Some truths and myths about the history of stucco. By The Stucco Manufacturers Association
Stucco: So Controversial. Why?
Stucco:
So Controversial. Why?
Stucco is simple: sand, cement and lime. How can something so simple have so much controversy? The first fact is that stucco is used all over the world, but the confusion about stucco seems to be only in North America. This reason is simple. Cement stucco on framing is popular only in North America. It is not new to this continent, but is being re-invented because, who makes money on basic sand and cement?
Why So Much Attack On Stucco?
The U.S. Census Bureau puts out data on new homes every year. Currently, stucco is the number one cladding on all new homes, with 28 percent market share. Being the king of the mountain makes you the prime target. Being that stucco is essentially generic or a commodity makes it even riper to pick on. Who will defend stucco? The manufacturers of sand and cement will tell you that stucco is a small market to them. Most say about 2 to 3 percent of their sales are stucco-related. Consider that roads, bridges and foundations alone use significantly more sand and cement than stucco. Basically, we’re told stucco is not worth putting resources into promotion. So, why then is stucco number one? This is the double-edged sword; stucco is a commodity and in some areas the cost is hard—if not impossible—to beat. This is mainly in the southwestern U.S., where stucco is far higher than 28 percent market share.
But Stucco Only Works Out West
This is 100 percent false. Stucco is used around the world and many countries have far more than 28 percent stucco market share. Those that claim stucco only works in regions with no rain are mistaken. While it makes a good sound bite, it is simply not true. There are hundreds, if not thousands, of projects still performing after decades—even in cold or wet climates. The adjustments to make stucco work on framing and in cold/wet climates is not that challenging and does not need to be that expensive. However, many consultants will disagree, and it should not be surprising that they have elaborate designs that require special details that come at a price.
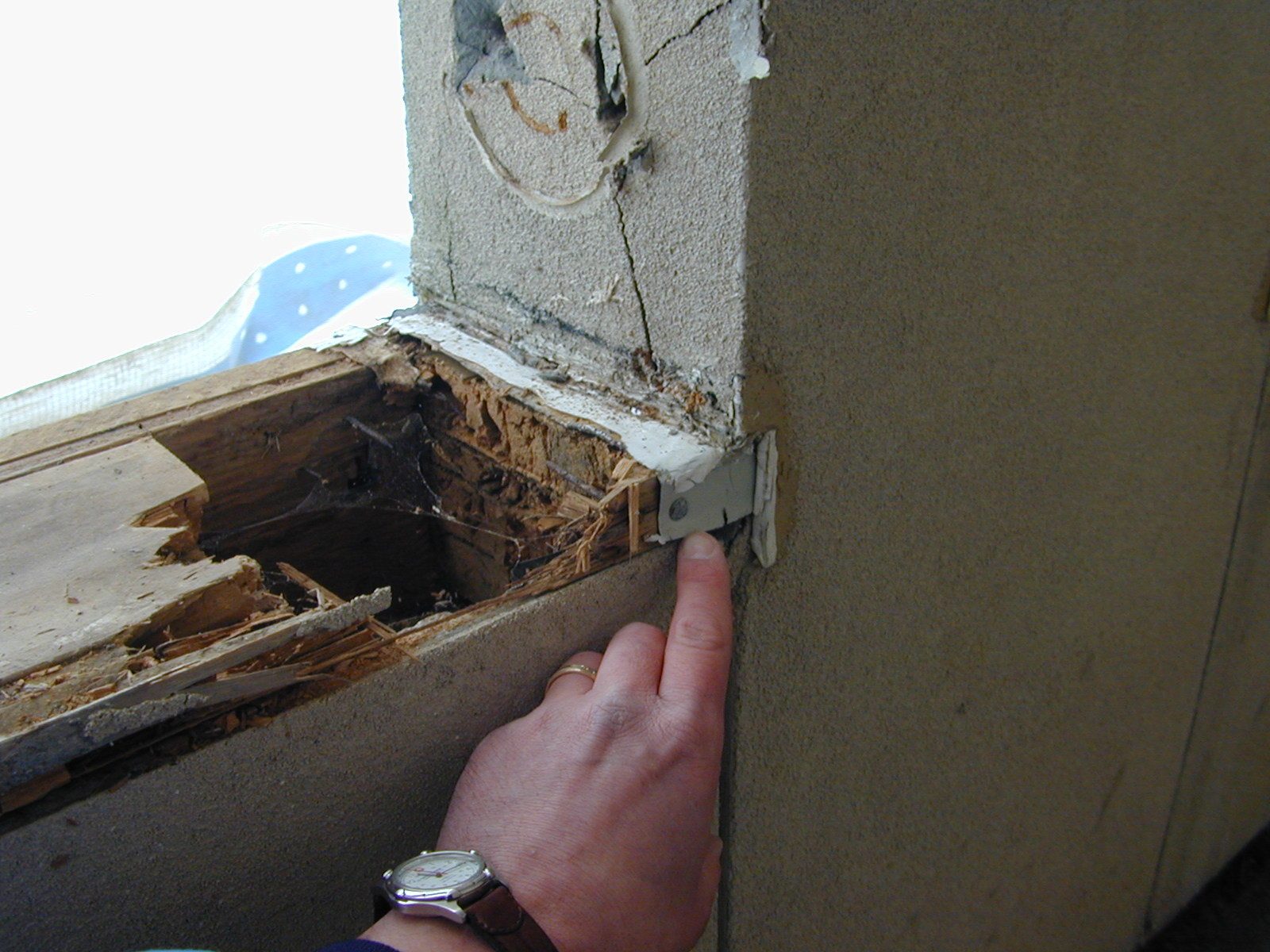
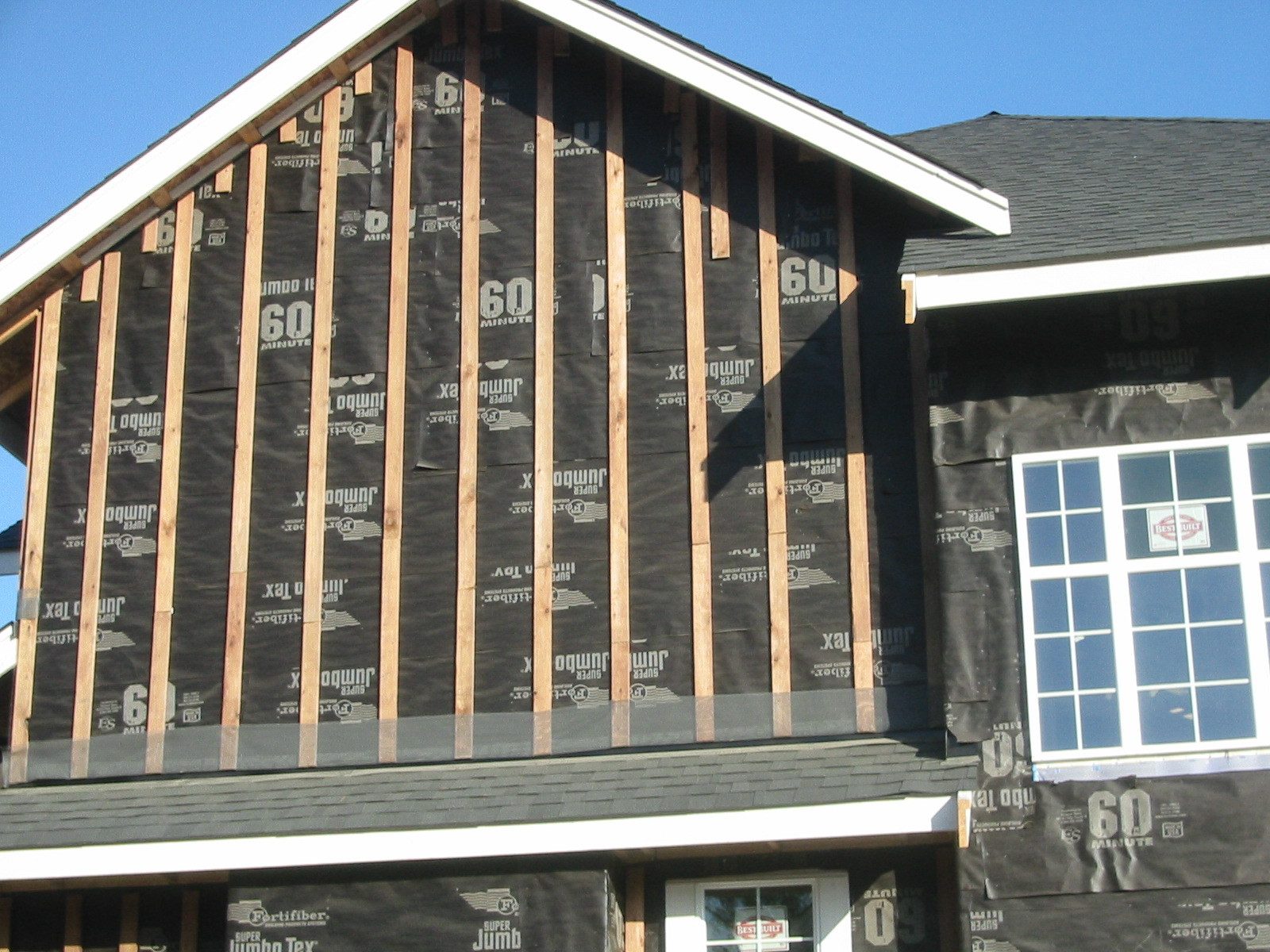
Reservoir Cladding
The popular term “reservoir cladding” is meant to disparage stucco or verify the need for high-priced consulting. Cement absorbs water; we can see it in the sidewalks or on the freeway overpass. It rains and the cement soaks up water and turns darker. This does not mean stucco is porous. Studies, tests and countless reports conclude that properly mixed and applied cement stucco will not let water pass through the membrane. It has been found that water typically only gets 3/8 inch to a 1/2 inch into the membrane and is then stopped. Cement swimming pools prove this statement. They are made of basic Portland cement and they hold water. As with stucco, water penetrates a little and is then stopped. This makes sense, as cement does not know or care whether it is in pool or on a wall.
Cement plaster will absorb and can hold water so it can act as a reservoir, but so what. The sun comes out and that moisture in the cement is driven off to the exterior. While some experts claim it is also driven to the inside of the structure, that is not true. I have investigated hundreds of stucco buildings—some with water damage. Here is another fact: when water damage is found on a stucco-clad framed wall, it is rarely—if ever—the field of the wall having an issue. What typically occurs is water damage around penetrations, such as windows. The leaks can almost always be traced back to bad or missing flashing.
Today, it is common to have leaks due to too much flashing. How can this be? It is about complexity. The fact is that most workers in the field are minimally trained, even in flashing. A complicated flashing program is like asking a mechanic familiar only with lawnmowers to build a Ferrari from the parts on the floor. Even with well-written instructions, it is not likely to work out.
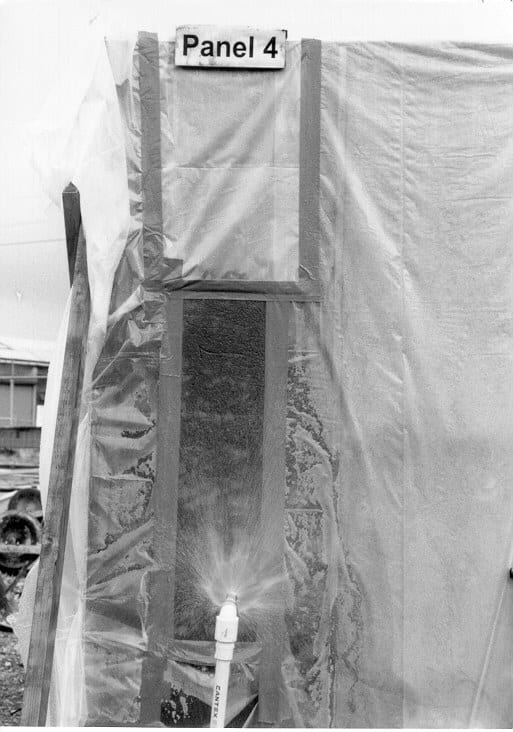
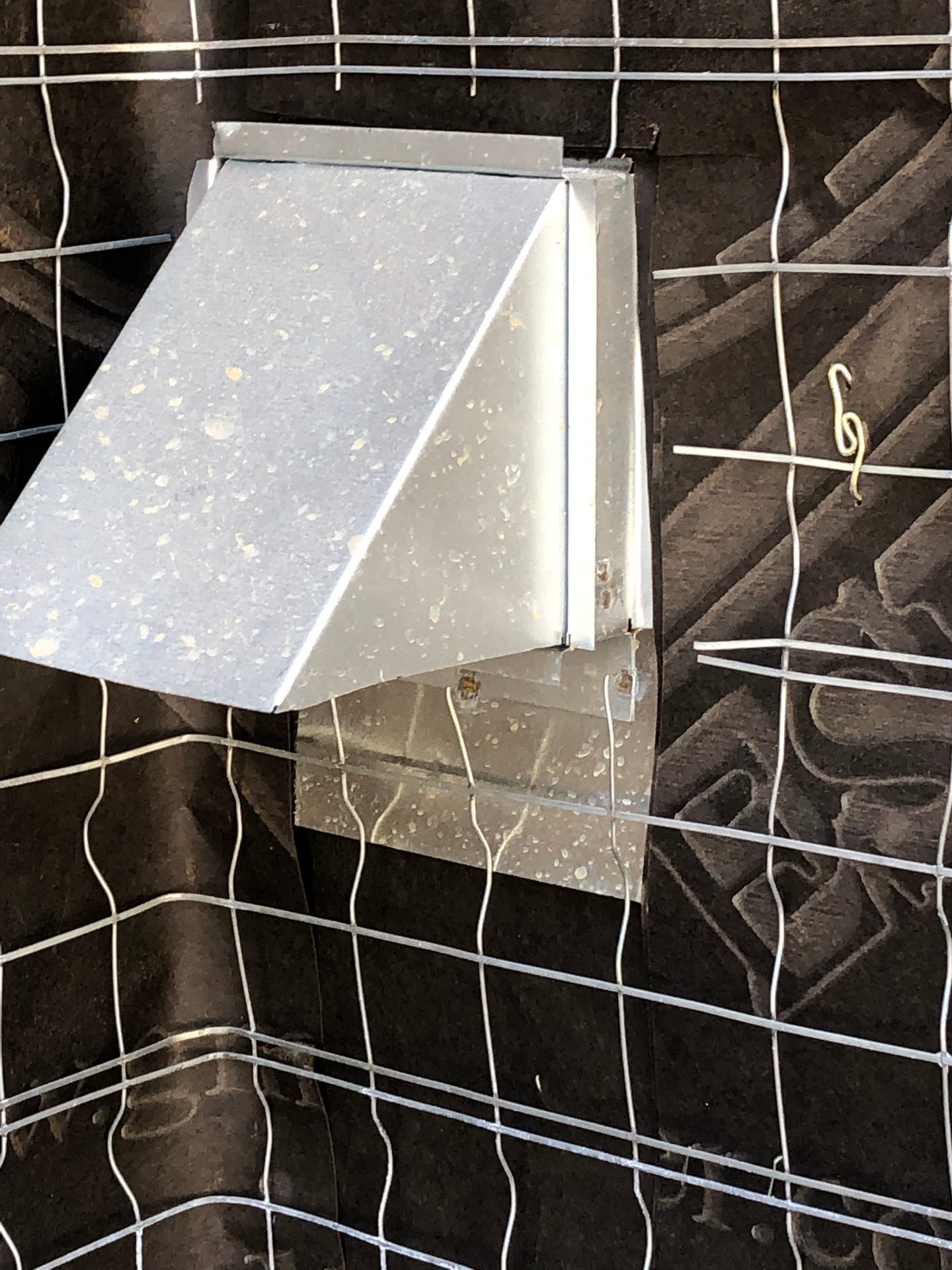
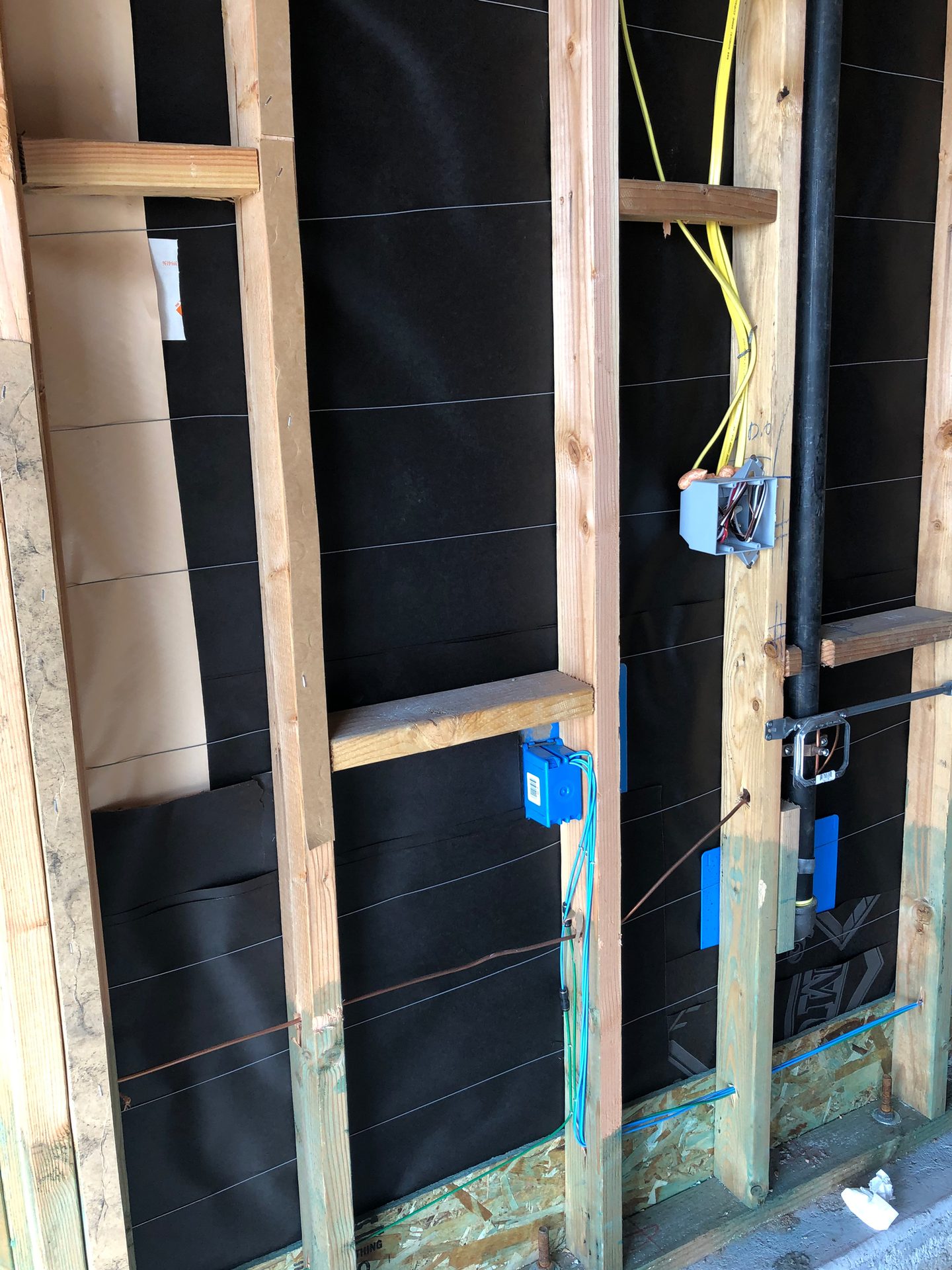
The Leaky Condo Crisis
Many say this all started with the “leaky condo crisis” in western Canada. I recently heard a young building scientist opine about this and say the code-mandated ventilation space is what saved them.
Yes, leaks stopped with the code-required ventilation but this also coincided with industry attention to provide some basic flashing procedures for windows and doors. I can remember giving classes and teaching lathers how to flash a window. I am convinced flashing, because they were doing nothing before, was accountable for much of the success. In fact, Seattle did exactly that, and some attention to flashing and putting off the ventilated air space resulted in a huge reduction in wall leaks.
Even the testing was skewed a bit to support ventilation. Canada funded research on ventilation on stucco cladding back in the 1990s. I was there. They were certain that the code-mandated 3/4-inch cavity was the solution for the leaky condos. They tested, looking to validate a foregone conclusion, as it was being introduced into city code. When the data came in, it was disappointing, to say the least. This 3/4-inch gap did next to nothing to help with drying the wall. The traditional wall was not far behind in drying. The final report was issued and concluded that there was a “significant” drying benefit, yet provided no actual numbers for comparison. It makes logical sense that air is not going to flow freely behind a cladding. This space is essentially stagnant, unless forced by high winds or a fire. This is why building departments have been reluctant to accept ventilated claddings on fire-rated walls.
Two Layers of WRB?
Many building scientists claim the reason the building code initially mandated two layers of water-resistant barrier was for extra water protection or, really reaching, ventilation. Both are wrong. The Uniform Building Code first mandated two layers in 1982. The industry had no issue with water or ventilation at that time. Consider that the requirement was only for stucco over wood-based sheathing. There is a strong clue as to why two layers were introduced into the code. It was noted that cement plaster tended to crack more when placed over wood sheathing. It is hard to believe, but stucco was routinely placed over open studs with line wire prior to 1985.
Walt Pruter was a respected stucco guru and consultant to the code bodies and ASTM. He passed away almost two decades ago. I wanted to know why we did two layers over wood sheathing. He explained that someone found out that adding a second layer of grade D paper reduced cracking in stucco over wood-based sheathing. He was instrumental in getting that section into the code.
Drainage Mat
Now, to make the case for why a drainage mat is a good idea for stucco. Hint: it is not to enhance ventilation behind stucco. The reason the second layer of black paper worked to minimize cracking and why it was only needed for wood sheathing is basic science and common sense. Wet cement is applied to the asphaltic paper, and the underlying wood sheathing can become slightly damp and then swell. While this is not harmful to the wall, it is enough to fracture green or uncured cement plaster. Adding a top or second layer of paper creates a small gap to keep the base layer of paper dry, preventing the wood sheathing from warping. Drainage mats will do the same thing as the top layer of paper and help minimize cracking. Plus, they provide a clear and better drainage path. What is wrong with that?
Stucco can work in all climates, even if put on framed walls. There are regional practices, and most are beneficial to a stucco wall, as the contractors putting it up learn. If it fails, they can be sued, so it is in their best interest to make it work. Leaks are the prime fear. The reason and the route with lawyers, experts and insurance is another article for another time. Just know that stucco does not have to be overly complicated or costly to work. Stucco is simple but complex.
Opening Image Credit: ChuckSchugPhotography / iStock / Getty Images Plus via Getty Images.
Remaining images courtesy of SMA.
xxxxxxxx