Protection against severe weather starts with what the building is made of. By Maxime Duzyk
Hurricane, Flood and Wind Resistance:
Spray Foam in Commercial Facilities
As global warming and climate change conditions continue to wreak havoc, hurricanes and storms are increasing in both intensity and frequency. Some of the most destructive hurricanes have been witnessed in the past few years. The 2017 Atlantic hurricane season was one of the most disastrous on record. It included Hurricane Maria, which decimated Puerto Rico; Hurricane Irma, which caused extensive damage on the Virgin Islands; and Hurricane Harvey, whose rainfall and cyclone destruction reigned over Texas, Louisiana and the Tennessee and Ohio Valleys. The 2018 Hurricane Florence caused monumental damage and deaths in the Florida panhandle and the Carolinas, and 2019’s Hurricane Dorian was the most intense tropical cyclone and worst natural disaster to hit the Bahamas yet. Most recently, in August 2021, Hurricane Ida left over one million people in Louisiana without power before bringing catastrophic levels of rainfall and flood damage to the northeastern United States. Hurricane Ida created many casualties across numerous states, flooded New York City’s subway system and halted air travel at airports.
In the United States, these storms not only cause general safety concerns but have become top-of-mind for builders and contractors, as well as for owners and managers of commercial facilities who have witnessed the damage that has been incurred. Stanford University researchers recently attributed a $75 billion price tag specifically to flood damage in the U.S. over the past three decades, caused by intensifying rainfall driven by climate change. A report by re-insurance company Munich Re determined that in 2020, the world’s six most expensive disasters occurred in the U.S., the worst of which was 2020’s Hurricane Laura, the strongest hurricane on record to hit Louisiana.
Commercial facilities are, in fact, vulnerable to serious storms and inclement weather. First Street Foundation, a nonprofit research and technology group, asserts that more than 14 million properties across the United States are susceptible to flood damage. Luckily, building material innovations have resulted in options that, when applied properly, can assist in protecting facilities from severe weather events. Closed-cell spray polyurethane foam is one such material. When applied in walls, ceilings, floors and on the roof, closed-cell SPF protects the structure from serious, costly damage.
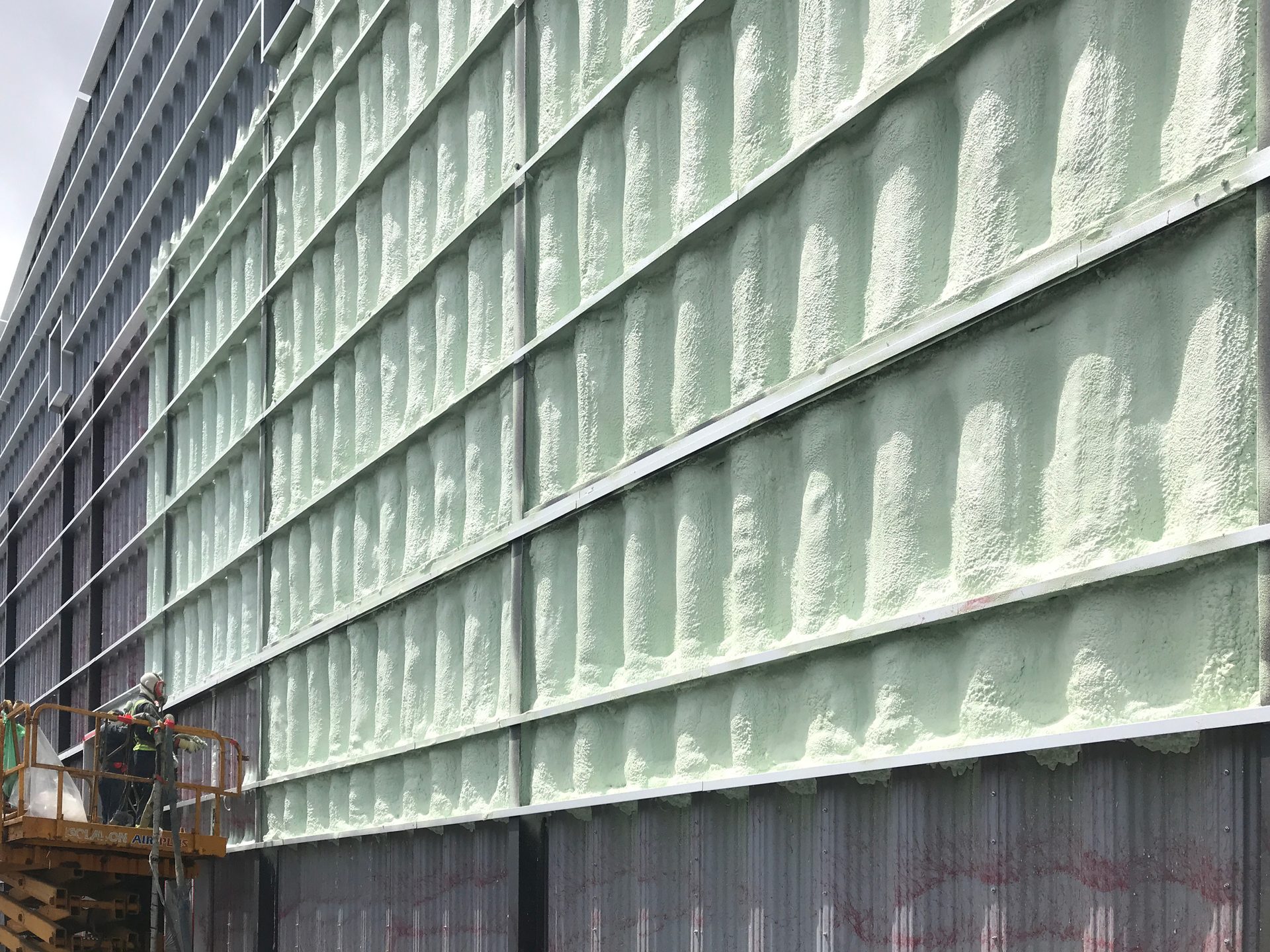
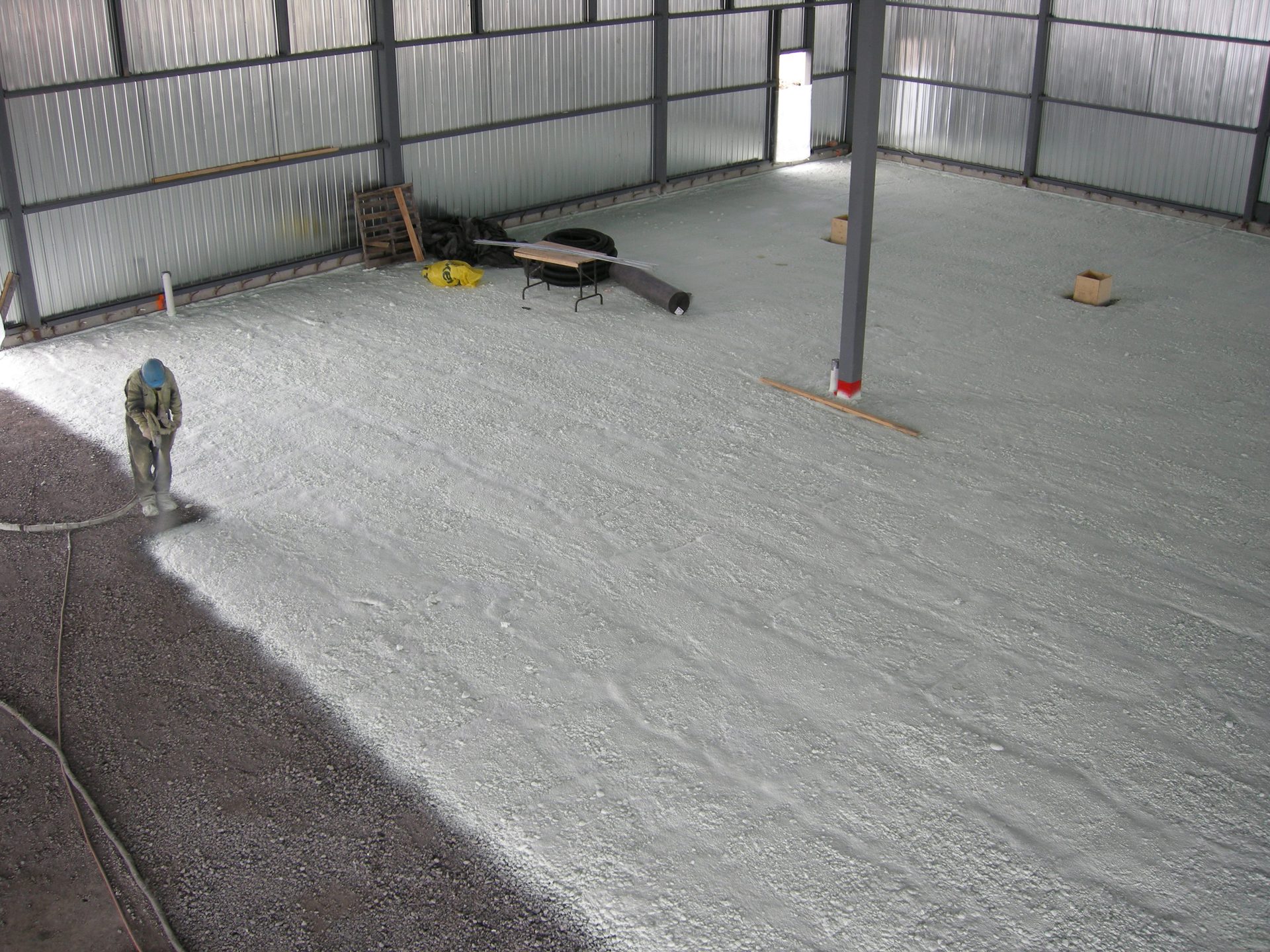
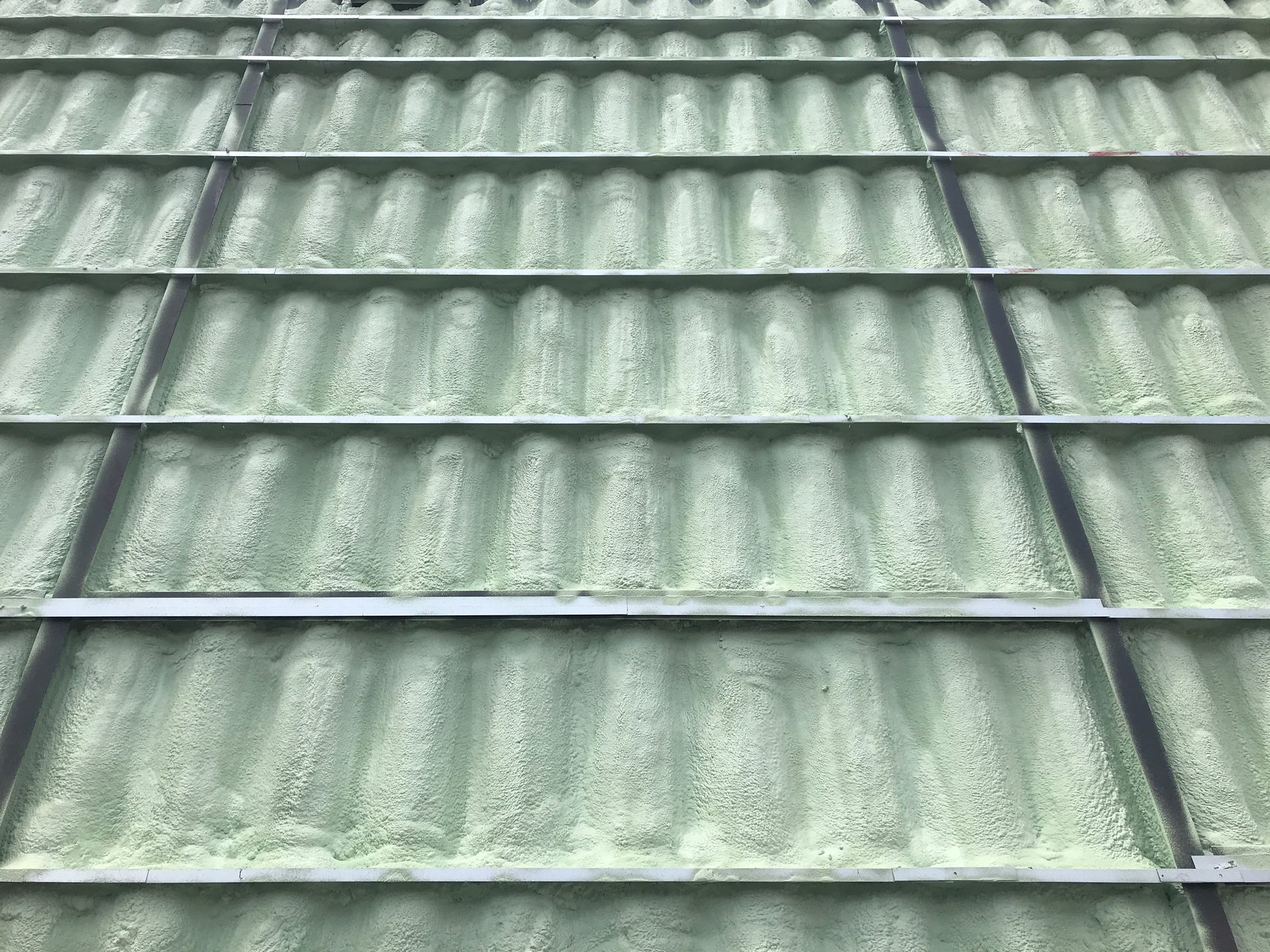
Water-Resistive Barrier & Flood Resistance
Closed-cell spray foam is ideal for continuous insulation applications in commercial structures and can be used in both interior and exterior applications. The material boasts low water absorption and resistance to mold, as demonstrated with ASTM C1338. Closed-cell spray foam excels as a water-resistive barrier on exterior applications and has been tested in accordance with ASTM E2357, with a pressure up to 300 Pa for Air Barrier Assemblies, which included the ASTM E331 (AC71) Water Penetration Testing. The result was no leakage through the spray foam.
When applied in walls, ceilings and floors, FEMA names it a Class 5 material, the highest classification for products, indicating strong resistance to floodwater damage. Class 5 materials do not require special waterproofing protection, can survive wetting and drying, and may be successfully cleaned after a flood to render them free of most harmful pollutants.
As a Class 5 solution, closed-cell spray foam provides both time and money savings for owners of commercial structures that have endured flood conditions. Additionally, while closed-cell spray polyurethane foam may be applied as cavity insulation or as continuous insulation in commercial structures and still qualify as a Class 5 material, it is the only cavity insulation approved by FEMA with the highest floodwater resistance. When applied under slab as insulation, closed-cell spray foam is also flood-resistant.
Structural Strength and Wind Resistance
The application of closed-cell spray polyurethane foam in above-grade walls can also increase the structural strength of buildings and assist with wind resistance. The degree of hardening depends primarily on the strength of the building to begin with. For example, an I-beam modular-constructed metal building with a 22-gauge metal panel will benefit significantly less from an interior application of closed-cell spray polyurethane foam than a post-frame-constructed building with 29-gauge corrugated metal panels will. When installed, closed-cell SPF essentially glues the assembly together, reduces the potential for movement and adds a tensile strength average ranging from 15 psi to 25 psi.
The Spray Polyurethane Foam Alliance conducted racking performance tests in 1992 and 1996, and at Architectural Testing, Inc. in York, PA in 2007. The tests demonstrated that medium density closed-cell SPF installed at 2 pounds per cubic foot increases racking strength by 70% to 200% in wall assemblies sheathed with OSB, plywood, gypsum wallboard, vinyl siding and polyiso board. The research proved closed-cell SPF significantly increased rack and shear strength in both wood and metal construction. Installed SPF also increases the strength of weaker substrates, such as gypsum drywall, vinyl siding and polyiso foam insulation, at a much greater percentage than stronger substrates, such as OSB and plywood. Notably, special bracing for wind resistance is not required for strengthening purposes when using closed-cell spray foam in walls.
Roofing & Wind Uplift
Spray polyurethane foam roofing is also an ideal solution for commercial structures in hurricane-prone regions. It forms a durable, monolithic membrane over the roof and offers a compressive strength of approximately 40 to 55 pounds per square inch.
Spray foam roofing increases wind uplift resistance when installed to the roof substrate and wind uplift protection is even stronger when applied to concrete. The material also resists peeling failure, a result of wind pulling flashings and copings away from a roof’s edges, which can ultimately lead to devastating structure damage. Some high-performance spray foams demonstrate wind uplift resistance by meeting the High-Velocity Hurricane Zone criteria of the Florida Building Code. The material’s ability to withstand leaks due to hail is also unsurpassed.
Notably, a review of roof damage following Hurricane Katrina found that buildings roofed with spray foam performed well without blow-off of the SPF or damage to flashings. The report found that only one of the examined SPF roofs incurred notable damage and concluded that spray foam kept the roofs intact, prevented moisture from entering the buildings and protected the structures from hail and debris.
Images courtesy of Huntsman Building Solutions.
Maxime Duzyk is director of building science and engineering for Huntsman Building Solutions, a global leader in spray polyurethane foam solutions.