THE AFFORDABILITY, RESILIENCY AND SUSTAINABILITY OF ICFs. By Frank Gordon, Assoc. AIA
Build Better
Retail
Build Better Retail
xxxxx. xxx
xxxxx
xxxxxxxxx
xxxxxxxxxxxxxxx By xxxxxxxx
h2 - xxxx
h3 - xxxx
H1 headline
Retail construction is a complex balancing act, demanding cost-effectiveness, durability, and aesthetic appeal. With growing emphasis on energy efficiency, disaster resilience, and sustainability, material choices have become critical. Insulating concrete forms are emerging as an alternative to traditional methods. As demand for sustainable, cost-effective practices grows, ICF is transforming the retail construction landscape.
ICFs consist of hollow EPS foam blocks connected by high-density polypropylene webs, which double as finish attachment points. These blocks, stacked and filled with reinforced concrete, create a robust, energy-efficient, and insulated exterior envelope that exceeds building code standards. ICF integrates structure, thermal and moisture barriers, fire resistance, sound attenuation, and finish attachment into one system. This streamlined approach makes ICF a high-performance solution for retail construction.
The Challenge: Affordability Without Compromise
Cost remains the primary concern in retail construction. While ICF was once seen as costlier, its price has become competitive due to advancements in contractor proficiency, stable material costs, stringent building code requirements and expedited construction.
ICF combines wall assembly and construction, insulation/thermal barrier, and sheathing into a single step, reducing labor needs and construction schedules by up to 35 percent. Its weather-resistant properties further minimize delays, enabling faster project completion and quicker returns on investment. Manufacturer data shows that ICF cuts labor hours for exterior walls by 20 percent. Additionally, ICF’s strong insulation and structural integration lower HVAC requirements, significantly reducing equipment and installation costs.
A 2023 study by the National Ready Mixed Concrete Association found that ICF walls were as much as 10.3 percent more cost-effective than CMU when factoring in labor, materials, and overhead. The continuous insulation (R-24+) and minimal air infiltration of ICF walls can reduce heating and cooling costs by up to 40 percent - a significant saving for retail spaces where HVAC accounts for 50 percent of energy use. These energy savings, combined with lower maintenance costs and reduced risk of structural damage, make ICF an attractive option for retail developers.
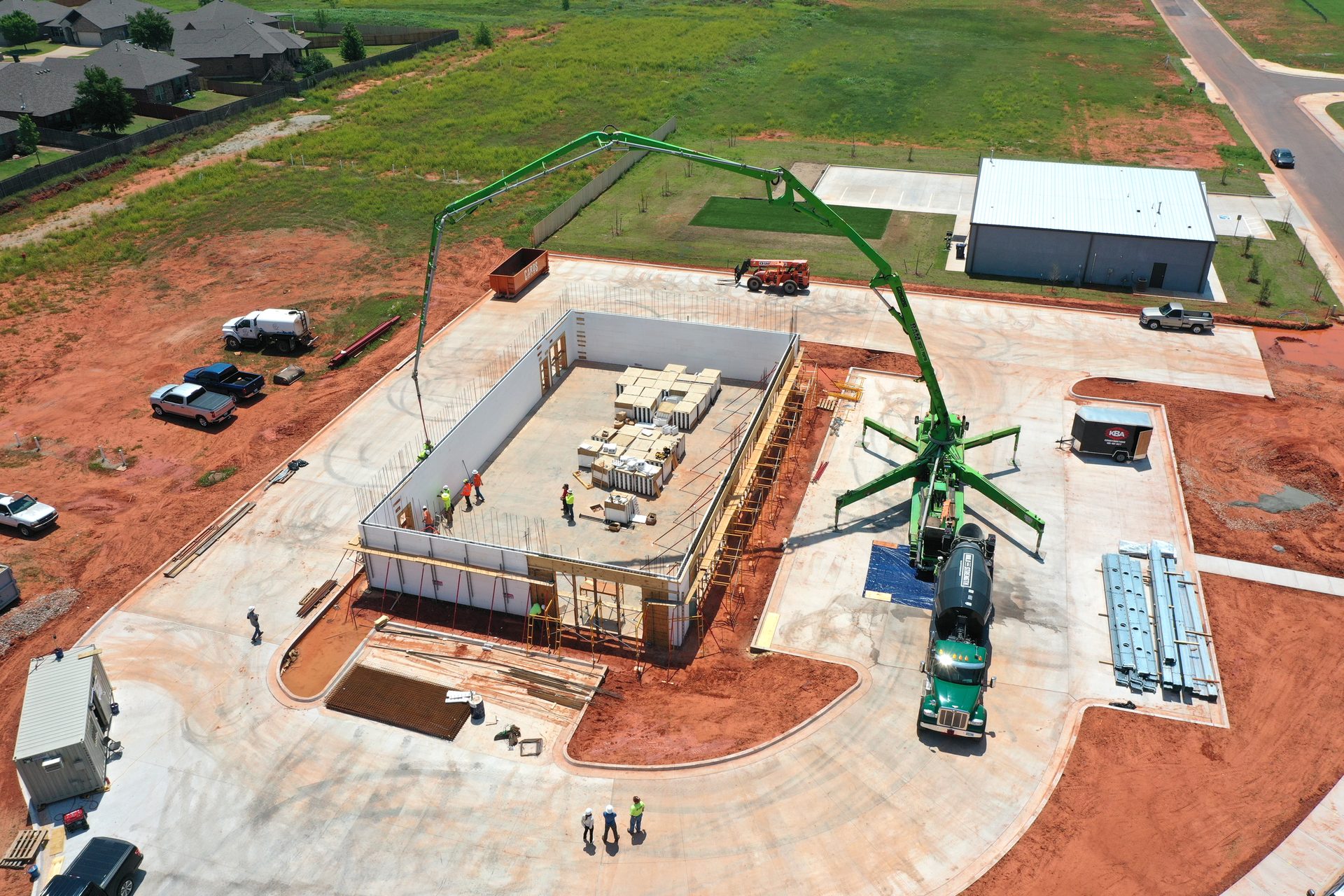
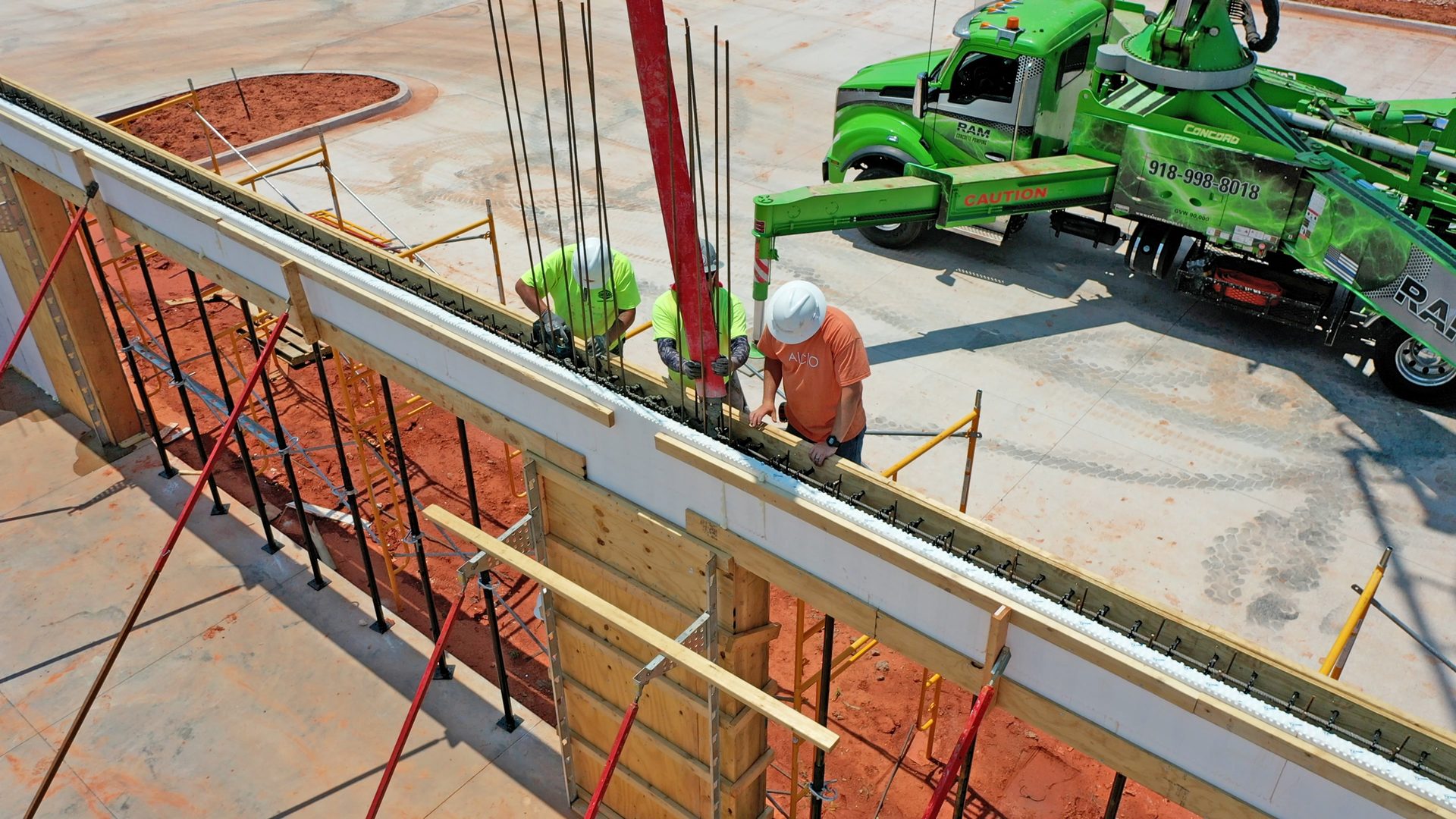
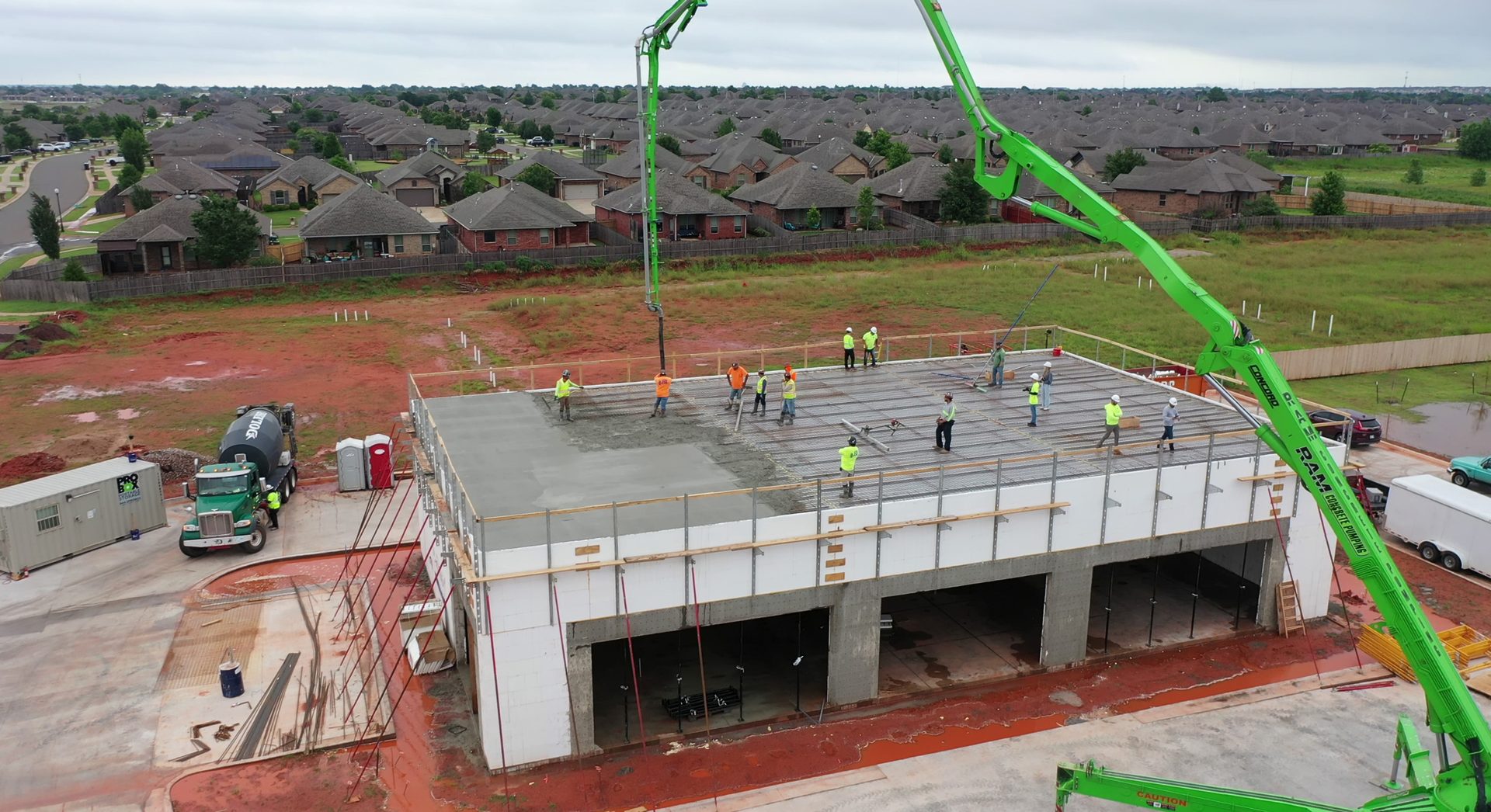
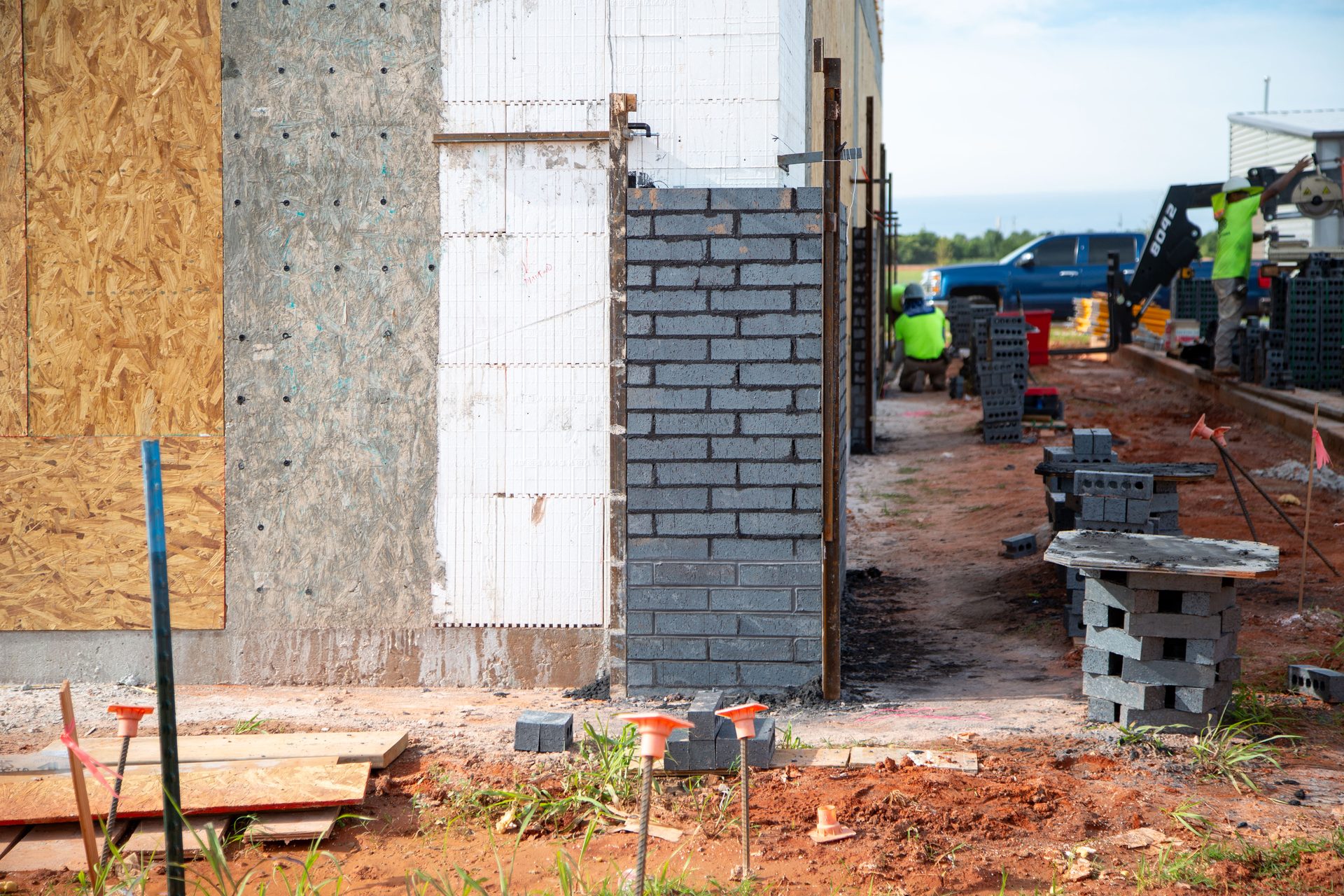

A New Jersey office designed by Gensler, featuring a NanaWall HSW60 single-track system | Photography by Garrett Rowland Photography
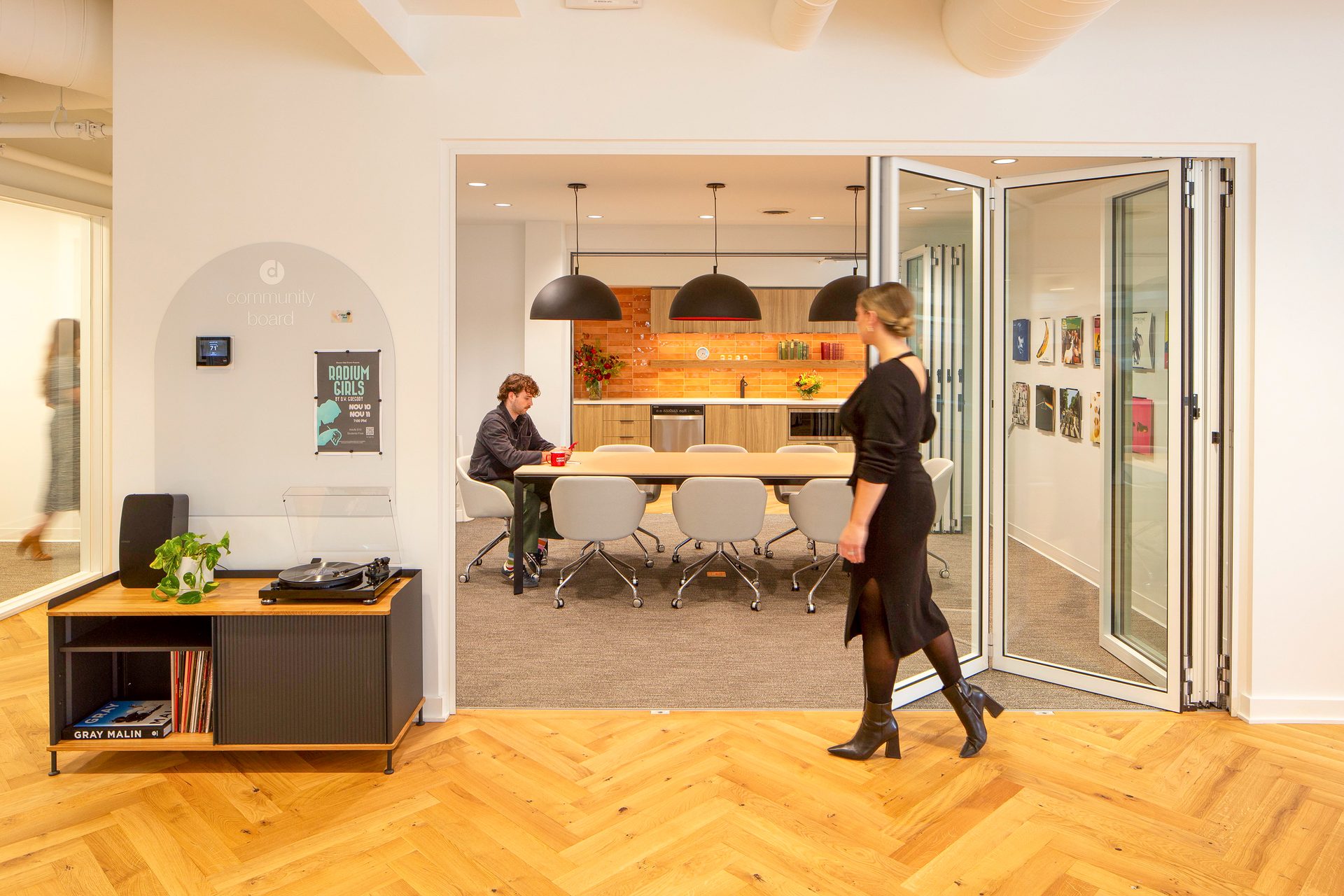
The office of an Omaha financial institution designed by Alley Poyner Macchietto Architecture, featuring a Generation 4 acoustical, folding glass wall system.
Reducing Risk and Insurance Costs
ICF buildings also lower builder’s risk insurance premiums from 35 percent by up to 60 percent compared to CMU or steel-frame structures. For a $10 million retail project, annual premiums could drop from $30,000 to $22,500. Once operational, property and liability insurance costs can decrease by 45 to 80 percent, further reducing total ownership costs. This reduction is due to ICF’s exceptional resistance to fire, storms and other disasters.
Resilience: Build for the Unexpected
Retail buildings must withstand severe weather, fire hazards, and noise pollution. ICF delivers unmatched resilience, ensuring safety and durability. ICF walls provide up to a 4-hour fire rating, outperforming CMU (2-3 hours) and steel structures (per code – 1 to 2 hours), which can fail at high temperatures. In high wind events, ICF buildings can endure speeds up to 250 mph, offering protection against EF-5 tornadoes and hurricanes. Traditional materials often fail at lower thresholds due to weaker connections and less integrated wall systems. And this does not consider the cost to reinforce and fortify these structures to resist wind shear or uplift.
ICF also reduces thermal bridging, preventing material degradation and minimizing the risk of intrusion by moisture, pests, and mold. These attributes ensure healthier indoor environments and lower maintenance costs. Unlike CMU, which can crack under extreme stress, or steel frames that are prone to thermal bridging, ICF offers dual layers of continuous insulation and a monolithic pour of reinforced concrete for greater durability, resulting in superior energy efficiency and long-term resilience.
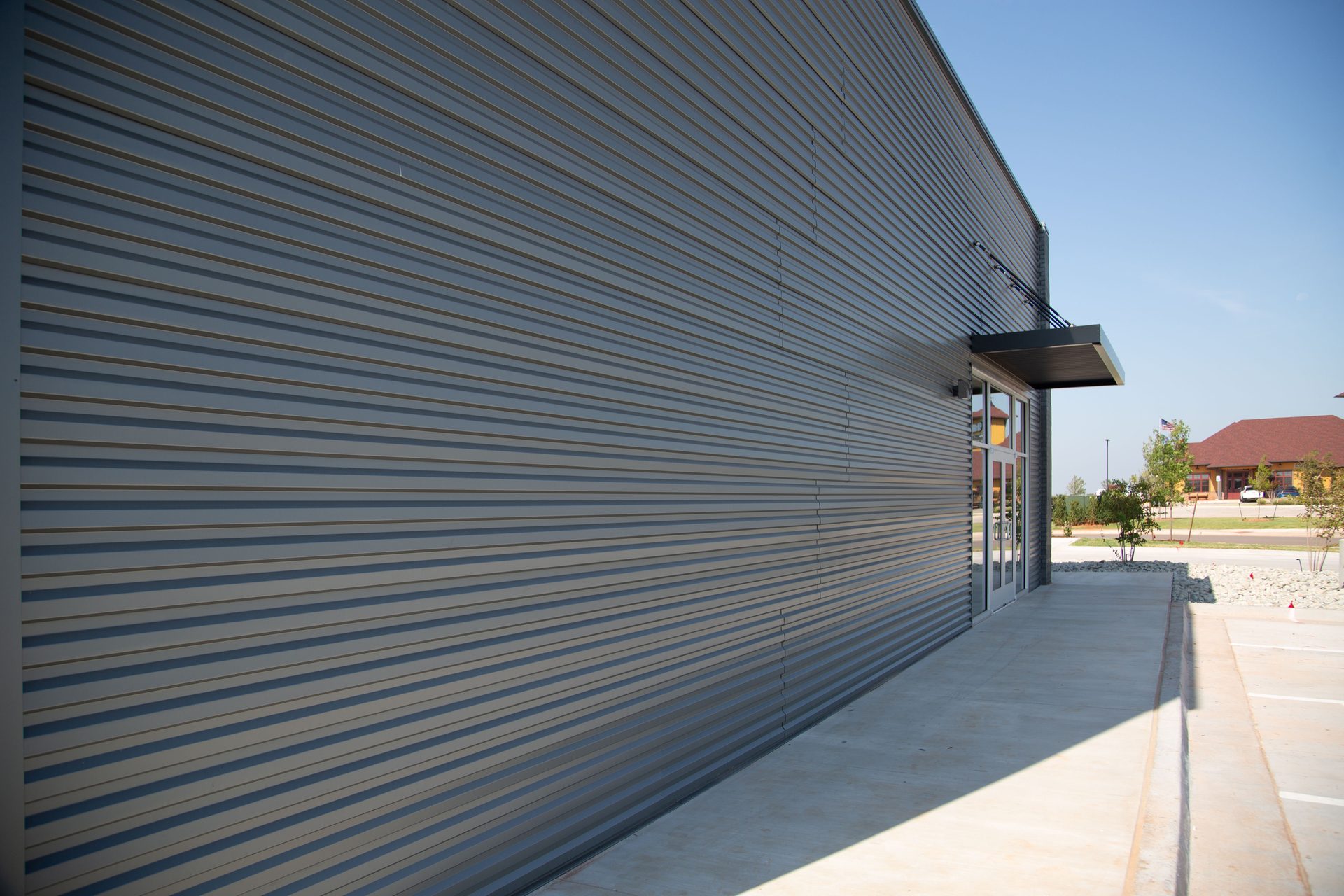
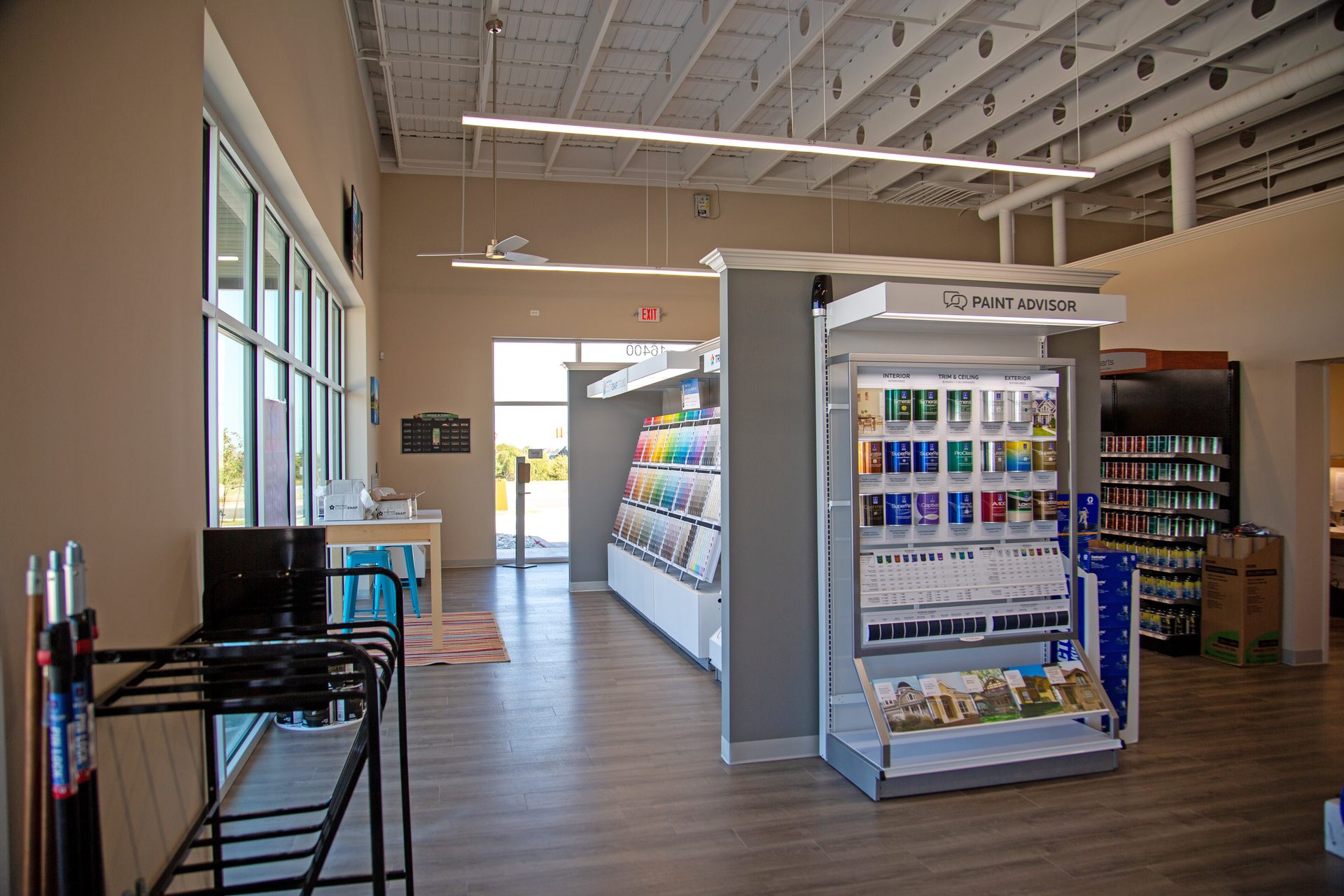
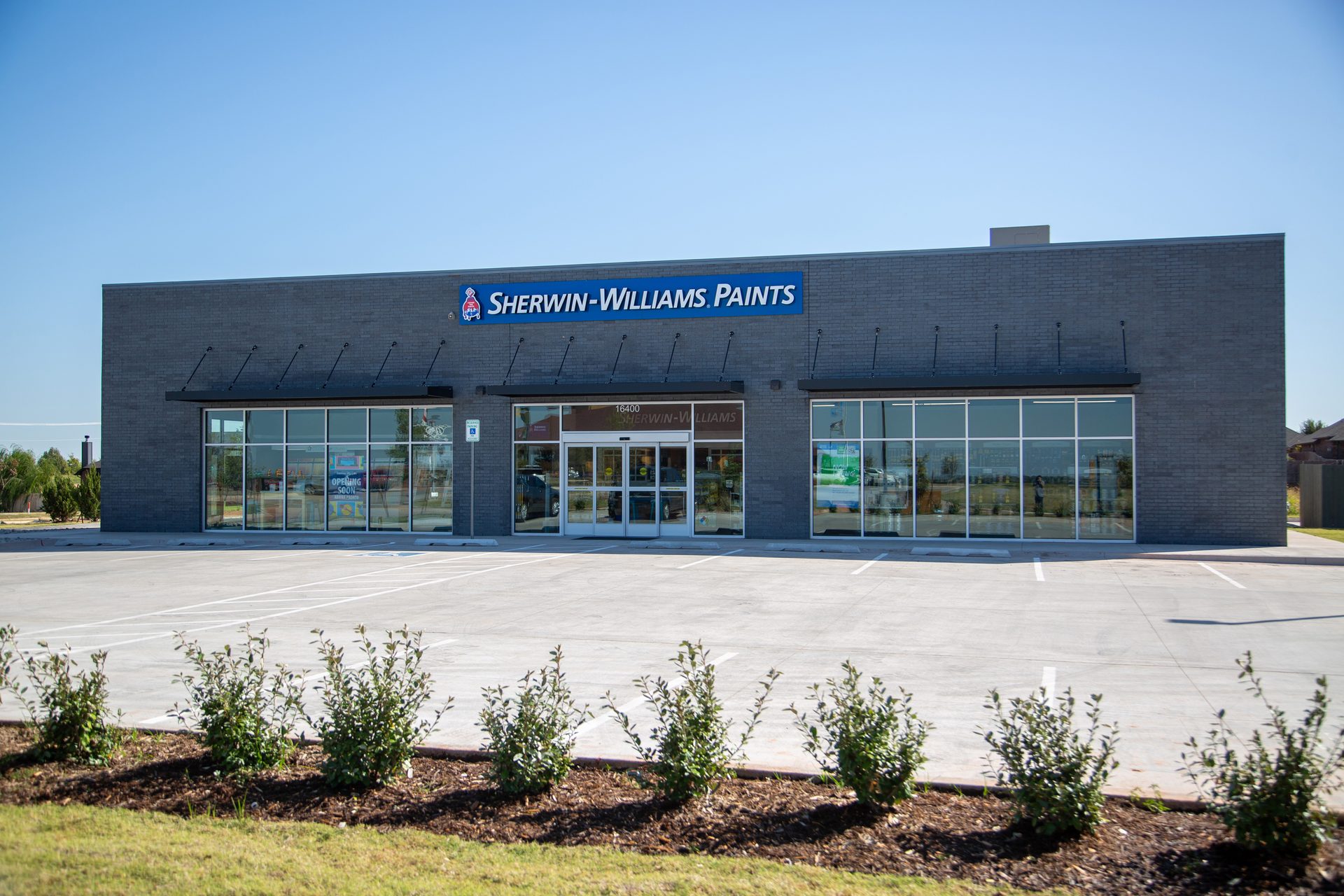
Sustainability: Grey is the New “Green”
ICF supports cradle-to-grave sustainability by reducing embodied carbon, minimizing construction waste, and enhancing building durability. This aligns with corporate ESG goals and certifications like LEED and EnergyStar. The durability of ICF also means fewer repairs over a building’s lifespan, reducing environmental impacts and supporting long-term sustainability objectives.
The concrete industry has made significant strides in lowering its carbon footprint. According to the Portland Cement Association and NRMCA, the industry reduced its environmental impact by 22 percent over the last decade. In 2023, the World Resource Institute reported that the ready-mix concrete industry has a lower global carbon footprint (8 percent of the world’s carbon emissions) when compared to the wood industry (10 percent) or steel industry (11 percent). Operationally, ICF-built retail spaces significantly reduce energy consumption through superior thermal performance, contributing to corporate sustainability commitments while exceeding minimum energy code requirements.
Additionally, ICF improves indoor air quality and occupant comfort, supporting ESG reporting and reducing lifecycle carbon footprints by up to 35 percent plus compared to traditional construction. And at the end of its life, ICF materials can all be recycled or reused, aligning with the principles of a circular economy and minimizing landfill waste. These sustainability benefits make ICF a forward-thinking choice for retail developers aiming to meet regulatory requirements and appeals to eco-conscious consumers.
Retail Case Study: Reduced Costs = Better Construction?
Sherwin-Williams Retail Store – Oklahoma City
A new Sherwin-Williams retail store in Oklahoma City utilized ICF for its 4,400-square-foot facility. The structure included storefront sections, showrooms, restrooms, a storage room, a shipping bay, and office space. The exterior combined brick, steel siding, and EIFS for finishes.
Choosing ICF reduced construction costs by over 10 percent compared to traditional CMU or steel systems. The exterior envelope was completed and dried-in in less than five weeks, significantly accelerating project timelines. Additionally, a Composite Concrete Flooring System roof deck was integrated to provide storm shelter capabilities, ensuring the building’s durability and safety. Here are some ways ICFs were able to reduce construction costs on this building:
- By using ICFs and concrete, the builders were able to increase the speed of construction by as much as 25 percent, helping reduce labor costs.
- Using ICFs for the exterior shell can save as much as 20 percent on the initial costs of the HVAC system equipment due to the reduction in heating and cooling loads, resulting in a return on investment that would reduce monthly utility costs by 40 percent or greater.
- ICFs can also reduce builder’s risk and owner liability insurance by as much as 80 percent by utilizing the storm and fire-resistant exterior building shell offered by ICFs.
- Using ICFs will allow construction to continue during cold weather conditions along with reducing the time needed to build the exterior building envelope.
So, if these savings (combined with disaster resilience and a reduced carbon footprint) can be achieved at scale for a 4,400-square-feet building (including the high-wind resistant composite concrete roof), then how much more could be saved on a big-box retail (100,000 square feet plus) or a large anchor development? The savings would be tremendous.
The Verdict: ICF is Ideal for Retail
Retail construction demands affordability, durability, and sustainability. ICF meets these needs through:
- Affordability: Lower labor costs, faster construction, and long-term energy savings.
- Resilience: Unmatched protection against storms, fire, and daily “wear and tear”.
- Sustainability: Reduced carbon footprint, unmatched energy efficiency, and support for green building certifications.
ICF offers a competitive alternative to CMU and steel frame systems, combining comparable (or reduced) initial costs with superior performance and sustainability. As the construction industry shifts toward energy-efficient and disaster-resilient practices, ICF is becoming a pivotal solution for retail developers. It not only addresses today’s challenges but also anticipates tomorrow’s needs.
For challenged retail developers seeking to maximize their ROI, enhance durability and longevity, and provide a lowered carbon footprint while meeting sustainability goals, ICFs are more than another option—they are the solution.
References
- National Ready Mixed Concrete Association (NRMCA): “Build With Strength”
- U.S. Department of Energy: “Insulation Materials”
- BNP Media/Architectural Record: “Making the Business Case for Building with Insulated Concrete Forms”
- Structure Magazine: “Insulating Concrete Forms for Commercial Construction”
- International Institute of Building Enclosure Consultants (IIBEC): “A Durable Option for Mid-Rise Construction”
- Architect Magazine: “The Benefits of Using ICF: One Architect’s Perspective”
Images courtesy of BuildBlock Building Systems.
Frank Gordon joined BuildBlock Building Systems LLC in early 2024 as vice president of Strategic Development, overseeing the Sales, Technical, and Marketing groups while promoting the use of ICF wall systems and Composite Concrete Flooring Systems. He is an active member of the design, construction, and facilities management industry for more than 36 years, serving five of those years as senior director, Building Innovations with NRMCA’s “Build With Strength” campaign in the Mid-Atlantic Region of the USA and as one of two co-directors for the Concrete Design Center, providing comparative analysis for concrete structural systems to the industry.
xxxxxxxx