One product that can help save time and money and reduce waste. By Jennifer Annas
Transforming Job Site Efficiency: One Drywall Corner at a Time
One Drywall Corner at a Time
EFFICIENCY:
JOB SITE
Transforming
In today’s often unpredictable landscape, speed and ease have never been more important when it comes to time and materials in the construction industry, as we navigate the challenges that come with limited timelines, workers and resources. That’s why it’s imperative to think beyond how we can make products better and instead address how to transform the processes through technology. This will help us streamline installation, reduce waste and help keep schedules on target. This is especially important for specific skilled trades, like drywall finishing, that require expertise and time to master.
Specified widely across the construction industry, drywall presents a simple solution for creating clean divisions across a multitude of interiors, as opposed to other more labor intensive applications. More affordable products offer water and fire resilience, as well as insulation for buildings year-round. Yet, just because it’s a simpler solution doesn’t mean it’s easy to install.
Drywall installation that achieves a monolithic aesthetic requires skill—especially when it comes to finishing corners, which involves a seamless blend across multiple sheets of drywall and other surfaces. Most commercial contractors estimate that using traditional methods and materials, such as metal to finish drywall corners, can take about 800 to 1,000 linear feet per man, per day. Available on the market since the 1950s, metal beads have presented some challenges. Heavy metal cornerbeads are sometimes damaged in transit and on the job site, can be harder to cut by hand, and in some cases require time-intensive installation that requires nails or screws, mesh tape and heavy coats of mud.
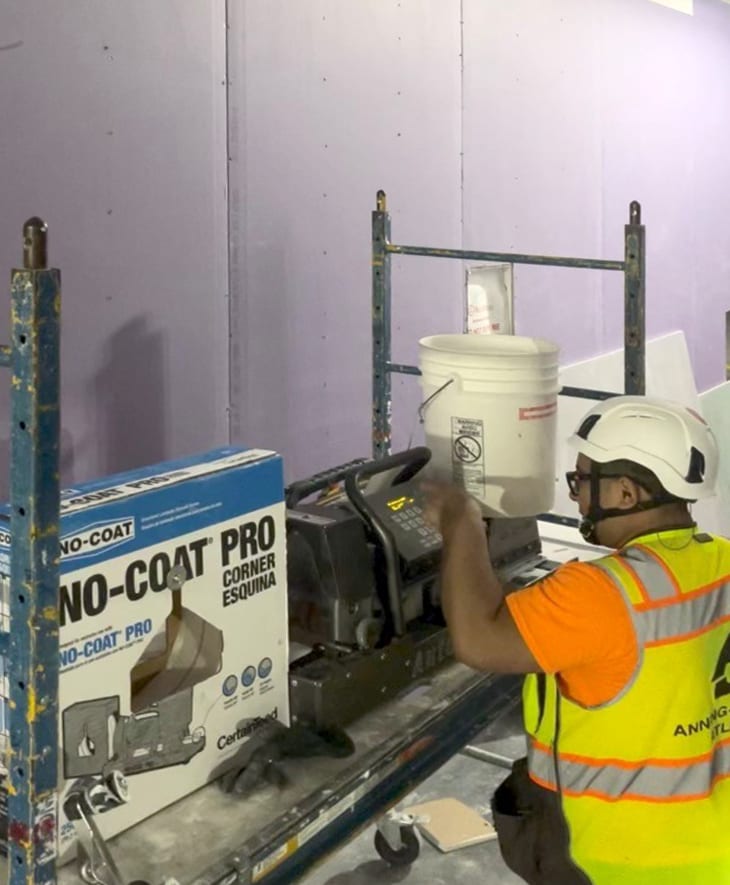
The Evolution of Cornerbead
The drywall industry has always been deeply committed to partnering with contractors by developing innovations to save time and money and reduce waste, which benefits both the project’s bottom line and the planet. Consequently, some companies pushed for innovation in the development of newer product portfolios that would help streamline the process of finishing drywall corners in commercial and multi-family projects with a high volume of “cookie-cutter” spaces.
In the late 1990s, paper-plastic cornerbeads were introduced with a co-polymer core that delivers impact resistance. Ten years later, pre-cut standard sticks were brought to the market.
In 2006, an inventor in the drywall market came to the industry with the idea to incorporate automation within the product. As a former drywall finisher himself, he understood the setbacks that corners could lead to on a job, and so, with this first-hand experience in mind, a deep development phase was entered for two years, finally launching an automated system for custom cutting corners of any length or angle. Paired with a line of structural laminate corners and combined with water-activated corners, this product marked the first time custom length automated cornerbeads were made on the job site, enabling an improved flexibility.
Since its introduction into the market, this product has been refined for optimal performance and job site support, and the feedback has been incredible.
The Benefits
Overall, most contractors have reported close to 35 percent savings in productivity and time through the use of new beads. Savings are also made in terms of materials. Commercial contractors typically factor in 12 to 15 percent waste on cornerbeads, as fittings—such as windows and doors—often do not come in the standard lengths in which traditional corners are available. Some products cut waste down to about 3 percent by cutting the cornerbeads to the desired length and automatically applying the joint compound. Most of the time, it takes just two coats to fill and finish.
Regardless of all these benefits, we as an industry understand that skills that have been cultivated in the trade can be frustrating to modify and difficult to adapt to. Time on the job site is money, and people are often creatures of habit and can be slow to embrace new things.
Innovations have the power to change how we work and help curtail the complications that come with industry shortages—an issue that may never be completely resolved. In an era where working smarter and not harder is vital to saving costs on labor and materials, embracing technological advancements can be the difference between finishing a job on time or running behind.
Images courtesy of CertainTeed Gypsum.
Jennifer Annas is a segment marketing manager at CertainTeed.