Building excellence with EIF systems: the journey of Elite Wall Systems. By John Wyatt
Elite Status
xxxxx. xxx
xxxxx
xxxxxxxxx
EIMA Excellence Awards
- 2019 Hero Award - Buena Vista Apartments
- 2020 Award of Merit - Imperial Facade
- 2021 Award of Merit - Louis M Klein Middle School
- 2022 Award of Merit - LI Vets
For more than 25 years, Richard Sangiorgi has led Elite Wall Systems Inc. with passion, expertise and an unwavering commitment to quality. With nearly four decades of experience in the construction industry, Sangiorgi has built a company that specializes in an array of services, including EIFS, cement stucco, cultured stone, plastering, ornamental moldings and more. Based in Deer Park, N.Y., the company has made a name for itself as a leader in interior and exterior restoration, and throughout the Northeast/Tri-State area.
xxxxxxxxxxxxxxx By xxxxxxxx
h2 - xxxx
h3 - xxxx
H1 headline
Sangiorgi’s journey in the trades began early. As a creative child, he was naturally drawn to hands-on work. By the age of 19, he had already acquired experience in multiple trades, including carpentry, electrical, plumbing, roofing, painting, and tiling. His passion for construction led him to pursue a degree in architecture at SUNY Farmingdale, where he honed his design and structural knowledge.
His first professional role was as an assistant project manager for a large union subcontractor specializing in commercial drywall, acoustical ceilings, flooring, and plaster. Demonstrating exceptional leadership and business acumen, Sangiorgi quickly rose through the ranks, eventually overseeing hundreds of employees as an operations manager. At 32, he took the leap to establish his own business—Elite Wall Systems —which has since seen consistent growth and success.
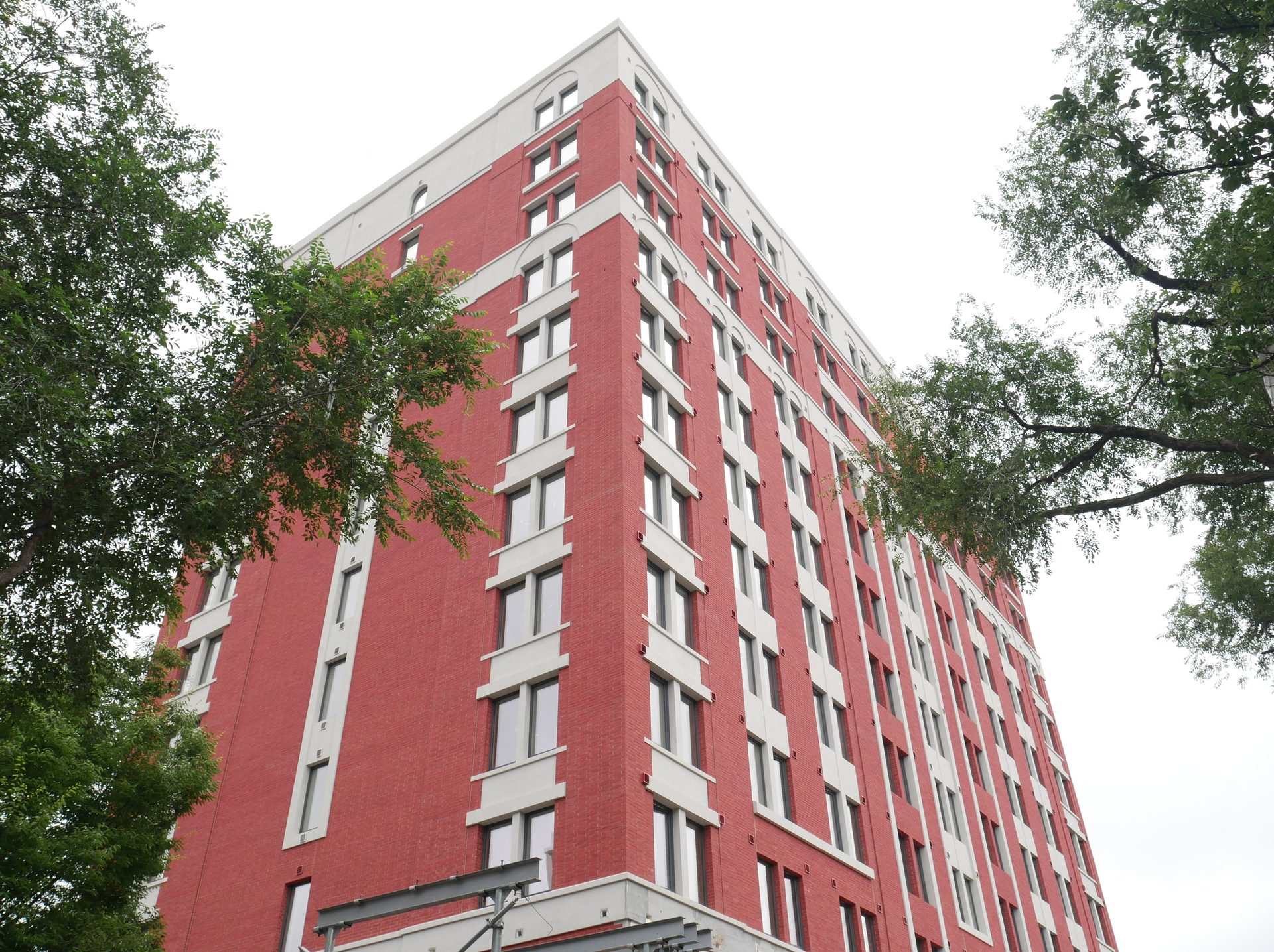
A New Jersey office designed by Gensler, featuring a NanaWall HSW60 single-track system | Photography by Garrett Rowland Photography
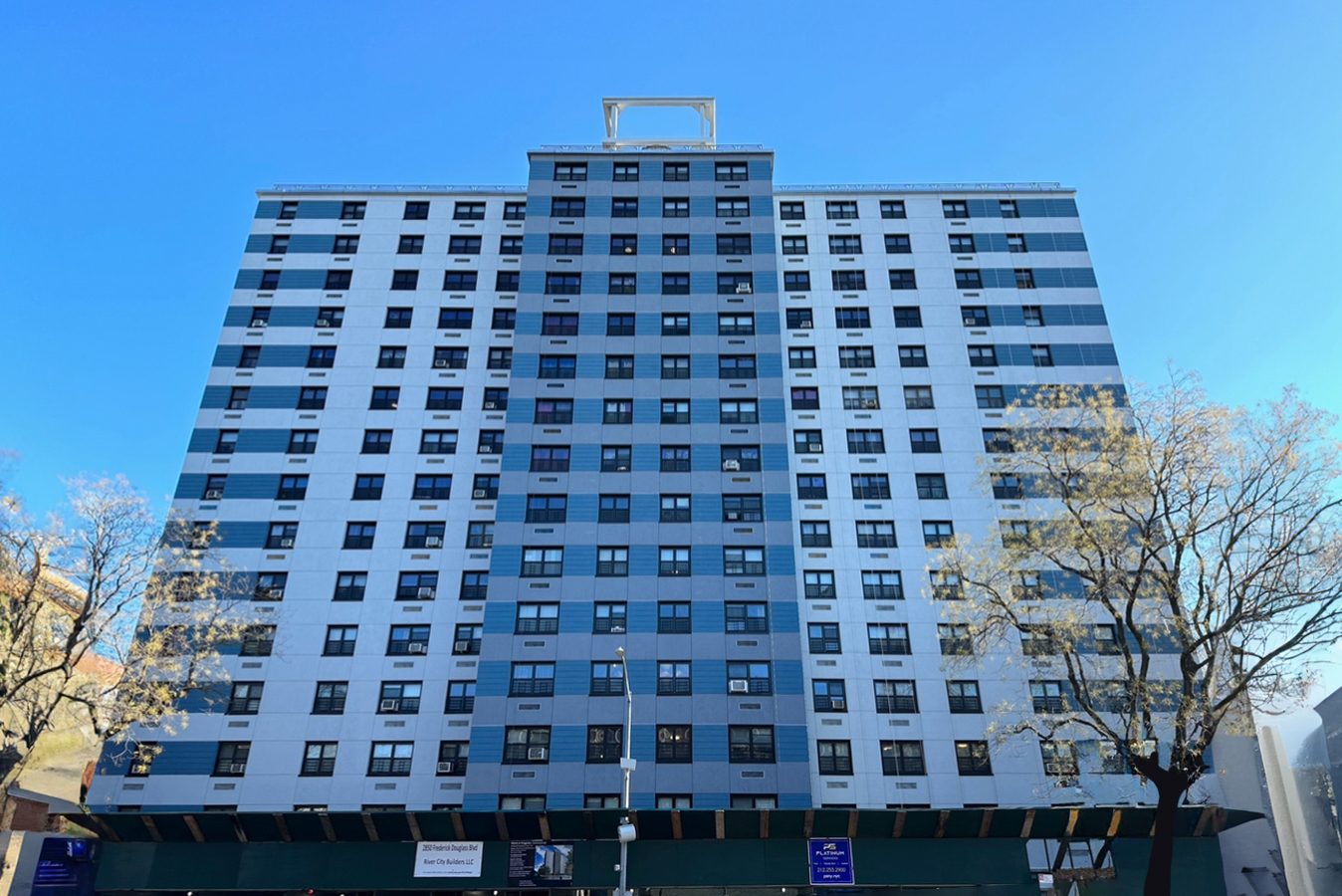
The office of an Omaha financial institution designed by Alley Poyner Macchietto Architecture, featuring a Generation 4 acoustical, folding glass wall system.
A Business Built on Expertise and Excellence
The company operates with a team ranging from eight to 10 office employees and between 40 to 60 field workers, depending on the project workload. The company’s expertise lies in EIFS, conventional plaster, acoustical plaster, and both interior and exterior restoration. Sangiorgi ensures his workforce is highly trained, with all field mechanics and operations team members being EIFS Smart Certified and current in OSHA training and certified in acoustical plaster applications.
With affiliations including AWCI, EIMA, WC&C New York, BAC Plasterers and LIBI, Sangiorgi is deeply embedded in the industry’s best practices and standards. His company works with top manufacturers such as Sto Corp, USG Plaster, StarSilent Acoustical Plaster/Pyrok and more, ensuring that only high-quality materials are used in their projects.
Navigating Industry Challenges and Growth
The past 25 years have not been without challenges. The rising costs of fuel, materials, taxes, insurance and over-regulations have presented difficulties for many contractors in New York. Sangiorgi highlights a particularly burdensome issue—the state’s outdated labor laws (200, 240 and 241 aka “Scaffolding Law”) enacted in 1885, for which many states followed suit (Acts 200, 240, and 241)—which have driven insurance premiums up drastically. While other states have moved on from these century-old regulations many years ago, New York’s strict liability laws make it significantly more expensive for contractors to operate. Today, New York state is the only one not to repeal this outdated law.
Despite these challenges, Elite Wall Systems has continued to grow. Two years ago was its highest-grossing year, and while the latter half of 2024 has been slower, Sangiorgi remains optimistic, as the company’s backlog for 2025 is on track to exceed all previous sales records.
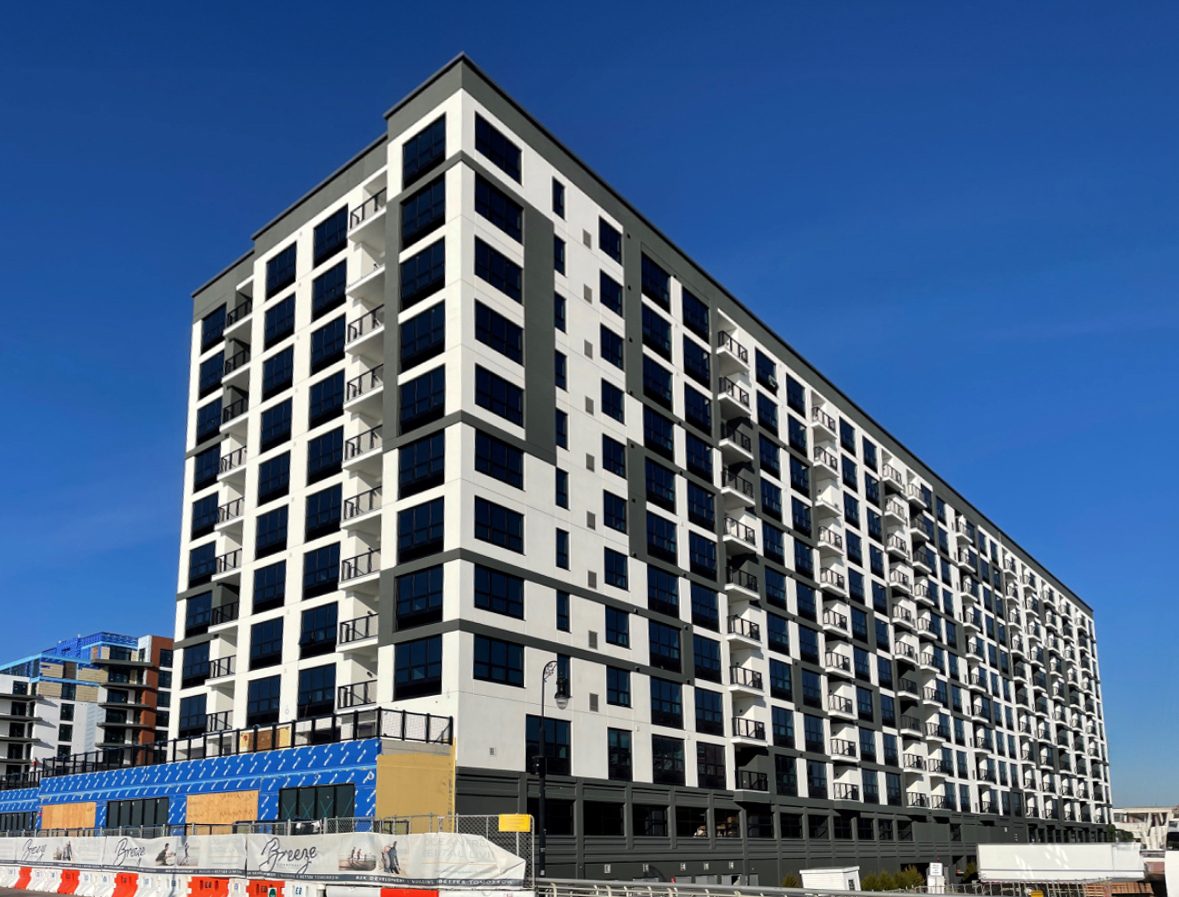
A New Jersey office designed by Gensler, featuring a NanaWall HSW60 single-track system | Photography by Garrett Rowland Photography
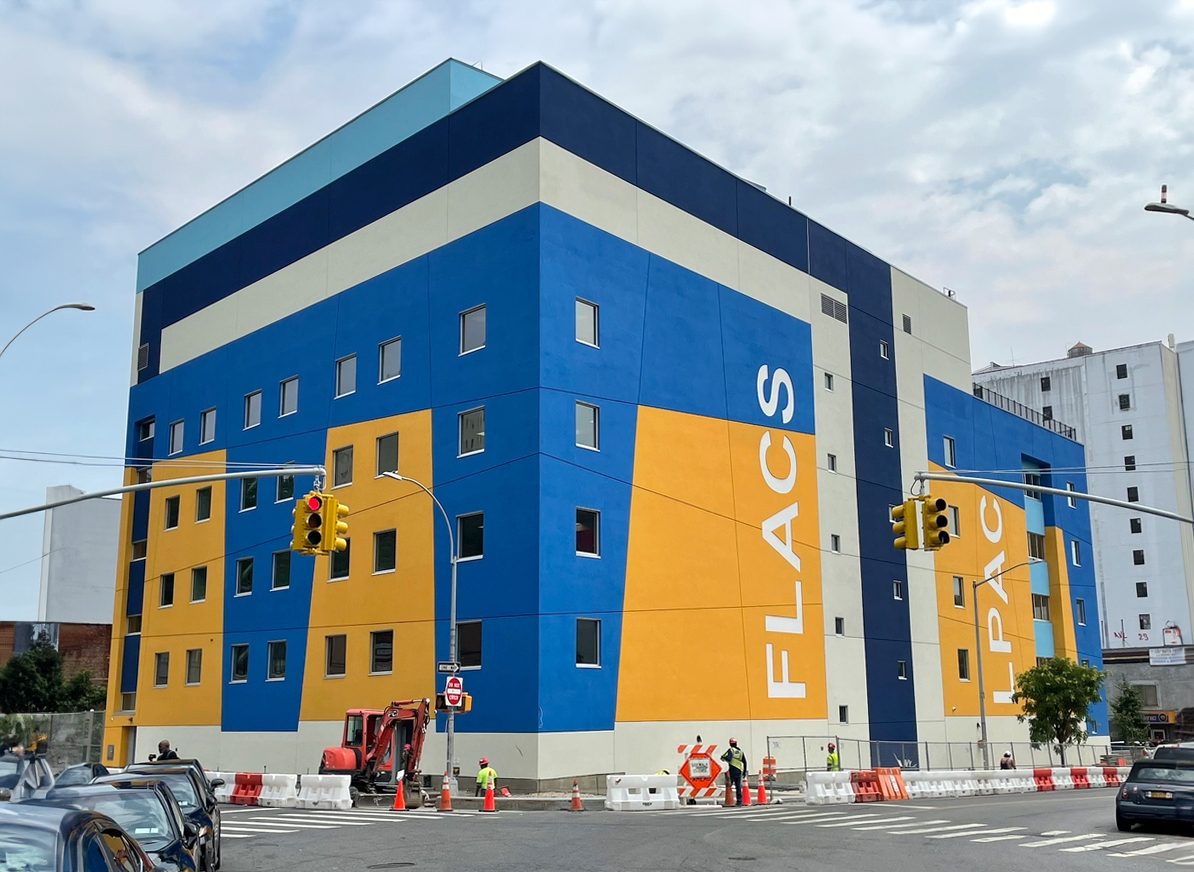
The office of an Omaha financial institution designed by Alley Poyner Macchietto Architecture, featuring a Generation 4 acoustical, folding glass wall system.
Working on Innovative Projects
One of Elite Wall Systems’ most exciting projects in recent years has been the Linden Grove Project, a 13-story modular structure designed for affordable senior housing under New York City Housing Authority. This project, built to meet U.S. Green Building and LEED standards, presented a unique opportunity for innovation. Elite Wall Systems developed a hybrid EIFS panel system, enabling them to work offsite during the winter months—typically a slow period for their trade. This project was also among the first in the United States to incorporate the new StoCast Brick product, demonstrating the company’s willingness to embrace cutting-edge building technologies. But the StoCast Brick system has been proven performance for 20 years of project use in Europe before starting up manufacturing in the United States.
When asked what sets Elite Wall Systems apart from the competition, Sangiorgi points to 38 years experience in drywall and plastering, highly skilled union labor, and a commitment to safety. His leadership philosophy is simple yet effective: build a team that is well-rounded in multiple trades, instill discipline and safety-first attitudes, and maintain an accident-free work zone.
The company is also financially prudent. Sangiorgi has weathered three major recessions in his career and learned the importance of saving for downturns and making wise investments, including real estate. His cost-conscious mindset has enabled Elite Wall Systems to remain stable even in uncertain economic times.
Beyond Business
Beyond his professional achievements, Sangiorgi cherishes time with his family. A proud father of three, he looks forward to watching his children carve their own paths. When not working, he enjoys boating and fishing—his two biggest passions outside of business.
His love for architecture extends beyond construction; if given the opportunity, he’d love to tour Shanghai, China, or Dubai to admire its modern high-rise marvels. He also likes to visit Europe to see the ancient architecture of the Old World, which draws him back to his interest in ornamental plaster.
Asked about a dream dinner guest, Sangiorgi’s answer was heartfelt—his parents. His values, both in business and in life, reflect a deep respect for family, integrity, and perseverance.
What the Future Holds
Sangiorgi’s long-term goal is to continue growing Elite Wall Systems at a sustainable pace while maintaining the balance between work and family life, which he also instills in all his employees. His focus remains on building a company culture where employees are empowered to lead and take pride in their work. By upholding strong ethical and professional standards, he has created a company that is not just surviving—but thriving.
Through decades of hard work, innovation, and a steadfast dedication to quality, Sangiorgi has solidified his place as one of the most respected contractors in Northeast region/Tri-State area. As the industry continues to evolve, one thing remains certain: Elite Wall Systems will continue to set the benchmark for excellence in the years to come.
Project Profile:
Project Name: 223 Linden Grove, Brooklyn
General Contractor: Promethean Builders
Developer: Blue Sea and Gilbane
Architect: Chris Benedict Architect R.A.
EIFS Installer: Elite Wall Systems
EIFS Manufacturer: Sto Corp.
Product: StoCast Brick
Gilbane Development Co., in a joint venture partnership with Blue Sea Development Co., developed Linden Grove, an affordable senior housing apartment building in the Bushwick neighborhood of Brooklyn, N.Y. The highly efficient and sustainable, 13-story, 153-unit community combines the latest in technology, programming and amenities within a traditional building exterior that pays homage to Bushwick’s long and notable architectural heritage. Some highlights and overviews of the project include:
- More than 150 senior affordable rental apartments were erected in a 13-story building located in the Bushwick neighborhood of Brooklyn;
- Part of New York City Housing Preservation & Development’s Seniors First, a three-pronged strategy including Aging in Place, an initiative to make more homes accessible to seniors and people with disabilities; developing new senior housing on NYCHA and other land; and preserving more of the senior housing originally developed through federal housing plans;
- Mix of studios and one-bedroom apartments for rent to the formerly homeless and individuals with incomes at 30 to 40 percent of the area median income;
- Gilbane Development Company’s first use of a modular solution, offering fast delivery of 206 modules manufactured in a controlled environment;
- JASA, one of New York’s largest and most trusted agencies serving older adults, will provide property management and supportive services;
- Building features and amenities will include a rooftop indoor fitness center, an outdoor fitness area, laundry room, private outdoor recreation area, video intercom, Smart Wi-Fi thermostats, solar panels, rooftop community gardens, rooftop sitting area, and artist-design fences;
- Designed to meet Passive House (PHIUS), USGBC (LEED Platinum), the National Association of Home Builders’ National Green Building Standard (Gold), the U.S. Department of Energy (Zero Energy Ready Home), the US Environmental Protection Agency (EnergyStar), the Center for Active Design (Active Design Verified), and Fitwel;
- Enhanced building performance will be achieved by employing several energy efficient elements such as a high-efficiency 90 to 98 percent VRF heating and cooling system, airtight drywall approach construction methodology, and Passive House certified windows;
- Winner in New York State’s inaugural Buildings of Excellence Competition for the early design phase of a low-carbon emitting multifamily building;
- A hybrid EIF system utilizing Sto systems.
Elite Wall Systems was contracted by Promethean Builders, a well-respected general contractor based in New York. Promethean Builders is a full-service general contractor and construction manager that specializes in many different areas, such as commercial, residential, sports and entertainment, performing arts, education, healthcare and modular.
Elite Wall Systems was hired to clad the exterior envelope of a 13-story low-income senior housing development project with EIFS.
The building was designed by Chris Benedict Architects R.A., in collaboration with the owners and partners Gilbane Development and Blue Sea Development.
Chris Benedict is an early pioneer in energy efficiency in apartment buildings and one of the first to adopt passive house protocols in the U.S.
Blue Sea Development specializes in creating affordable housing, with a focus on sustainability and community health. Its projects often incorporate green building practices and aim to enhance residents’ well-being.
Gilbane Development is a real estate development, investment and property management division of Gilbane Inc., a global player in construction and real estate development with 150 years of experience. It operates throughout North America and internationally, with more than 45 offices worldwide with its headquarters still in Providence, R.I., where its founder William H. Gilbane founded the company in 1870.
The owners and architects decided to design the exterior envelope using a StoTherm ci EIF system with continuous drainage and insulation. It is a high-performance, energy-efficient wall cladding that integrates StoGuard air and water-resistive barrier, EPS insulation, and drainage. The EIFS wall finishes were designed with Sto Cast Brick and ornamental EIFS limestone features such as crown moldings, sills and arches, giving it a Renaissance-revival style of architecture, which was popular in New York City during the late 19th century.
The Linden Grove project presented several unique challenges, as it was a first-of-its-kind modular ground-up building. It was the tallest affordable/low-income senior housing project ever built modular in New York. It is made up of 210 individual modules, 13 stories high, creating 153 senior apartments in the Bushwick area of Brooklyn.
In late 2022, the project team awarded the EIFS installation to Elite Wall Systems; simultaneously, Sto Corp, in its Atlanta plant, was still setting up its tooling and machinery to manufacture the StoCast Brick product for the first time in the United States.
Prior to that, the product was mostly popular in Europe for 20 years with some smaller projects in the U.S. This was a disadvantage for Elite Wall Systems and local EIFS installers in New York bidding the project, since the subcontractor never had installed the product and therefore we had no prior labor productions to utilize during the bidding process. The Sto Cast Brick Product has a beautiful natural brick appearance and has proven performance with more than 20 years of project use with specific colors, patterns and textures.
The EIFS portion of the project was originally scheduled to begin July 2023 and finish in late 2023. Due the nature of this project that was a prototype, 13-story modular build located in the extremely narrow streets of Brooklyn, there were many unforeseen conditions.
This created delays pushing the EIFS installation start date to late October, using up most of the four- to five-month EIFS schedule. By the time the building was watertight and ready for EIFS installation, it was already the beginning of November. With unusually cold weather patterns already developing in mid-November 2023, the company was experiencing below-freezing temperatures. (EIFS installations in the northeast region of the country usually come to a halt around December and resume again in April.)
These delays could cost the owners, general contractors, design team and subcontractors serious financial and liquidated damages with the financial institutions and also from the city since the project was also affiliated with the New York City Housing Authority.
Since this project was facing winter delays with the EIFS installation and all those trades that would follow the EIFS, such as site work, Elite Wall Systems had to come up with a solution. Sangiorgi had learned over his 38 years in the industry that he can be an efficient problem-solver.
Sangiorgi and his team of project managers, supervisors and foreman quickly came up with a solution to solve the problem since waiting until to the springtime was out of the question. Sangiorgi relied on his many years of experience in the industry field installing EIFS and also thought about his prior years of installing prefabricated curtainwall systems with his first employer Donaldson Industries back in 1987, when panelization was very popular. Since a full-blown pre-fabricated curtainwall system was out of the question, time was of the essence, plus the cost of doing something like that would have doubled or tripled the cost of the project and would take months just to do the engineering. Sangiorgi is typically cautious using panelization because of the problems with lots of caulk joints that eventually don’t hold up due to owners not maintaining the caulk joints. This can lead to water penetrating the envelope and causing issues.
Sangiorgi knew that he had to create a prefab EIFS panel indoors (but not allow for many caulk joints and seams). This was the design team and owner’s main concern, as it was Sangiorgi’s also. So he came up with a concept he coined the “hybrid EIFS panel,” which would allow him to work through the winter, prefabricating smaller lightweight panels that would not require any cranes or mechanical lifts to set in place.
Sangiorgi, along with his team of project managers and supervisors, some with architectural and engineering backgrounds, presented a concept to the owners, GC, design team and Sto. Within two weeks, Sangiorgi and his team of professionals presented CAD shop drawings with details and did a mock-up in place. Because of his long-time relationships, trust and loyalty to the owners, GC, architects and manufacturer, the entire project team supported and backed the idea. Within weeks, Elite Wall Systems turned floors 2 to 12 into a seamless prefab hybrid EIFS panel and was substantially complete by April 2024, and then thereafter completed the 13th floor bulkhead, hoist area and the ground floor lobby area starting in the spring and finishing the project in time for its first TCO walk through with the NYC Building Dept.
Sangiorgi says, although it wasn’t that large of a project for him (approximately 60,000 square feet) as compared to some of his larger projects he’s done, it was definitely one of the most challenging.