xxxxxxx. By xxxxxx
xxxxx
xxxx
Giving the same look while helping the environment. By Mike Ireland
Portland Limestone Cement: The Foundation for Greener Building
xxxxxxxxxxxxxxx By xxxxxxxx
h2 - xxxx
h3 - xxxx
H1 headline
At the entrance of the river-walk in Tampa, Fla., luxury condominium The Heron at Water Street definitely has the “wow” effect. Striking, floor-to-ceiling windows, spacious balconies, roof gardens and other dramatic amenities render it architectural eye-candy. However, beyond the appreciation for the obvious visuals, it’s impressive to learn that this building was built with sustainability at its core. The high-rise is the first in a mixed-use development that promotes itself as walkable, connected and sustainable.
Developed by the owner of the Tampa Bay Lightning and an investment group led by Bill Gates, the project team’s commitment to cutting emissions began with the choice to use Portland-limestone cement concrete as a key structural material. Using PLC (Type IL cement) is one way that concrete producers and contractors can achieve a lower carbon footprint. In the coming years, more and more projects will benefit from similar materials. At the forefront of innovation and efficiency, concrete produced with the right cementitious materials lays the groundwork for a sustainable structure.
Most of the 49,410 cubic yards of concrete used to construct The Heron were made from mixes using PLC and supplemental cementitious materials. Cement-only mixes included the precast members and most decks, which were post-tensioned.
Exposed architectural concrete finishes for some of the structural members feature PLC and add to the building’s dramatic appearance. Because PLCs can have a slightly lighter color than ordinary Portland cement, it imbued the concrete with a slightly lighter color, another striking feature for architects to consider. The Heron is a show-stopping example of projects responding to the increasing requests for lower-carbon cement and concrete we so often get from modern designers, owners and consumers with net-zero goals.
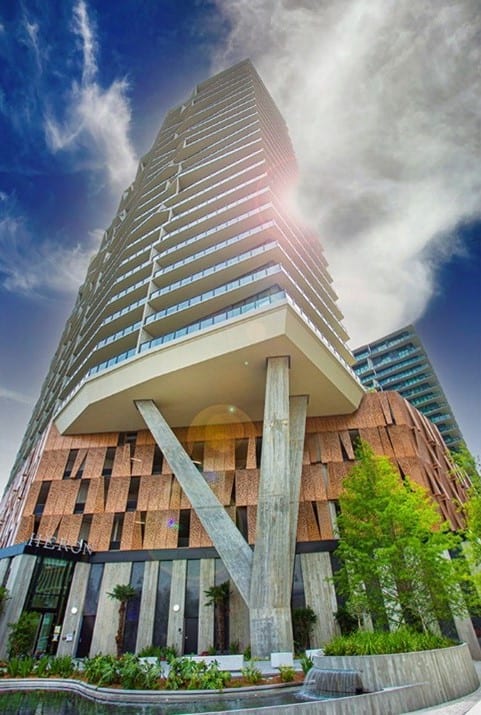
A New Jersey office designed by Gensler, featuring a NanaWall HSW60 single-track system | Photography by Garrett Rowland Photography
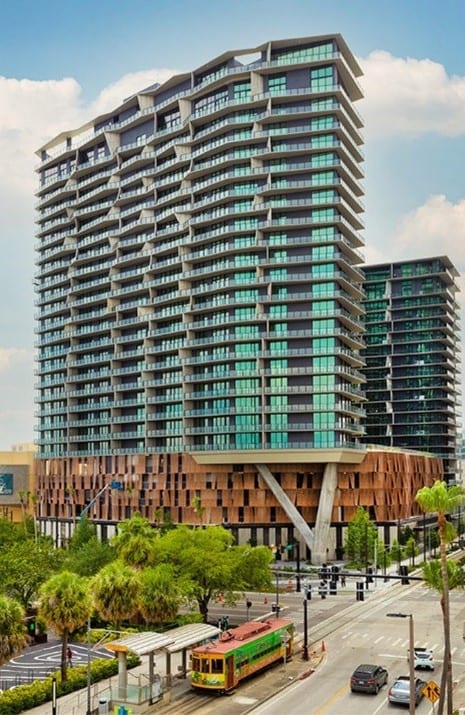
The office of an Omaha financial institution designed by Alley Poyner Macchietto Architecture, featuring a Generation 4 acoustical, folding glass wall system.
What is PLC?
So, what exactly are PLCs? Portland cement specifications limit the amount of limestone that can be utilized in cement to just 5 percent. That’s why Portland-limestone cements were developed, allowing for the use of up to 15 percent limestone and decreasing the amount of clinker. Much like fly ash, other pozzolans and slag cement have done for decades, the use of limestone as a cement ingredient reduces the overall carbon footprint while providing the same strength, durability and resilience as mixtures with traditional Portland cement.
Both the availability and acceptance of PLCs have increased over the past decade in the United States. ACI 318, Building Code Requirements for Concrete Construction includes PLCs and other blended cements. Along with code recognition, PLCs are similarly included in ACI 301, Specification for Structural Concrete and ASTM C94, Specification for Ready-Mixed Concrete. In addition, the International Code Council, all 50 state DOTs, the Federal Aviation Administration and the American Institute of Architects Master Specification recognize PLCs. Nevertheless, PLC has been a staple in European construction for decades. Germany started using it in the 1960s. It became commonplace in France in the 1970s. In addition, PLC has been widely used in the U.K. since the 1990s.
A switch to PLC is handled the same way as a switch to any other new material—with an investigation of the fresh concrete mixture’s behavior and hardened properties. Trial batches, mockups and specialty performance testing can all be completed to ensure a reliable final product. PLC can be sourced from many locations across the country, and it makes up about half of the cement used for general construction in the U.S.
Researching PLC
Overall, PLC is well understood because it has been the subject of extensive research and testing by the industry, both in the U.S. and abroad. Researchers have studied fresh properties related to placing and finishing, as well as hardened properties that relate to durability. Durability is usually first demonstrated by accelerated laboratory testing and backed up by observation of field performance over time. Areas studied include resistance to scaling and freeze-thaw, chlorides, sulfates and alkali-silica reaction. Each type of exposure has been thoroughly investigated to confirm that PLC produces strong, resilient concrete.
Caltrans, the agency that oversees more than 50,000 miles of highways and freeways in California, commissioned Oregon State University to conduct a study on PLC’s efficacy compared to traditional cement. The independent study, conducted by OSU’s College of Engineering, concluded that PLC would work just as well as traditional cement while also reducing carbon emissions.
Reducing Carbon Emissions
PLCs are enabling the reduction of our carbon footprint in many different projects, including diverse applications, from storage structures to bridges. Notably, PLC was used in the Seattle Storm’s new $64 million training facility. The Seattle Storm Center for Basketball Performance was recently named a 2024 Concrete Innovation Award winner by the National Ready-Mixed Concrete Association.
The 50,000-square-foot project achieved a significant reduction in greenhouse gas emissions from the concrete. Overall, the project exceeded a 50 percent reduction compared to typical mixes in the region and achieved 80 percent of the 2030 targeted reductions by the World Economic Forum’s First Movers Coalition for near-zero carbon concrete.
The cement industry cares deeply about the success of PLC and those who are using it. The Portland Cement Association is working closely with the National Ready-Mixed Concrete Association and the American Society of Concrete Contractors to ensure the industry is prepared to deliver PLC and answer technical questions.
With more than 3.9 million metric tons of carbon avoided in 2023 using PLC, America’s cement industry is already cutting emissions. Contractors, architects, manufacturers, suppliers and distributors are learning about the benefits of PLC and integrating it into their practices. The collaborative efforts are making the cement industry’s mission to reach carbon neutrality seem less like a distant possibility and more like an achievable reality.
References
- xxxxxxxxxxx
- xxxxxxxxxxx
Images courtesy of Portland Cement Association.
Mike Ireland is currently in his seventh year as Portland Cement Association president and CEO. The association launched its Roadmap to Carbon Neutrality under his leadership in October 2021. Previously, Ireland was associate executive director of the American Society of Mechanical Engineers, as well as CEO of the Association for Facility Engineers and the National Environmental Balancing Bureau.
xxxxxxxx