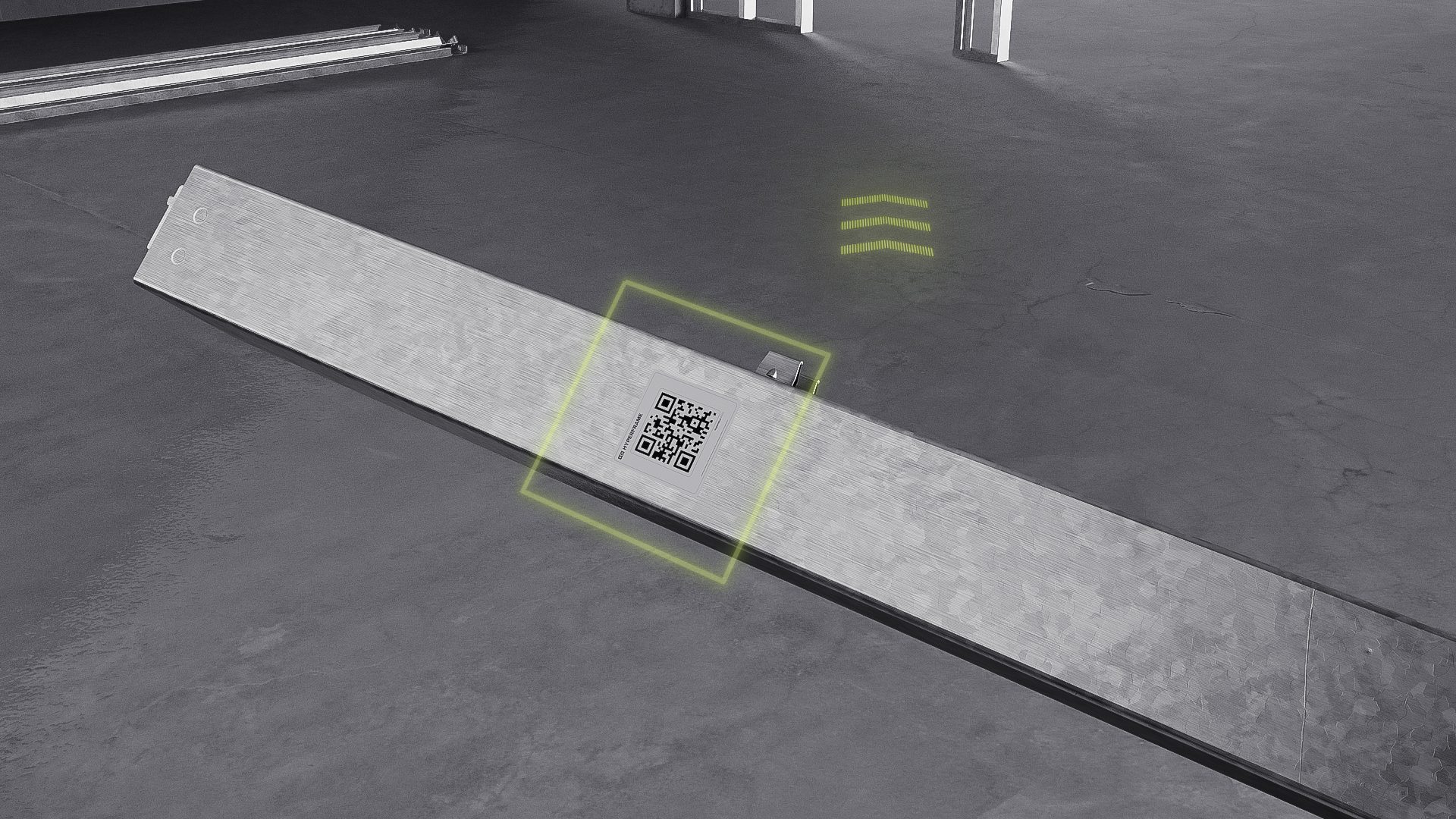
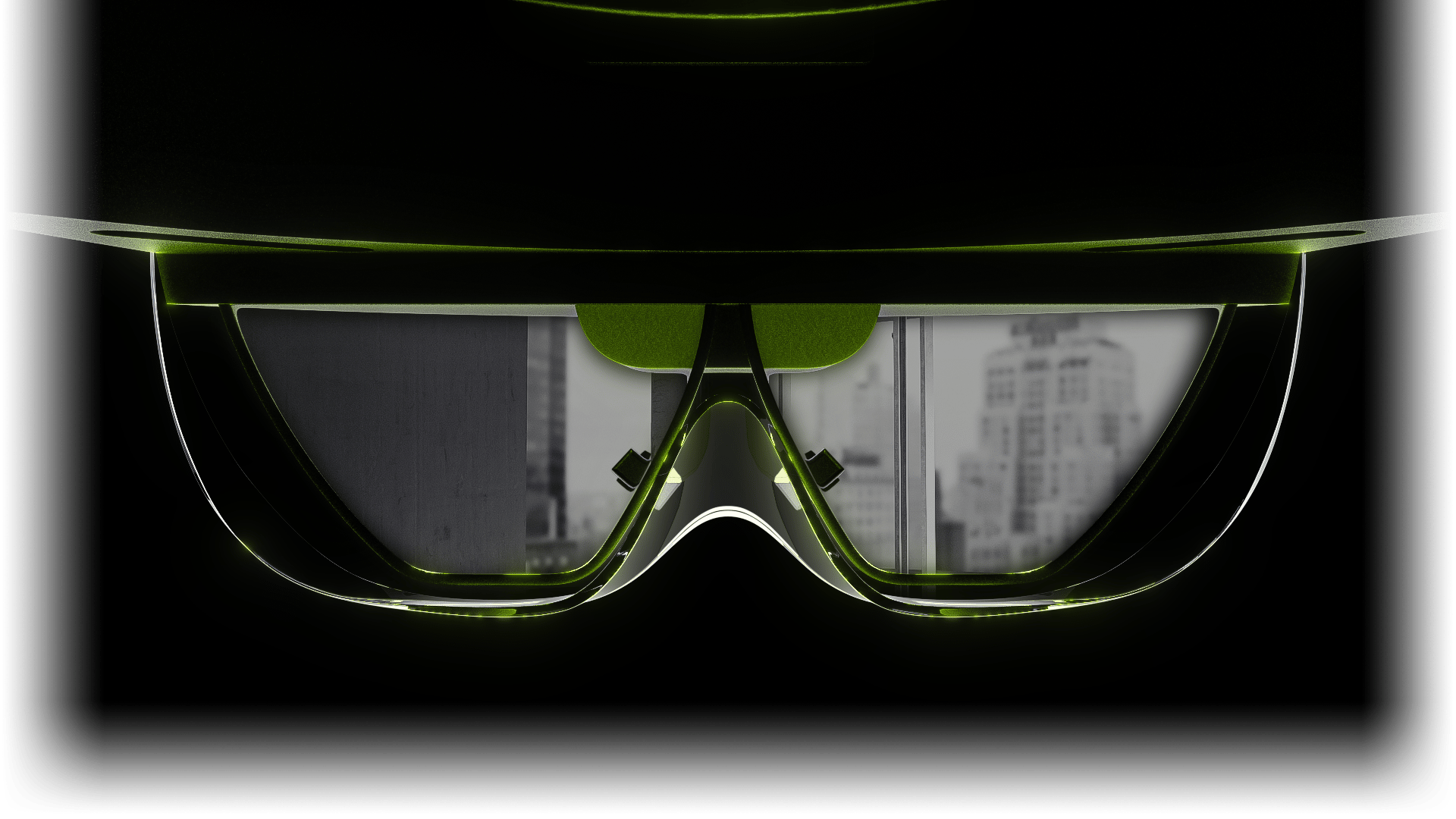
A discussion about the roles of people and robots in the future of construction. By Ken Sobel
Robots in Steel Framing
The advent of construction robotics leads to many questions for today’s contractors. How will construction technology evolve over the next 10 years? Will robots replace tasks that human crews perform today? How might contractors choose when to use a robot and when to use human labor?
Construction technology startups are already confronting these questions from a product development perspective. How should they design their products to be used? How do they intend for people and machines to interact? Their decisions will have a significant impact on how contractors run their businesses in the future.
At the outfit I’m a part of—a metal framing technology company I co-founded in 2018—our product development process often starts with two simple questions: what types of tasks are people best at, and what types of tasks are machines best at? The answers inform how future construction products should blend people and technology.
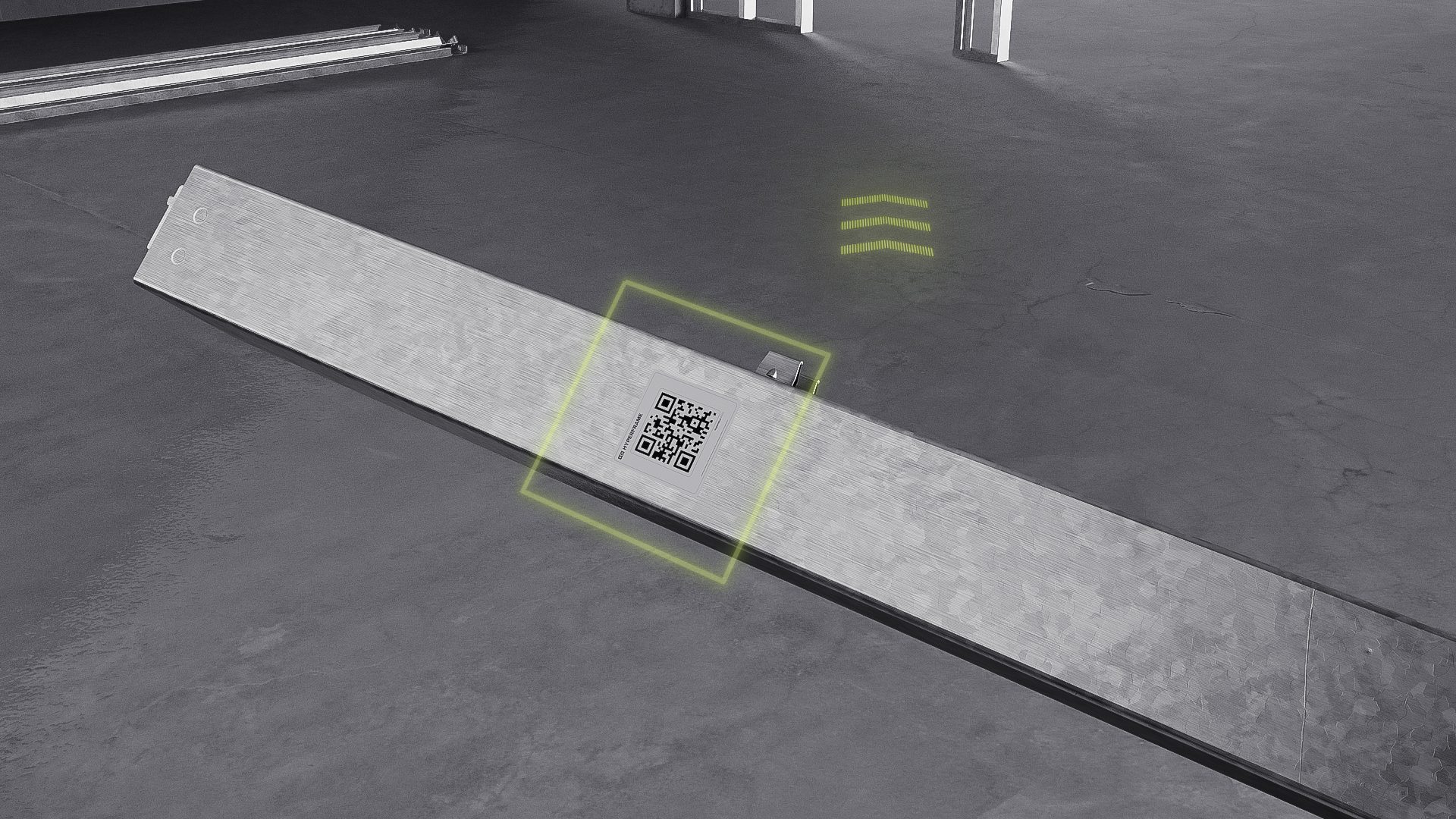
People: Dexterous and Adaptable but Prone to Error
Human physiology gives us an extreme amount of dexterity. This comes from the number of joints in our bodies and the number of ways in which we can move them. Each direction in which a joint can move is called a degree of freedom. The human body has over two hundred degrees of freedom, whereas the typical robotic arm has only six. With such a vast range of motion, we have the ability to easily grasp items and move them into a variety of positions—extremely useful skills on the job site. No commercially available robot comes close to our level of dexterity.
Then we have human intelligence, which enables us to think critically and negotiate complex environments. For example, consider the sophisticated reasoning needed for a task as simple as standing a stud. The framer needs to identify the position of a drywall cart, separate a stud from its bundle, flip it vertically, navigate through construction debris, avoid collisions with other people, and twist the stud into place. While framing crews perform this task with ease everyday, today’s robots would struggle to maneuver long, unwieldy studs through an unpredictable job site environment. More sophisticated problem-solving skills—such as resolving unexpected field conditions—are even further out of reach for machines.
Despite our superior dexterity and adaptability, people act imperfectly. We forget things. We make mistakes. We get tired. We get hurt. These are areas of opportunity for technology innovators.
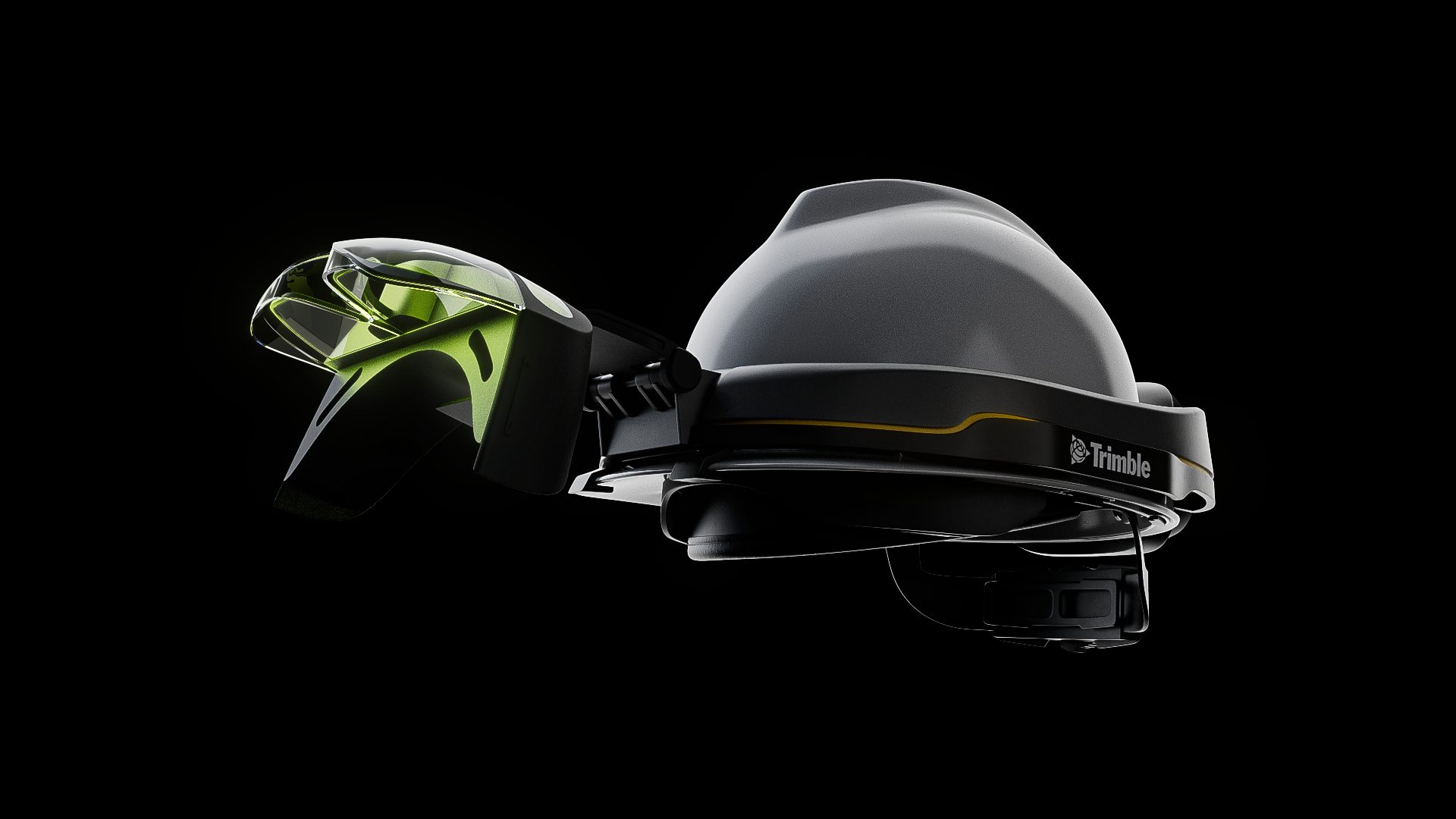
Machines: Consistent Performers in Controlled Environments
Machines are absurdly good at math. Today’s smartphones run trillions of operations per second. The human brain can run, at best, 1,000 operations per second—making computers several billion times faster than people at basic arithmetic. Not only are computers quick, but they deliver the same answer every time. They don’t make mistakes. They don’t get tired.
As a result, machines excel at tasks that are driven by math. We see this in total station technology, which uses trigonometry to report the position of a prism pole on the job site. Precise 3-D measurements are calculated in an instant. One might debate the time lost during total station setup, but once properly configured, a total station beats the speed and accuracy of a tape measure every time.
Despite their excellence in performing mathematical tasks, machines are limited by the way they were designed. They tend to malfunction when they encounter conditions their creators did not anticipate.
The result is that machines are good at performing precise, repeated operations in tested and controlled environments. For technology to succeed in construction, it must be designed to deliver value under these limitations. In cases where the environment can’t be controlled, a human operator is required to guide the machine through unexpected circumstances. It is critical for the value delivered by the machine to outweigh the cost of operator supervision.
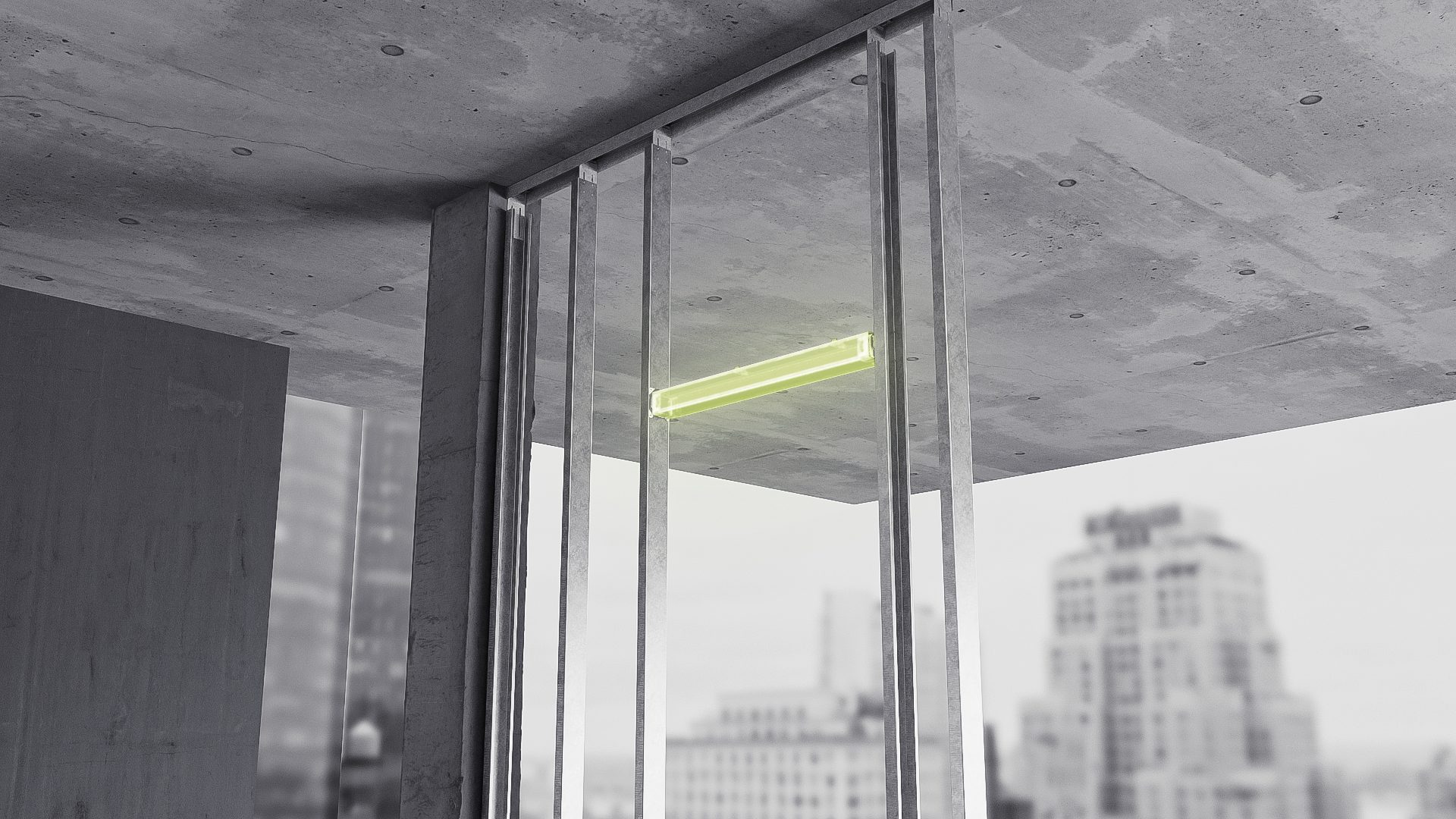
What it Means for Construction
Stepping back, you’ll notice that people and machines have complementary strengths. Where one is strong, the other is weak – and vice versa. The most valuable construction products of the future will combine the best of human and computer capability. Here are some areas where that can happen:
- BIM: Today’s BIM software relies heavily upon human modelers to configure the proper details throughout the plan. This has made BIM time-consuming, expensive, and prone to error. In the future, we will see advanced BIM applications that mathematically coordinate between the trades and determine the optimal detail for every condition. The software will solve 99 percent of the model, allowing human modelers to focus on the 1 percent—the strange conditions that the software wasn’t programmed to expect. These improvements will make BIM faster, more accurate, and more useful to the overall construction process.
- Manufacturing: Robots thrive in the manufacturing world because the environment is highly controlled. Robotic manufacturing processes can be insanely accurate (repeatable to within thousandths of an inch) and insanely quick (measured in milliseconds, not minutes). This technology will lead to the manufacture of more precise, customized, and multifunctional building products that are easier to install in the field.
- Installation: Buildings consist of a vast variety of construction components – consisting of many different shapes and sizes and installed in many different ways. The construction sites that receive them are chaotic. They contain hundreds of construction workers who perform hundreds of simultaneous operations. This injects immense unpredictability into the site.
You might have already sensed it—installing products in these conditions is extremely challenging for robots but very well suited to human dexterity and adaptability. Bearing this in mind, installation is likely to remain a human-centered activity for the foreseeable future. The role of technology on the job site will be to amplify human strengths and minimize human weaknesses, granting construction workers superhuman abilities. Expect innovations like augmented reality software that show where components fit into the building, or robotic layout tools that define the floor plan layout prior to framing.
Software and robotics are poised to become a critical part of our industry. But they’re not coming to take over. They’re coming to help with tasks that people don’t naturally excel at. The transition towards these tools may feel bumpy at times, especially as digital innovators learn to work with their customers.
Though some technologies may stumble, many will thrive. As this experimentation evolves over the next 10 years, we will achieve the highest levels of productivity, quality, and safety our industry has ever seen.
Images courtesy of Hyperframe.
Ken Sobel is co-founder and CEO of Hyperframe, a Berkeley-based startup that develops ultra-labor-efficient metal wall framing. With a background in mechanical engineering and software development, Sobel leads a team of eleven employees. The company has raised over $11 million in venture funding from notable investors including Saint-Gobain, Blackhorn Ventures, and Hometeam Ventures.