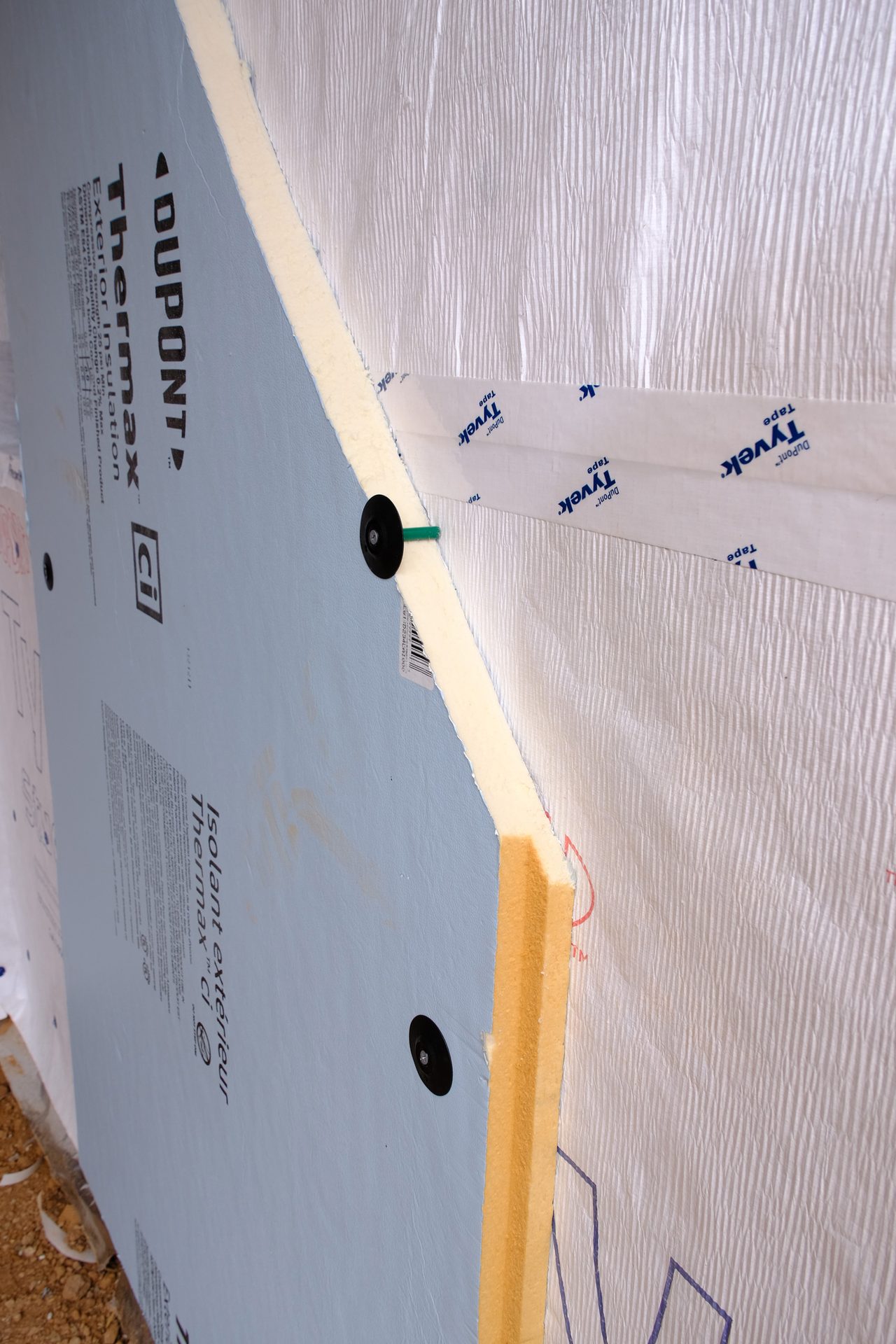
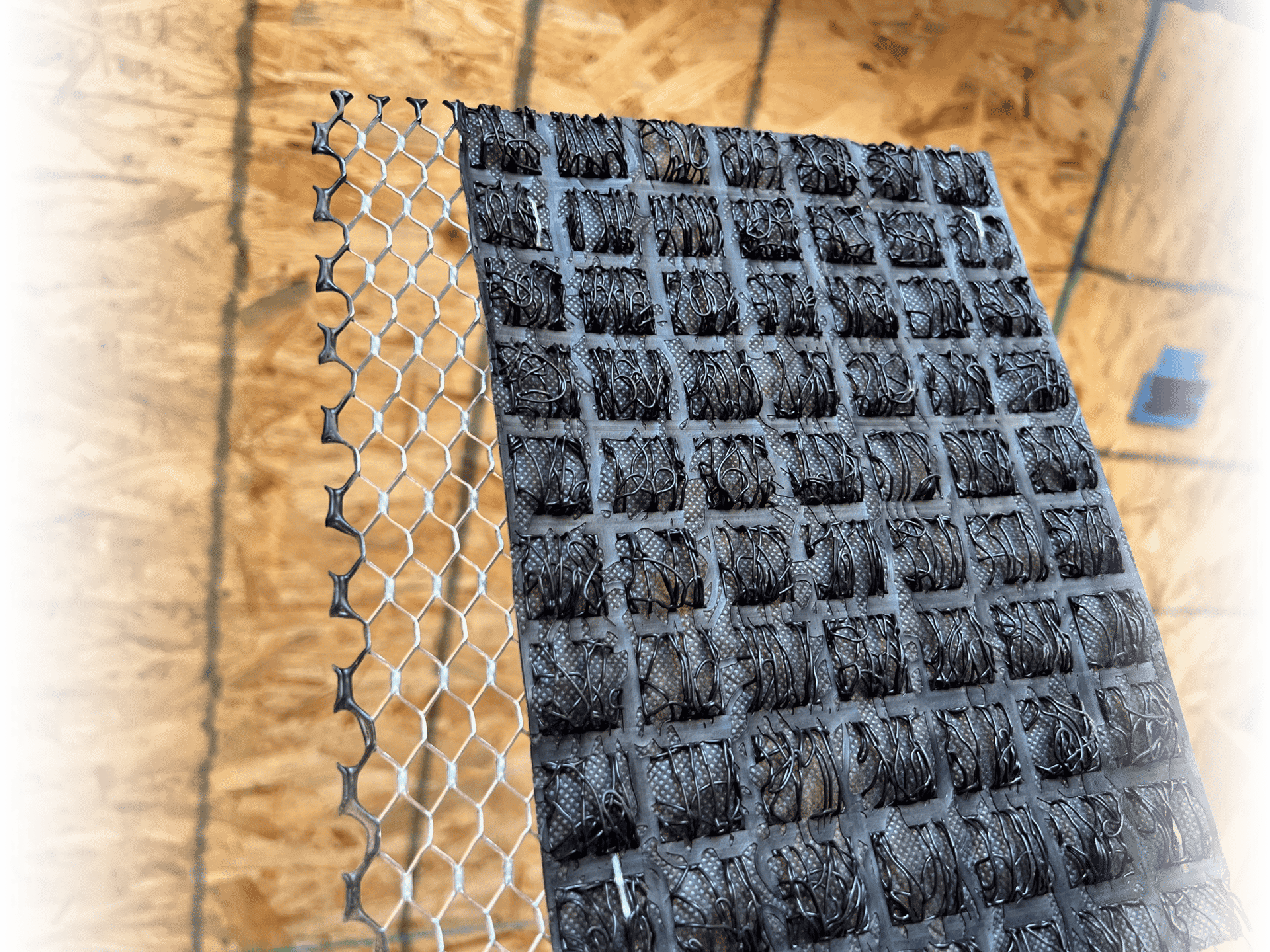
for Water Management for Stucco-Clad Walls
Best Practices
Why using rainscreen lath helps limit water damage in today’s code compliant walls.
By Steve Easley
Why using products with higher R-values helps limit water intrusion. By Steve Easley
Water intrusion continues to be the leading cause of callbacks and construction defects. Prescriptive versions of 2021 energy codes will require continuous insulation in climate zones 4-8. The logic behind this is to reduce the energy impacts of thermal bridging through framing members. On average, homes in the U.S. have 25 percent framing factors. This means 25 percent of the walls are wood and 75 percent are cavity insulation. The R-value of a 2x4 is only 4.38, significantly less than cavity insulation, which has an R-value of 13 for a 2x4 wall. Adding exterior continuous insulation can increase the wall’s R-value by almost 50 percent.
The majority of residential buildings also have wood-based sheathing for structural shear support and wind bracing. The majority of continuous insulation products are low-permeability foam sheathing that get installed over the wood sheathing. If water intrusion gets sandwiched between the foam sheathing and the wood sheathing, which is usually OSB, the OSB gets wet and because the foam is not breathable, the OSB will have little chance of drying out. This trapped moisture can create conditions for mold growth, which can lead to structural decay of the wood sheathing in a fairly short period of time. Needless to say, from a building science perspective, this is not ideal.
So, what do we do when the energy codes and the building codes are at odds? Here are some best practices that I use, that I believe are very effective at preventing water intrusion and dealing with these unintended consequences.
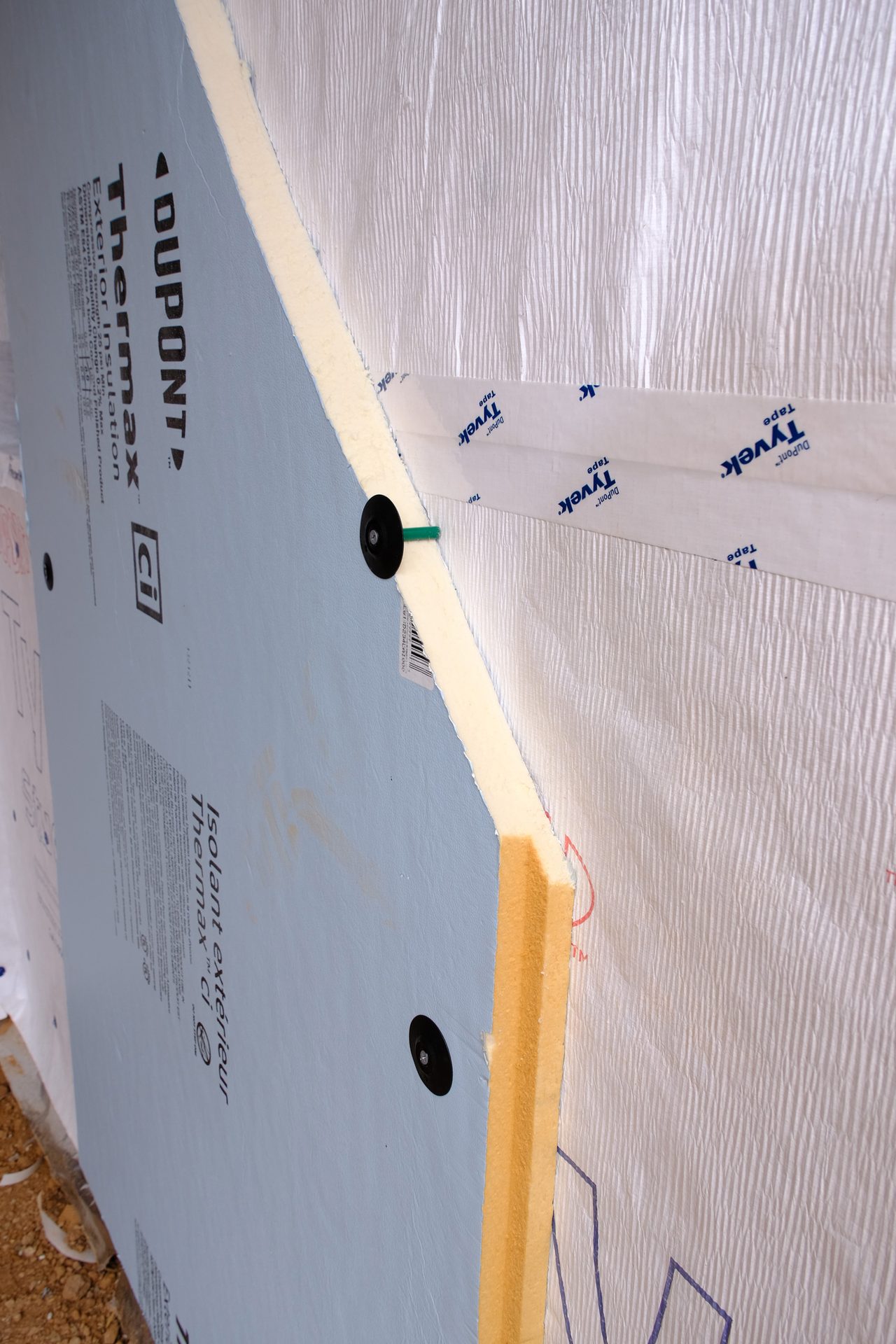
For this project, I used Tyvek DrainWrap over OSB sheathing with R-10 Thermax because I wanted a high R-value per inch. The foam is fastened with grip deck tube seal self-sealing fasteners.
The first job is to make sure that the water never reaches the wood sheathing. This starts with covering the OSB with a high-quality drainage wrap. These are products that have grooves to facilitate drainage. The 2018 IRC requires that walls have a drainage efficiency of greater than 90 percent, as tested by ASTM E 2925. Some specialty drainage wraps have an efficiency greater than 90 percent and drain considerably faster than traditional building wraps.
The wrap should be properly installed and shingled over a perforated weep screed at the base of the wall.
I don’t recommend the practice of just taping the joints of the foam as a primary weather barrier because often, the foam can be wet or dirty, thus the tape won’t stick. If the tape fails, it’s a sure-fire pathway for water to get behind the foam.
For my project, I used a moisture barrier over OSB sheathing with R-10 Thermax because I wanted a high R-value per inch. The foam is fastened with Grip-Deck tube seal self-sealing fasteners (more often, extruded polystyrene or Styrofoam is used for exterior insulation).
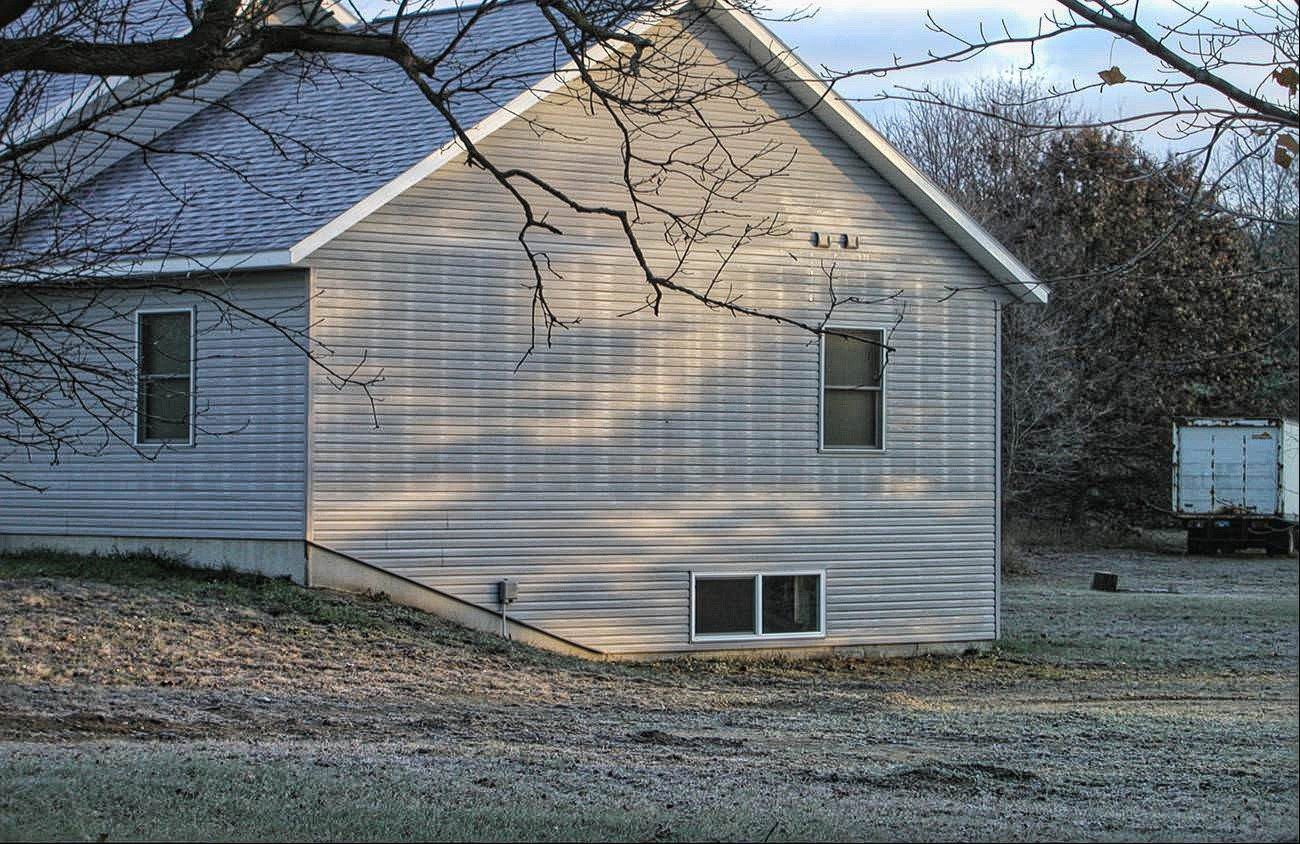
Thermal Bridging: Note the frost is melted at the framing members due heat loss at the framing members.
Rainscreens and Drainage Planes to the Rescue
Stucco by nature absorbs water and can transfer that moisture to building materials in the wall by capillary action. Rainscreens are by far the best practice to prevent water intrusion into walls. Rainscreens have been around since Roman times. Today’s rainscreen systems simply provide a small air gap between the cladding and the sheathing/building wrap. This gap provides two functions. One, rainscreens have a gap (1/4-inch or larger) that creates a space where, if water does get behind the cladding, it drains down the backside of the cladding. Water will not jump across the gap. Two, rainscreens prevent water flow by capillary action. Even a small gap, slightly greater than 1/8-inch, provides a capillary break and prevents water bridging. I believe rainscreens are imperative when building walls with foam over OSB sheathing. Building codes in some states require rainscreens.
The wall system in the house I am building will be 1/2-inch OSB covered in Tyvek DrainWrap. I am installing 1 1/2-inches of R-10 Thermax foam sheathing over the wrap (it’s also acceptable to install the moisture barrier or a stucco wrap over the foam sheathing).
Over the foam sheathing, I'm installing a product called Driwall Lathnet, made by Keene Building Products, a product tested to ASTM 2925 to have 98 percent drainage.
This product combines self-furring metal stucco lath reinforcement with a drainage plane material, with a built-in mortar barrier for drainage and ventilation and the lath holds the mortar. This system provides a 1/4-inch gap between my stucco and foam sheathing. This gap also allows airflow, which promotes drying. This saves labor, as the drainage plane material and lath go up in one step. This product would also work very well with adhered masonry veneer. Fastening the lath and the foam requires thousands of penetrations so I will fasten the foam and the lath with Tube Seal self-sealing fasteners from Tru-Fast to prevent water intrusion at the fasteners.
Images courtesy of Steve Easley & Associates.
Steve Easley is an internationally recognized construction consultant specializing in sustainable building practices, solving building science related problems and helping builders build high performance homes and buildings. In addition to consulting, he provides seminars nationally, educating building industry professionals and their trade partners. His work focuses on increasing quality of construction, sustainability, performance, and reducing costly mistakes that lead to construction defects and call backs. Easley's mission is helping industry professionals build and remodel structures that are durable, energy efficient, healthy and comfortable to live and work in.