Managing interior job site conditions can reduce the cost of replacing wet materials. By Peter V. Burns
Tools to Control Interior Conditions During Construction
xxxxxxxxxxxxxxx By xxxxxxxx
h2 - xxxx
h3 - xxxx
H1 headline
Measuring and controlling interior environmental conditions during construction in general, and specifically during gypsum wallboard finishing, has gained a heightened awareness and new solutions. Developers/owners and design teams are routinely creating and implementing construction moisture management plans that evaluate and mitigate moisture risks. These plans take into consideration:
- The local climate and the construction schedule.
- The need for temporary enclosures.
- Equipment to measure and record the following:
- Interior air temperature.
- Relative humidity.
- Dew point temperatures.
- Surface temperatures of moisture-sensitive materials.
- Standing bulk water.
- Equipment to condition the interior work areas.
- Heat.
- Humidity control.
- Ventilation.
- Budgets sufficient to fund requirements.
Recent changes to industry standards and guidance documents discuss interior environmental condition requirements for GWB finishing. ASTM International and the Gypsum Association set two such standards.
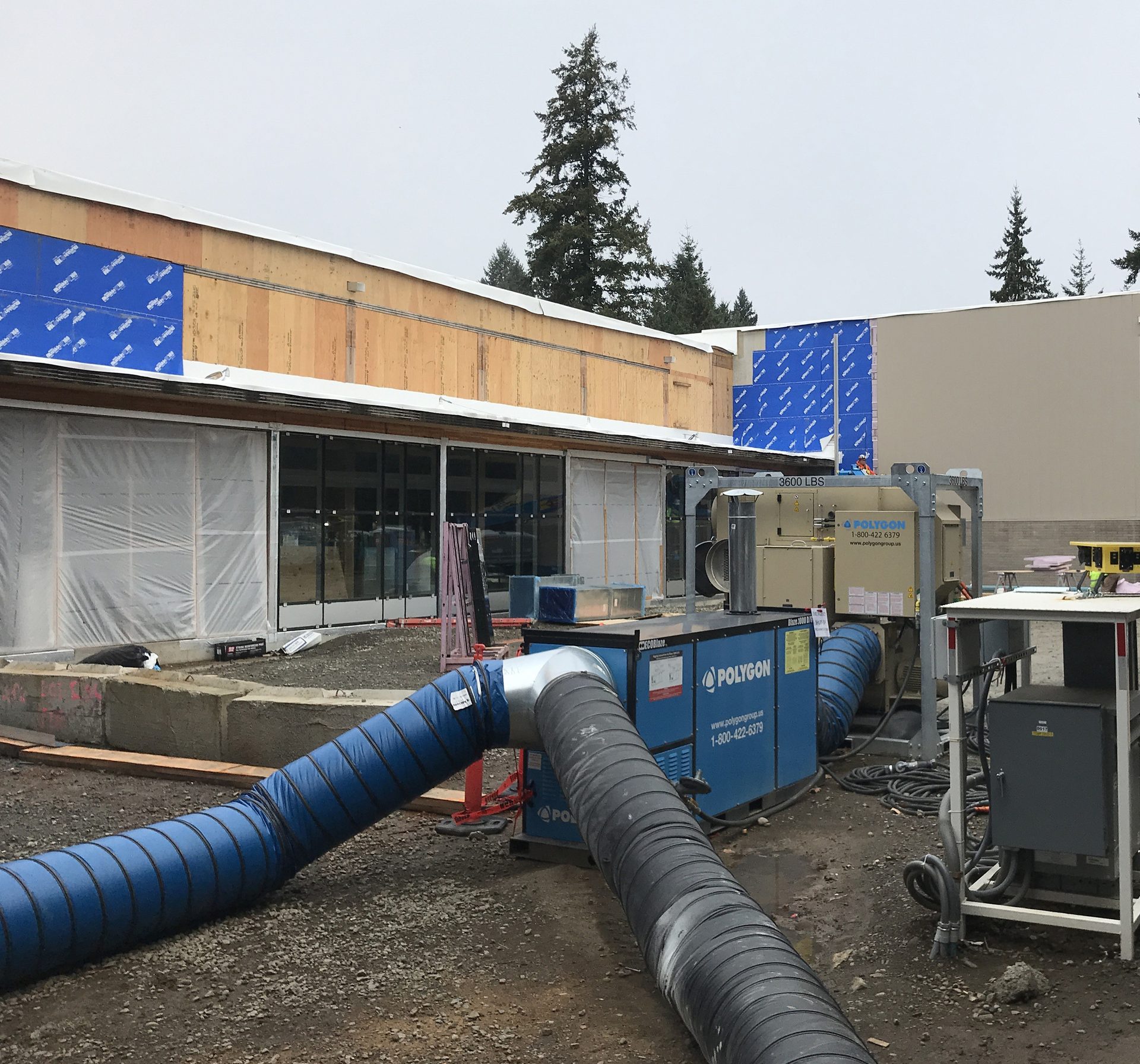
ASTM C840-2020
4. Environmental Conditions
4.1 Application of Gypsum Board, Joint Treatment Materials and Adhesives — Room temperature shall be maintained at not less than 40 degrees Fahrenheit (4 degrees Celsius) during application of gypsum board except when adhesive is used for the attachment of gypsum board. For the bonding of adhesive, joint treatment, texturing and decoration, the room temperature shall be maintained at not less than 50 degrees Fahrenheit (10 degrees Celsius) for 48 hours prior to application and continuously thereafter until completely dry. See X7.7 for additional detail regarding environmental control during the installation and finishing process.
X7.7 Environmental Conditions
X7.7.1 — The potential for finishing and decorating problems are minimized when temperature, humidity and airflow remain constant and as close to occupancy environmental conditions as possible. A minimum temperature of 50 degrees Fahrenheit (10 degrees Celsius) should be maintained continuously for 48 hours prior to and throughout the finishing process until applied materials are thoroughly dry.
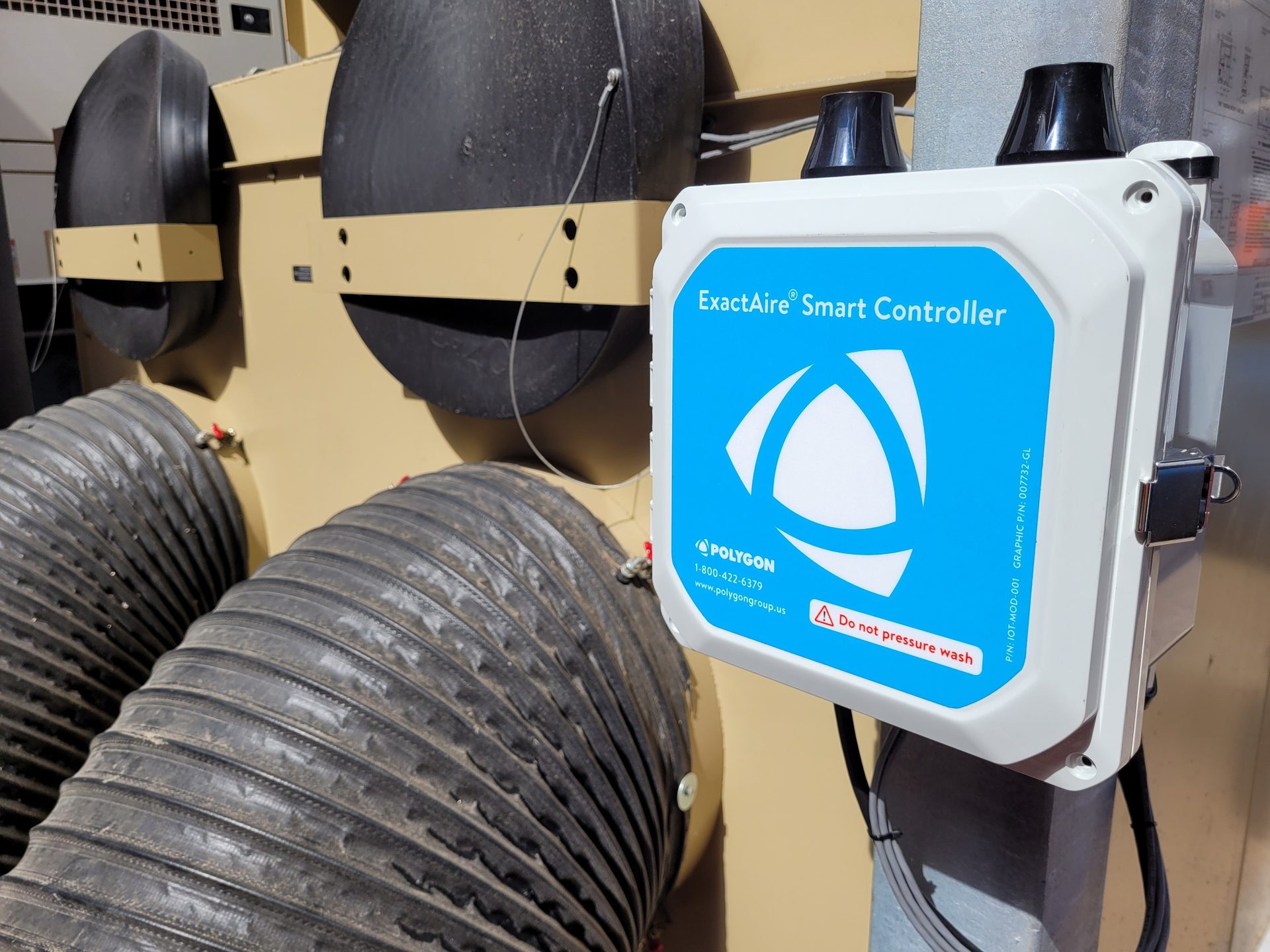
The Gypsum Association’s GA 214- 2021
Section V has the same requirements but also states that the interior environmental conditions shall be maintained until the building is occupied.
“Environmental Control. The potential for finishing and decorating problems are minimized when temperature, humidity and airflow remain constant and as close to occupancy environmental conditions as possible. A minimum temperature of 50 degrees Fahrenheit (10 degrees Celsius) shall be maintained continuously for 48 hours prior to and throughout the finishing process until the project is completed/occupied.”
USG’s guidance document titled “Evaluating Job Site Environmental Conditions” discusses interior job site environmental conditions that contribute to thermal and hygrometric movement of GWB. USG recommends that an interior temperature of 55 degrees Fahrenheit should be maintained during the entire finishing process and until the joint compound is completely dry. USG also recommends that no joint compounds or coatings should be applied unless the surface temperature of the GWB is at least 5 degrees Fahrenheit above the dew point and that surface temperatures must be maintained above the dew point throughout the curing process.
To comply with industry requirements, the following is needed:
- Permanent or temporary enclosure elements need to be in place. Open buildings are uncontrollable.
Measurements of interior environmental conditions.
- Conditions cannot be fully understood and controlled if unmeasured and unrecorded.
- Measurements need to be taken continuously, 24/7.
Ability to respond rapidly to changes in conditions by mechanically controlling interior environmental conditions.
- Automated heat and dehumidification systems can rapidly respond to changing conditions.
Polygon, a leader in engineered, temporary climate control, operates throughout the country and Pacific Northwest. The company, previously known as Munters, pioneered the use of desiccant dehumidification more than 60 years ago, has continued to advance the industry with the latest technology and offers the most energy-efficient dehumidification and temperature control equipment available. Their team has recently developed wireless monitoring systems that continuously measure and record interior job site environmental conditions and can then transmit real-time data to a fully automated mechanical heat and dehumidification system to control conditions.
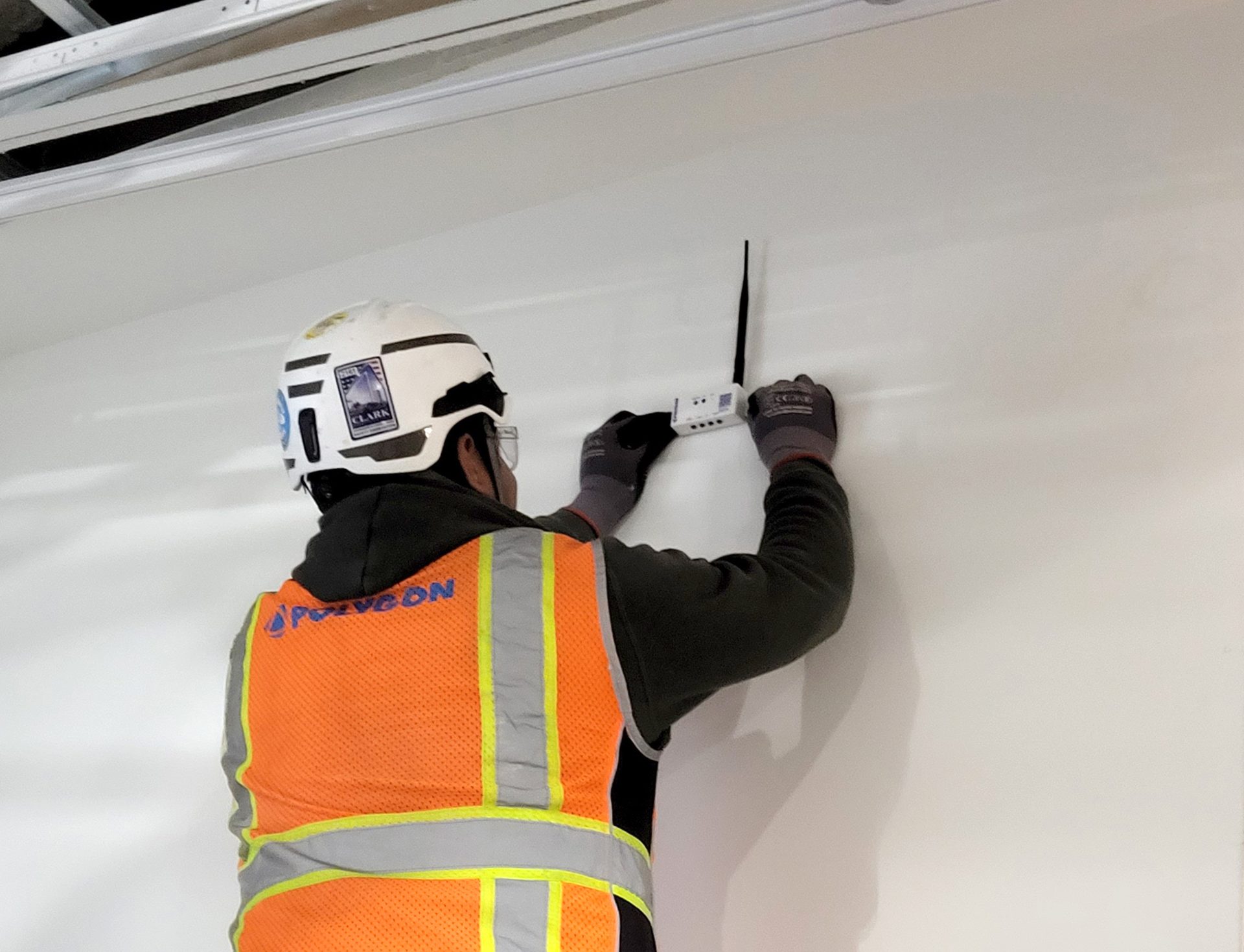
Smart Climate Control for Job Sites
I reached out to Polygon’s Director of Engineering and Technology, David Simkins, for an update on what’s out in the field today and what might be available in the future. Contractors are faced with a plethora of options on the market to measure climate conditions. These range from simple handheld devices to off-the-shelf data loggers. Simkins explained that where Polygon’s clients are most successful is the intersection between real-time data and active environmental control.
“We have spent over 20 years developing our IoT solutions,” Simkins says. “Our model is to be sensor-agnostic: taking third-party sensors, integrating them into our platform, feeding our equipment with real information and modulating equipment exactly when it’s needed.”
Polygon breaks down a smart climate system in a few pieces:
- Connected sensors that continuously measure parameters like temperature, humidity, surface temperatures and dew point.
- User applications for data visualization, documentation and alerts.
- Right-size climate control equipment outfitted with a smart controller to use data and modulate interior conditions.
“This the direction of the industry,” Simkins comments. “We are constantly taking in requirements, finding sensors, demonstrating capabilities and delivering that out to our clients. It is one thing to know the conditions at a given point in time, but it is powerful when you see them holistically and can do something about it.”
Polygon recently announced the release of a new sensor that is a “Swiss army knife” of their ExactAire sensor suite. The Multi Sensor is small, flexible and able to do T/RH, leak detection, concrete or wood moisture equivalent or surface temperature. When coupled with an active equipment controller, it gives developers/owners, design teams and installing contractors 24/7 visibility and confidence in the interior environmental conditions of the working space.
Some of the ways Polygon’s clients use the data and technology include:
- Identifying the starting point and predicting dry times.
- Maintaining or accelerating the drying schedule.
- Mitigating equipment performance issues that can affect installed materials.
- Identifying if interior conditions change due to a breach in the temporary enclosure or occupant behavior (e.g. window left open).
- Identifying problem areas and getting corrective actions in place.
- Reducing the risk of microbial growth by maintaining proper interior conditions.
- Documenting for all parties that proper interior environmental conditions were maintained according to the project and materials manufacturers’ requirements.
The ability to measure and record interior environmental conditions on job sites and then have the mechanical systems responding with adjustments to temperature and humidity levels in real time is a capability long overdue in construction. We expect this in our homes every day, 24/7. We should expect no less on job sites, where time is critical and costs to repair or rework materials damaged by moisture are high.
References
- xxxxxxxxxxx
- xxxxxxxxxxx
Images courtesy of Northwest Wall and Ceiling Bureau.
Peter V. Burns is the director of technical services for the Northwest Wall and Ceiling Bureau. The NWCB is a nonprofit trade association for the wall and ceiling industry, serving a wide-ranging membership of contractors, manufacturers, dealers, labor organizations and other professionals in the industry.
xxxxxxxx