, an Environmental Product Declaration1 transparently reports objective, comparable, and third-party verified data about products and services’ environmental performance from a lifecycle perspective. Finding a manufacturer whose products are backed by EPDs gives specifiers the confidence they need when designing sustainable buildings. This allows them to capture important data about the products used to create greener buildings such as global warming potential including biogenic carbon emission or eutrophication potential.
Not all manufacturers’ products have EPDs. It is a time-consuming and expensive effort. However, the value of EPDs is that they show the good and the bad of the product tested, offering an unbiased, thorough, third-party take on its sustainability and long-term performance on a building. Choosing a manufacturer who has made a dedicated effort to obtain EPDs for their products shows a commitment to consumer transparency. For specifiers, it provides the ultimate peace of mind when making product decisions based on embodied carbon and sustainability.
Reducing Embodied Carbon: Taking the Comprehensive Approach
Reducing the embodied carbon of building materials requires manufacturers to take a close look at all phases of the product’s life cycle before it ends up on a building – from sourcing, to production, through to construction. Therefore, this process must consider the entire cradle-to-grave lifecycle of a product or a wall assembly.
Manufacturers can do their part by sourcing high-quality raw materials obtained in close proximity to the manufacturing plant to minimize transportation emissions. It is also key to continuously identify new ways to reduce the embodied carbon of products or source alternate materials that are carbon storing. For wall assemblies, that means identifying possible alternative insulation materials or cladding that takes less energy to create but delivers on the performance requirements.
It is imperative for owners, developers, and policymakers to contemplate a deep energy retrofit as opposed to demolishing a building and starting from scratch. Salvaging and restoring what already exists in the built environment will have a much greater payoff compared to tearing down and beginning construction on something new.
As Carl Elefante, FAIA, FAPT, principal emeritus with Quinn Evans Architects once said, “The greenest building is one that is already built.”
Sources
- “Environmental Product Declarations.” The EPD | EPD International, https://www.environdec.com/all-about-epds/the-epd.
- UL Solutions - https://spot.ul.com/blog/embodied-vs-operational-carbon/.
Images courtesy of Sto Corp.
Teal Rooks is environmental health safety and ISO Manager for Sto Corp. She has more than 10 years of successful experience in driving environmental and safety initiatives. Currently, she focuses on integrating pollution prevention into business performance initiatives and manages the internal auditing program. In addition to ensuring a safe and healthy workplace, Teal works to continually improve the quality and environmental systems by managing the sites conformance to ISO:9001 and ISO:14001 and is passionate about product stewardship.
Zak Veres is the sustainable development manager for Sto Corp. For more than 18 years, he has held positions in R&D and product management focused on restoration and sustainable practices. Veres also holds a degree in International Business.