xxxxxxx. By xxxxxx
xxxxx
xxxx
Innovation in flashing technology has happened many times throughout the years. By Andrew Irvine
The Evolution of
Flashings
xxxxxxxxxxxxxxx By xxxxxxxx
h2 - xxxx
h3 - xxxx
H1 headline
Flashing technology has undergone quite a bit of innovation over the years, driven by demand for higher performance, longer service life and better energy efficiency. Recent advancements have led to significant improvements in its durability, temperature range and adhesion properties.
Initially dominated by asphalt-based products, the market has seen a steady shift toward more advanced materials, like butyl and acrylic, each offering distinct advantages. There are also options for liquid-applied flashings and brand-new clear, acrylic offerings that add even more choices for high-performance building envelopes. Understanding this evolution is crucial for selecting the right flashing material for a given project, especially as the construction industry increasingly prioritizes sustainability and reliability.
Asphalt Flashings
Traditionally, asphalt-based flashing was the go-to choice for construction. These tapes, made from modified bitumen, share properties with rubberized asphalt used in roofing applications. However, asphalt flashings have several significant drawbacks. They tend to be messy to install, requiring careful handling and priming for a strong bond with certain substrates, like oriented strand board and concrete. This added step can slow down the installation process and increase labor costs.
Moreover, asphalt flashings suffer from limited temperature resilience. They can lose their adhesive strength when temperatures drop below 50 degrees Fahrenheit and often fail to bond effectively below 40 degrees Fahrenheit. Conversely, at extremely high temperatures, asphalt can soften and begin to flow, compromising the integrity of the seal.
Butyl Flashings
The development of butyl flashings marked a significant step forward in the performance of flashing materials. Comprising a butyl rubber core, these tapes provide improved flexibility, making them more suitable for a wider temperature range. Butyl flashings can remain flexible in cold weather and are more stable under high temperatures than their asphalt counterparts are. Their adhesive properties also allow for a better bond with challenging substrates, and they can be adjusted during installation, which can be particularly helpful for complex detailing.
Acrylic Flashings
The most recent advancement in flashing materials is the introduction of acrylic-based tapes. Engineered for superior durability and temperature resistance, acrylic tapes are not only used in construction, but also in industries requiring high-performance adhesives, such as automotive and aerospace. Acrylic adhesives are known for their viscoelastic properties, which enable them to flow into surface inconsistencies to create a strong bond while maintaining enough flexibility to accommodate movement within the structure.
Acrylic flashings resist UV damage and heat degradation far more effectively that asphalt or butyl. Advanced cross-linking of the polymer chains enhances an acrylic tape’s molecular stability, allowing it to retain adhesive strength for years, even in harsh environments.
The transition from asphalt to butyl and, finally, to acrylic has been driven by the construction industry’s need for materials that can provide more reliable performance across a broader range of conditions. This evolution reflects a growing recognition of the benefits of higher-quality flashings in maintaining the overall integrity and energy efficiency of building envelopes.
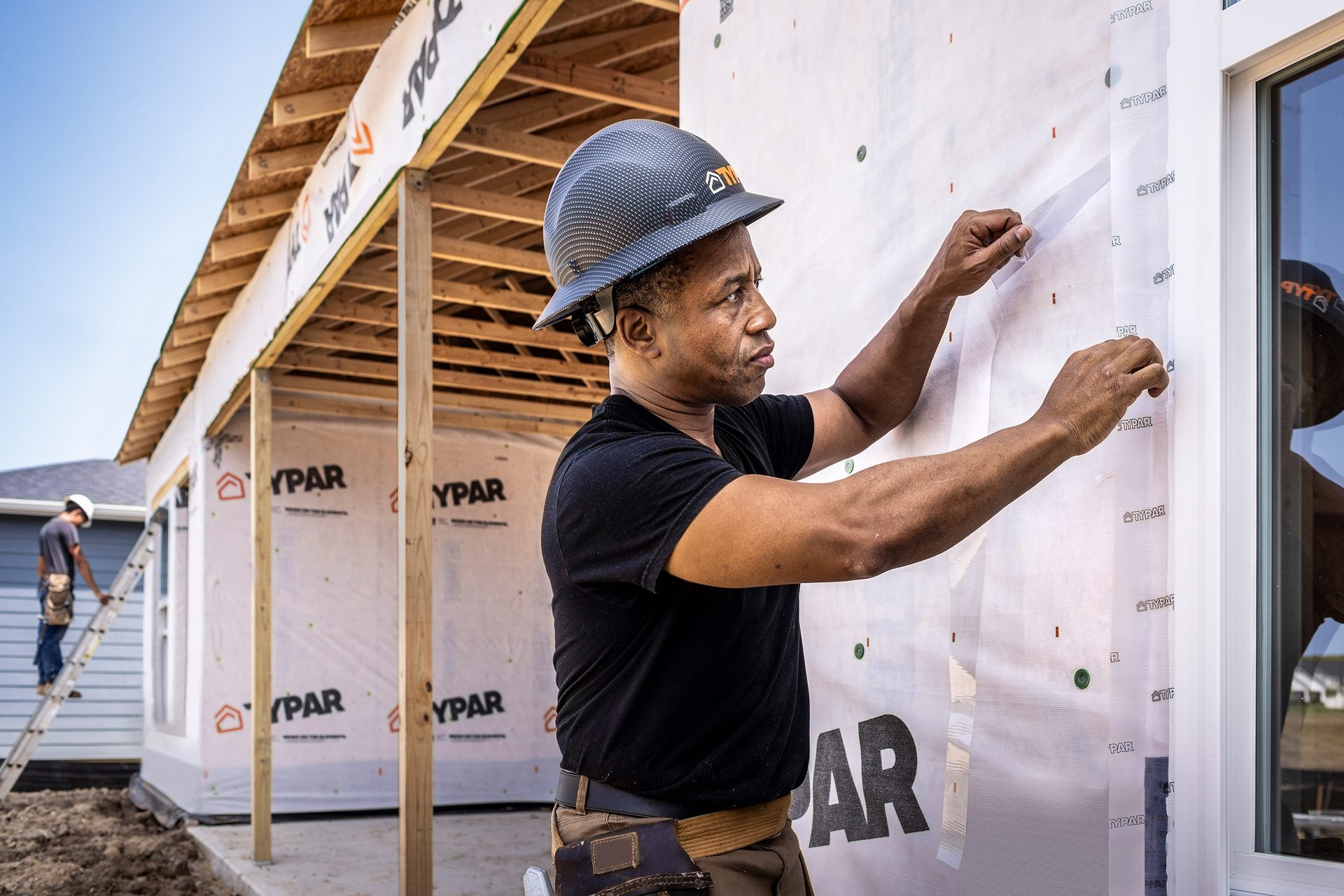
xxxxxxxxxxxx
Need to update flourish table
Traditional Flashings vs. Liquid-Applied
Choosing the right type of flashing can make a significant difference in both the ease of installation and the long-term performance of the building envelope. Traditional flashings, typically in the form of sheet or tape, have been the standard for years, while liquid-applied flashings offer an alternative that can be advantageous in certain applications.
Sheet or tape flashings are widely used for sealing areas like windows, doors and roof penetrations. Their ease of use and straightforward application make them suitable for a variety of standard construction details. Traditional flashings can also be pre-formed for specific uses, such as around corners or penetrations, which can reduce installation time and labor costs.
However, traditional flashings can present challenges when working with irregular or complex surfaces. The need for a consistent, tight seal can be difficult to achieve in areas where surfaces are uneven or access is limited. In such cases, multiple layers of flashing tape may be required, which can complicate the installation process.
Liquid-applied flashings, on the other hand, are designed to conform to irregular shapes and hard-to-reach areas. They can be particularly useful in complex transitions, such as around curved or non-standard window frames, pipe penetrations and unique architectural details. The ability to form a seamless, monolithic membrane provides superior protection against water intrusion in these challenging conditions.
When choosing between traditional and liquid-applied flashings, it is important to consider the installation method. Traditional, self-adhered flashings require both hand application and pressure from a J-roller to activate the adhesive bond, adding steps to ensure durability and water resistance. This is necessary because the adhesives are pressure-sensitive. In contrast, liquid-applied flashings, which can be applied by hand or spray in a single coat, form a seamless, flexible barrier without additional rolling. This streamlined process not only saves time, but also reduces labor complexity, making liquid flashings particularly effective for irregular surfaces.
However, liquid-applied flashings require a certain degree of expertise to install properly. They also require specific curing times, which can vary depending on environmental conditions. These factors make liquid-applied solutions more suitable for projects where their advantages outweigh the added complexity and installation time.
Selecting the appropriate flashing material depends on the specifics of the project and the characteristics of the building envelope. For standard window and door installations or straightforward roofing applications, traditional sheet or tape flashings are typically sufficient and offer a cost-effective solution. In contrast, when dealing with irregular shapes, complex transitions or areas with high potential for water exposure, liquid-applied flashings may be the better choice due to their superior ability to create a continuous, watertight barrier.
The decision between traditional and liquid-applied flashings ultimately comes down to balancing the benefits of ease of installation with the need for a more robust seal. Understanding the properties and limitations of each type ensures that flashings are applied where they can offer the most benefit, protecting the building’s envelope and extending its service life.
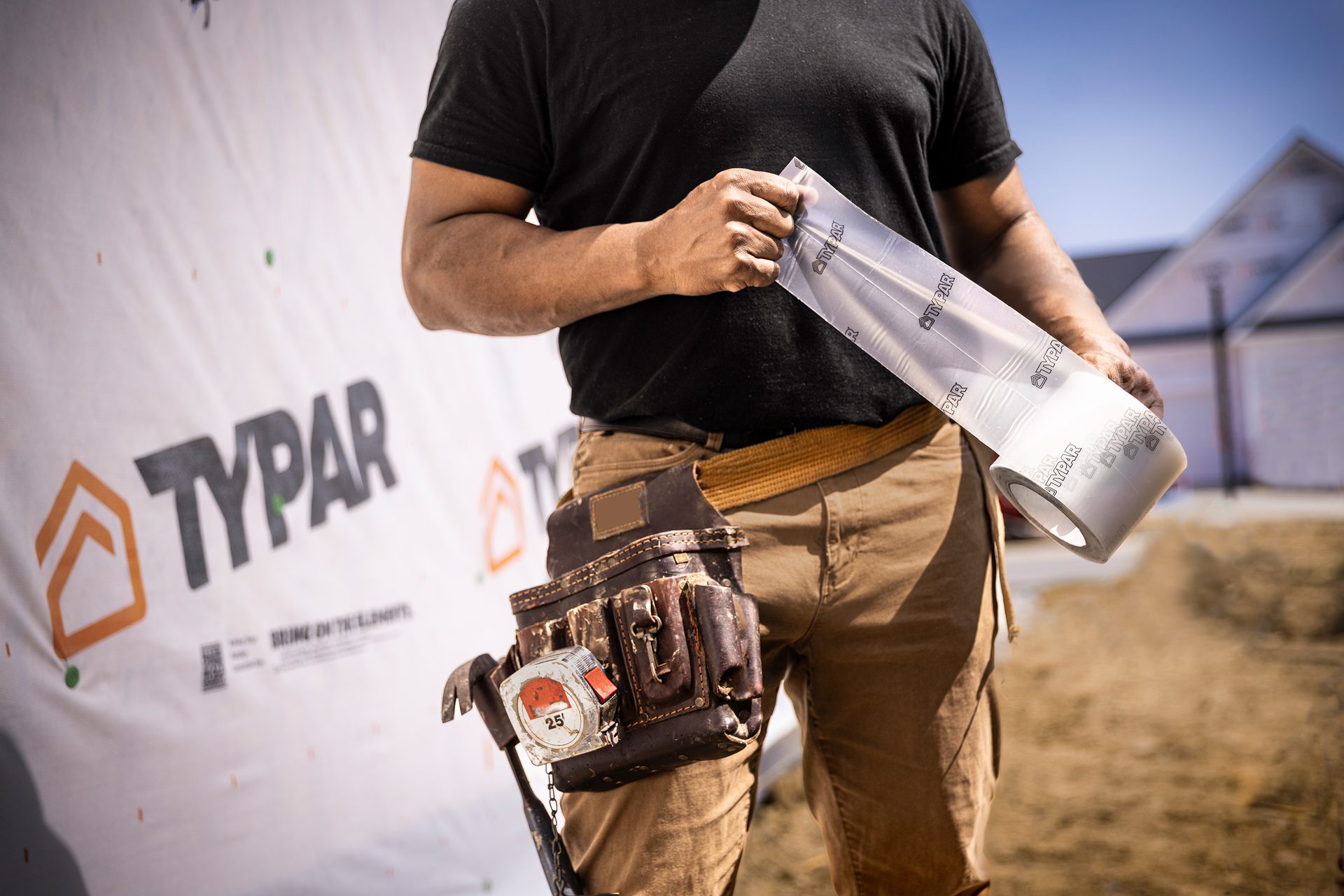
xxxxxxxxxxxx
The Emergence of Clear Flashings
The very recent introduction of clear flashing products into the marketplace represents yet another significant innovation in the construction industry, offering a practical solution for challenges that often arise during window and door installations. This game-changing product was developed in response to emerging building code changes that require better visibility of the nail and screw-fin patterns during window installations and inspections. Traditional, opaque flashings can obscure these patterns, requiring multiple steps to complete the installation process.
Improperly installed windows and doors can be a significant and often hidden expense for homebuilders due to both immediate repairs and long-term issues, like energy loss and structural damage. These issues represent common callbacks for builders, placing them high on the list of frequent post-construction concerns. By allowing a clear view of the nailing fins, clear flashings streamline the inspection process, helping installers and inspectors verify that fasteners are properly placed without needing to remove or adjust the tape. This visibility reduces the time and labor associated with reworks, cutting down costs and minimizing delays.
Clear flashings also improve quality control, accountability and transparency among tradespeople. By allowing for visual confirmation of proper nailing patterns and flashing application, they align with a “show your work” approach to construction that is especially valuable amid current labor shortages, as it helps maintain high standards while also supporting sustainability goals.
The advantages extend beyond visibility. Because clear flashings utilize the latest advanced, acrylic adhesive, they provide superior waterproofing, self-healing properties around fasteners and excellent temperature flexibility. They also offer high UV resistance and comply with industry standards, ensuring long-term performance and protection against water infiltration.
Ultimately, clear flashings not only enhance the efficiency and accuracy of installation, but also help prevent costly callbacks and improve overall project quality.
The evolution of flashing materials reflects the construction industry’s broader drive toward greater efficiency, durability and performance. As materials have advanced from asphalt to butyl and now to acrylic-based tapes, builders have gained tools that enhance installation quality and building longevity. Incorporating modern options, like clear flashing, into a project’s approach addresses challenges like inspection visibility and weatherproofing while simplifying the process. By understanding these innovations and selecting the right products for each application, construction professionals can ensure that projects meet today’s demanding standards with fewer callbacks and improved overall outcomes.
References
- xxxxxxxxxxx
- xxxxxxxxxxx
Images courtesy of TYPAR Construction Products.
Andrew Irvine is a senior product manager at TYPAR Construction Products. He has extensive experience in the building and construction industry, including global product management, national account management and finance. Irvine is responsible for the building and construction portfolios, including the TYPAR product line.
Andrew Irvine is a senior product manager at TYPAR Construction Products. He has extensive experience in the building and construction industry, including global product management, national account management and finance. Irvine is responsible for the building and construction portfolios, including the TYPAR product line.