Density and Mass
Boston’s first ground-up mass timber Passive House project integrates innovative 5-in-1 wall assembly.
Project Notes
Location: Boston
Building Type/Details:
• Multifamily mixed-use
• Mass timber
• 43,000 square feet | 7 stories | 34 units
• Passive House pre-certified
Sales Representative: façades X
Architect: Monte French Design Studio
General Contractor: Haycon Inc.
Installer: ONTIME Construction Services
Structural Engineer: H+O Structural Engineering
Products: ArmorWall Plus Fire-Rated Structural Insulated Sheathing as part of DuPont ArmorWall Systems
Currently under construction and on track for occupancy in late 2022, 11 E Lenox is a seven-story, 34-unit multifamily building in Boston’s Roxbury neighborhood. The project was conceived in 2019, when developer Haycon was looking for a cost-effective and environmentally sustainable solution to stay within Boston’s height limits for mid-rise construction. The building’s innovative design removes the need for a podium or additional fireproofing, resulting in a sturdy, fire-resistive, energy-efficient, comfortable and cost-effective structure that’s beautiful inside and out.
This project is the first ground-up mass timber Passive House project in Boston. Well before the launch of the Boston Mass Timber Accelerator Program, mass timber was selected for the project to help achieve its sustainability goals. Building with mass timber results in lower embodied carbon compared to other traditional materials. But the project team didn’t stop there. The project is pre-certified and expects to meet PHIUS+ 2018 standards, which require advanced energy efficiency measures that benefit the building owner and occupants through passive design and high-performance construction methods.
After the project’s architecture firm, Monte French Design Studio, and other project partners conducted extensive research on mass timber and completed feasibility studies for the project, construction began in June 2021.
DuPont ArmorWall Plus Fire-Rated Structural Insulated Sheathing was specified for the project to realize the 5-in-1 system’s many benefits, including labor and schedule savings, air, water and fire resistance and structural support for cladding materials.
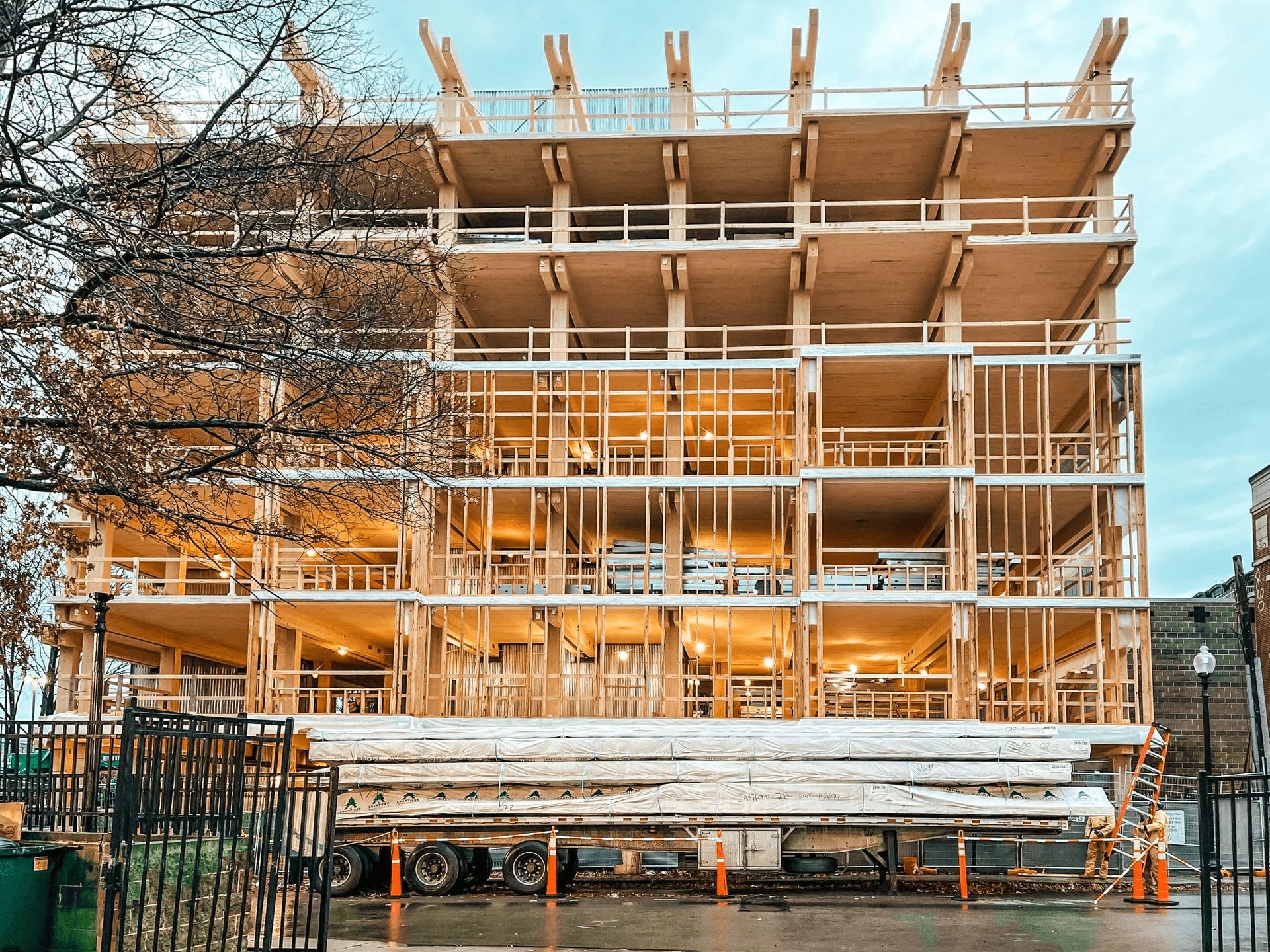
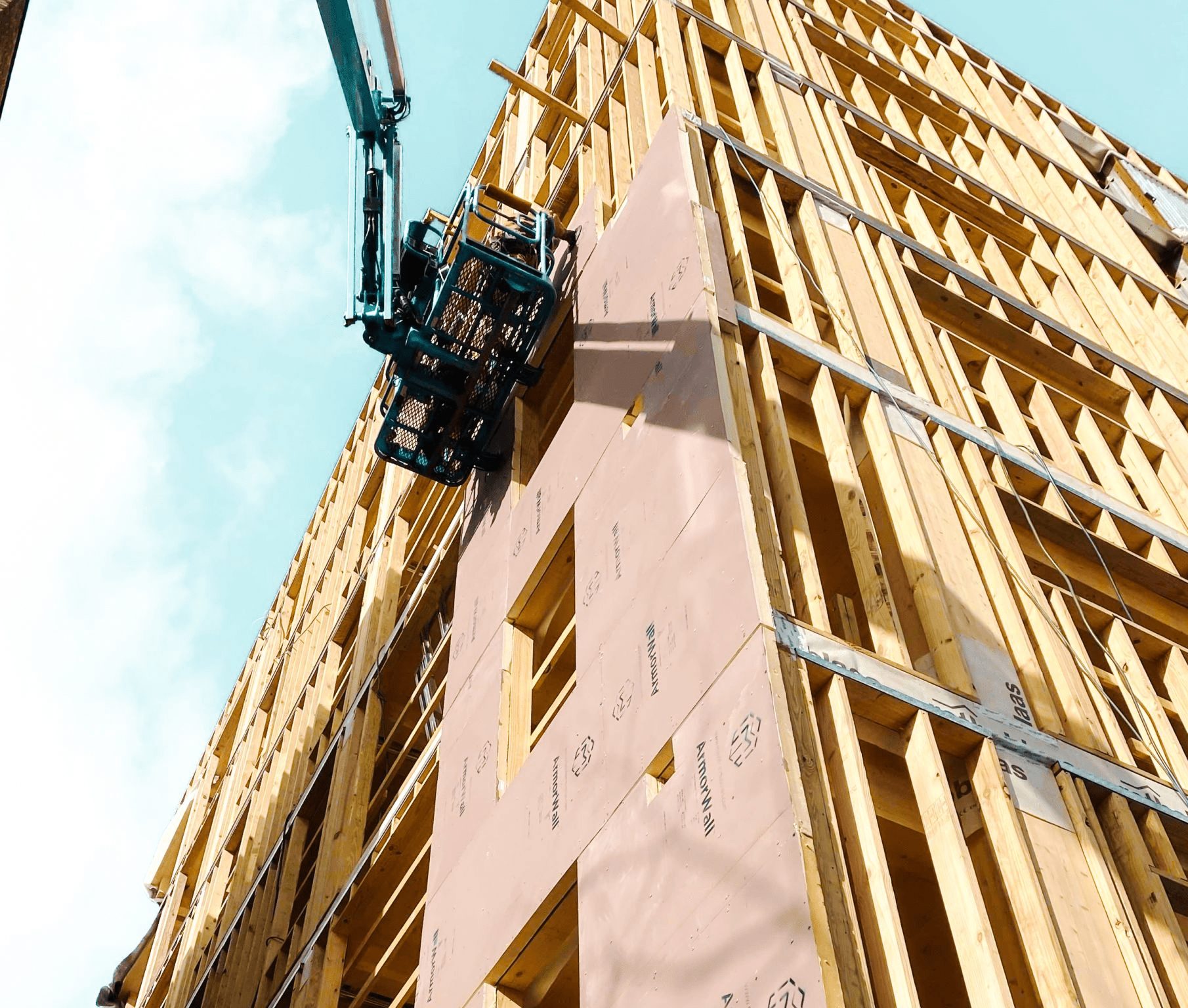
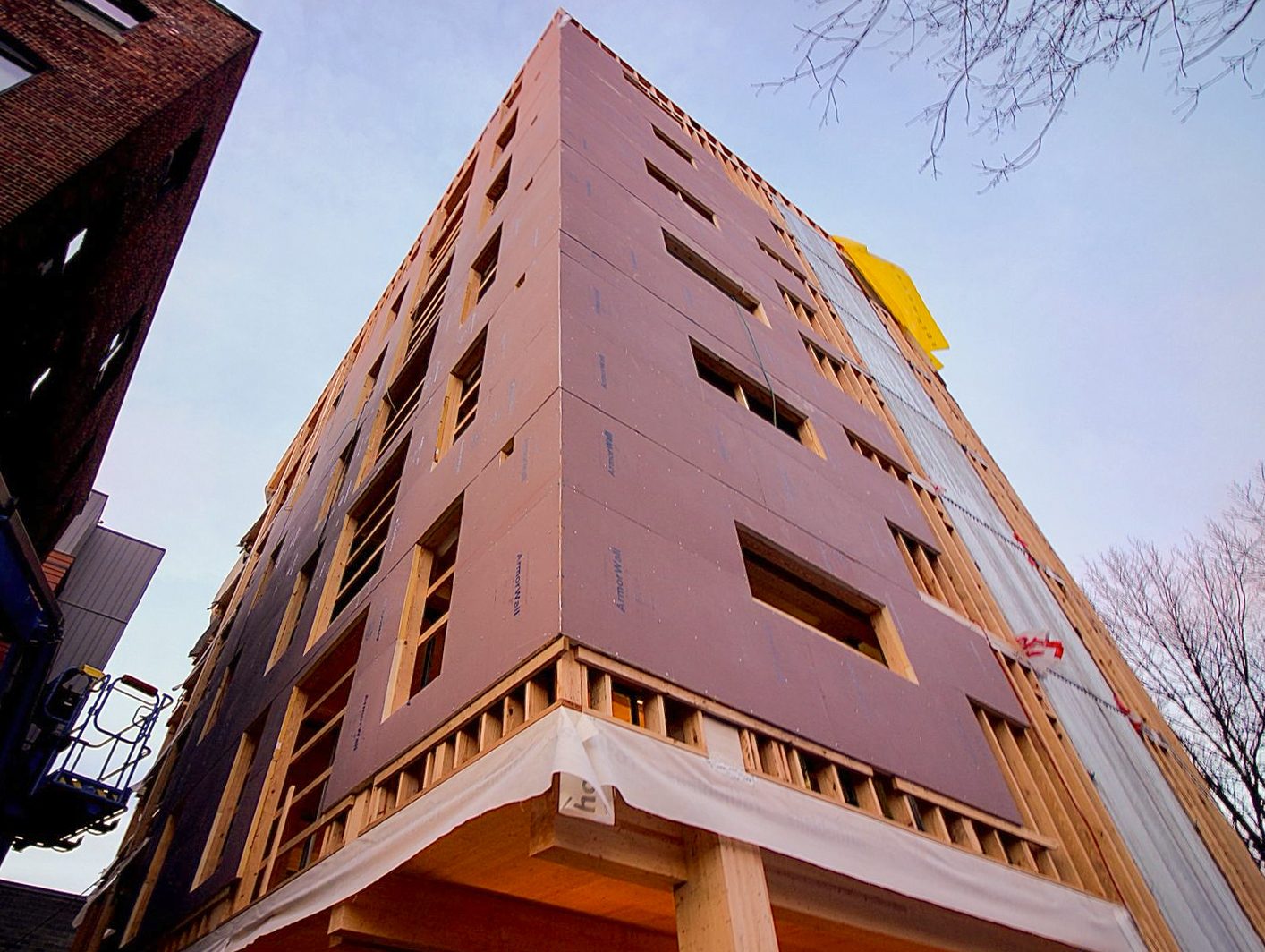
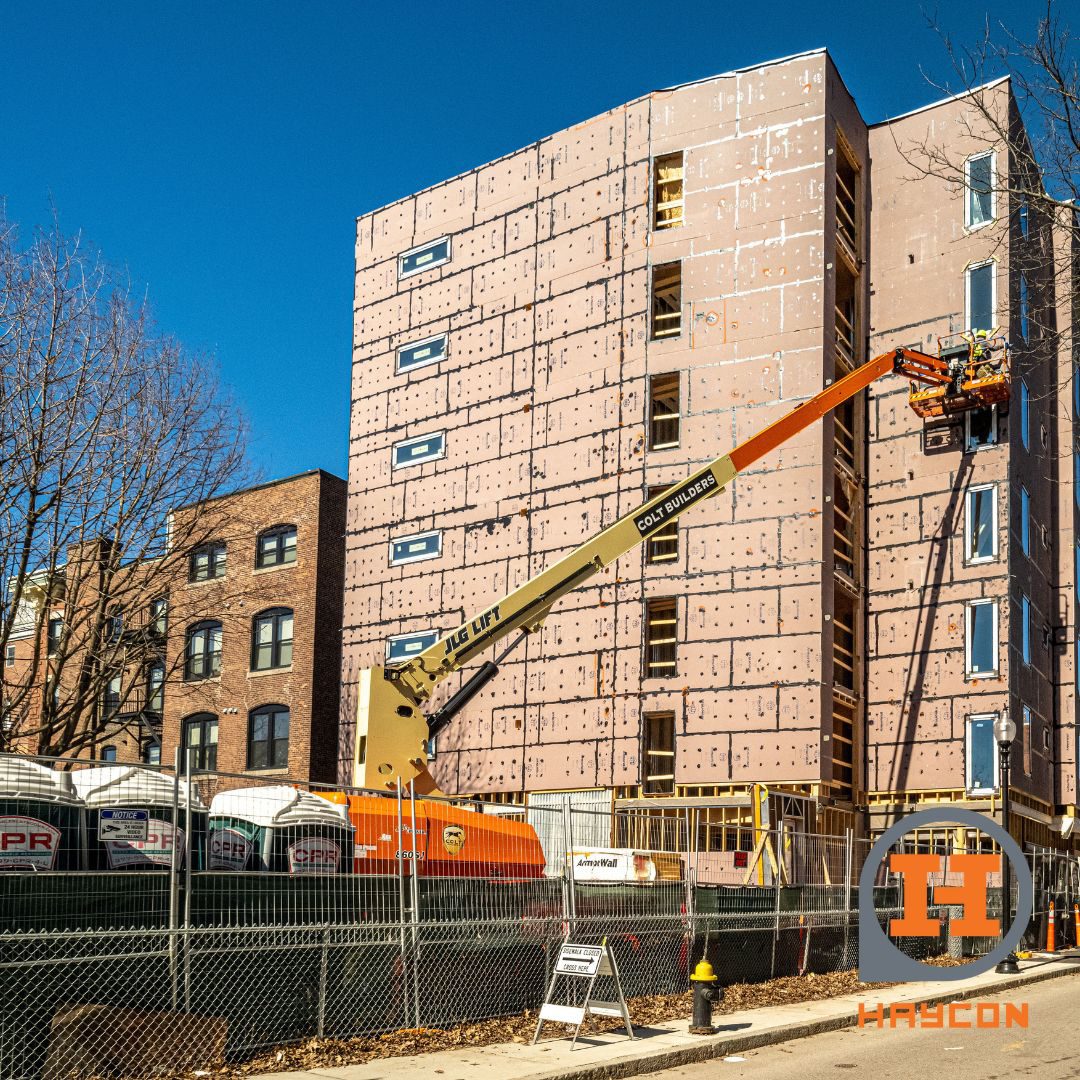
An Innovative Wall System for an Innovative Project
Selecting the right exterior wall system for an innovative project like this required advanced understanding and application of building science and installation innovation by the team, in part due to the project’s small physical footprint in a bustling neighborhood. To address these needs and provide many other benefits, the wall system was specified in late 2020, well before construction began.
“I was first introduced to the product working at Monte French Design Studio through our local rep, façades X, in trying to develop a façade system that would work on this building,” says William Lee, project architect at Monte French Design Studio. “11 E Lenox is the first ground-up, new mass timber and Passive House project in Boston. It is a structural insulated sheathing, which means that we can direct-apply cladding and fenestration to it without the need of additional girts and trades on-site—which saves us time, labor and ultimately, money.”
The systems utilize patented fusion technology to fuse the fire-resistive magnesium oxide structural sheathing layer to the high-performance poured polyurethane insulation layer, which creates an ideal structural substrate for many types of cladding attachment. Additionally, all panels arrive to the job site with a factory-applied, high-quality air- and water-resistive barrier that eliminates the need for additional field-applied coatings or wraps.
One issue that the project team won’t have to worry about is the degradation of the building envelope during construction and over the life of the building. This can occur when manufacturers use glue or lamination to bring together the insulation and sheathing components in their products. Over time, moisture intrusion can break down this connection and cause degradation of the building envelope.
“The fused design of the product essentially eliminates any long-term potential for delamination of the polyurethane core and the sheathing,” says Chip Bisignaro, building envelope specialist at DuPont.
“Our expectations on this project are to meet and exceed Passive House requirements – and part of that is maintaining continuous thermal and air barrier continuity,” Lee says. “11 E Lenox, as a Passive House project, needs to maintain less than .6 air changes per hour, which is incredibly tight.”
Five Wall System Elements Installed in One Revolution
Installation of the 2 3/4-inches thick panels began in February, 2022.
“One of the benefits to using the panels is schedule,” says Patrick Larcom, Haycon Inc. construction project manager for 11 E Lenox. “With every project, we’re able to work with one installer. The one installer is able to install the whole system and we’re left with an end product that covers our water barrier, insulation for the exterior, an airtight layer and also meets our fire code. We definitely plan to use the product on future projects.”
Project leaders knew they would face continued supply chain, labor and other challenges all too common in the construction industry throughout 2021 and 2022. By bringing an innovative and committed building envelope installer onto the project early, the project team was able to plan for schedule, material and labor savings.
“Once our crew learned how to install the system, we were able to cut 50 to 70 percent of installation time compared to other systems,” says Jonathan Barcelos, general manager at ONTIME Construction. “Working with the system is very easy. It’s as simple as cutting drywall, in a sense. We can definitely comply with a variety of details around corners, inside corners and small custom pieces.”
Not Just a Pretty Façade
Interior work on 11 E Lenox began in early 2022 and installation of exterior cladding—a combination of fiber-cement and terra cotta paneling—began in mid-June.
One of the most valuable benefits the system provides to the project is a smooth and consistent structural substrate for cladding attachment that also meets continuous insulation requirements and maintains a one-hour fire rating. The structural properties of the system reduces the need for costly and heavy girt systems that other building enclosure products require. This feature lowers material costs and reduces labor, both of which proved invaluable on the project.