The benefits of using polyiso insulation. By Jen Frey
The Good, Better and Best Solutions for an
Effective and Code-Compliant WRB
It’s relatively cold across the country right now, and while many areas of the nation will deal with snow that comes with the cold, much of the south and western parts of the country will be living with typical winter rain. With that in mind, heading into the slower construction season provides a perfect opportunity to take a closer look at the evolution of material options for water-resistive barriers. The number of code-compliant WRB options available to specify have grown over the years and as building science advances, it is always a good idea to evaluate this crucial element of a wall system.
A water-resistive barrier is a critical component of an effective wall system that protects against water intrusion that can get behind the exterior cladding, protecting the structure and its interior. WRBs are universally specified in commercial and residential wall construction and have been required by the International Building Code and the International Residential Code for decades.
Water can be one of the most destructive elements in the deterioration of any building over time. Innovative wall designs can add complexity to a wall design and make it difficult to balance compliance for building code, energy and long-term performance. However, building codes can be confusing as to how they define a WRB. The IBC defines a WRB as “one layer of No. 15 asphalt felt ... or other approved materials” providing a continuous layer of protection behind the exterior cladding. When considering the various layers of protection necessary for a high-performing wall, the opportunity to consider alternative, value-add materials becomes intriguing. These other materials offer opportunities to improve performance while simplifying the wall design and still complying with code.
There are many materials other than asphalt-saturated felt that are considered WRBs, including rigid foam insulation, that can be specified and installed within a wall assembly to meet code, yet not all are equal in performance and overall value. We’ll review some good, better and best options, each with their own set of pros and cons to the wall assembly, and also to the architect and installer.
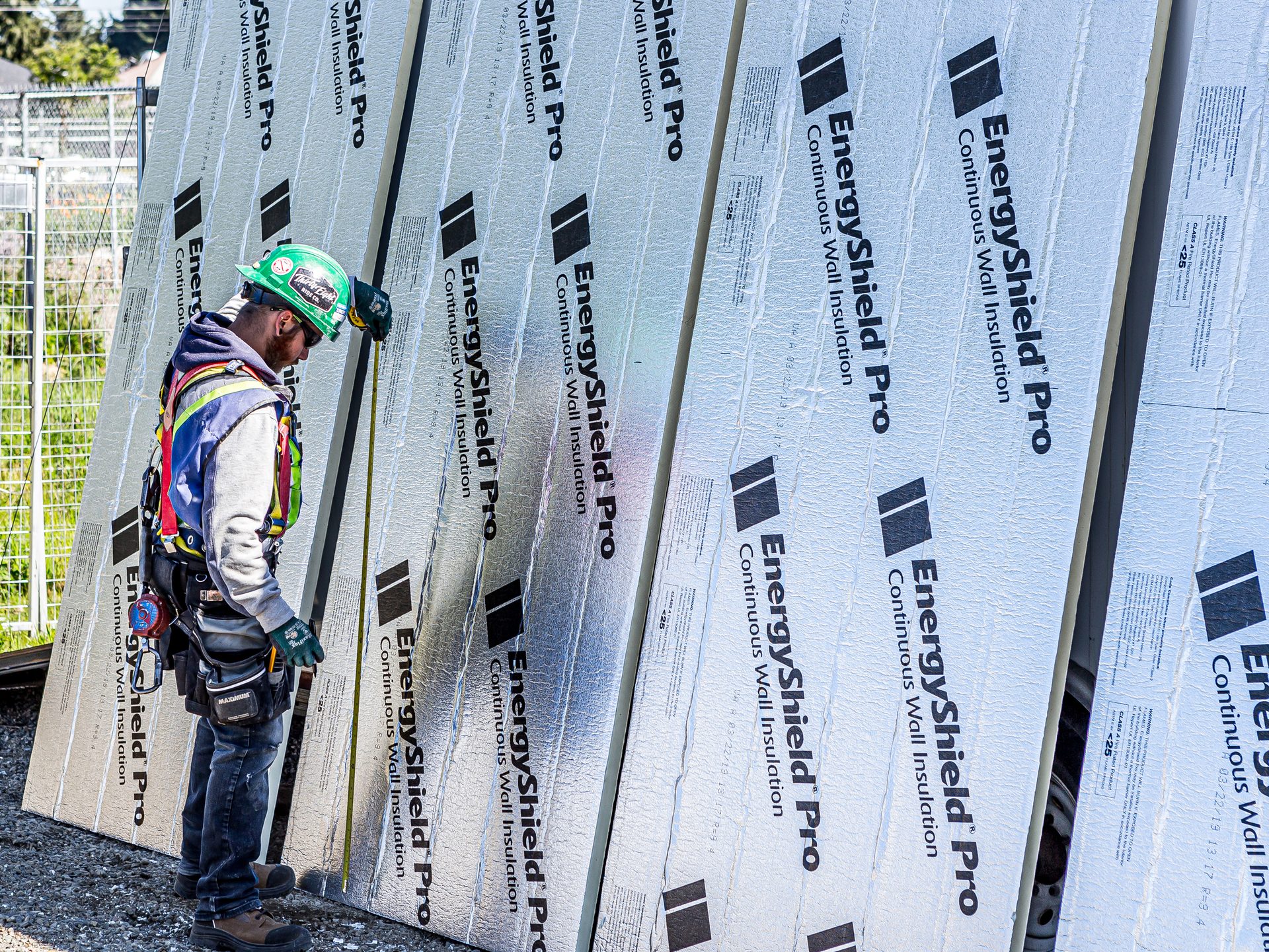
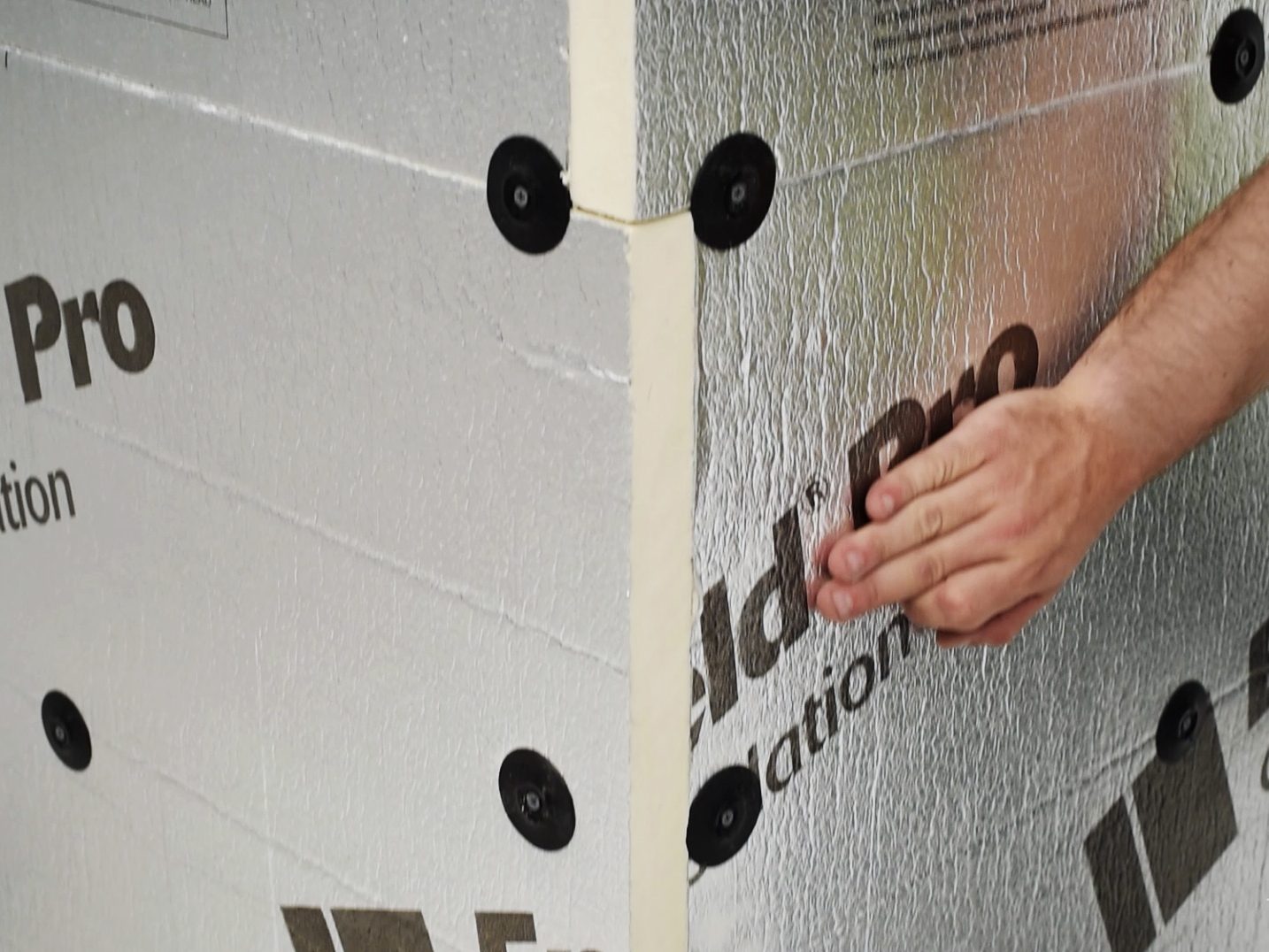
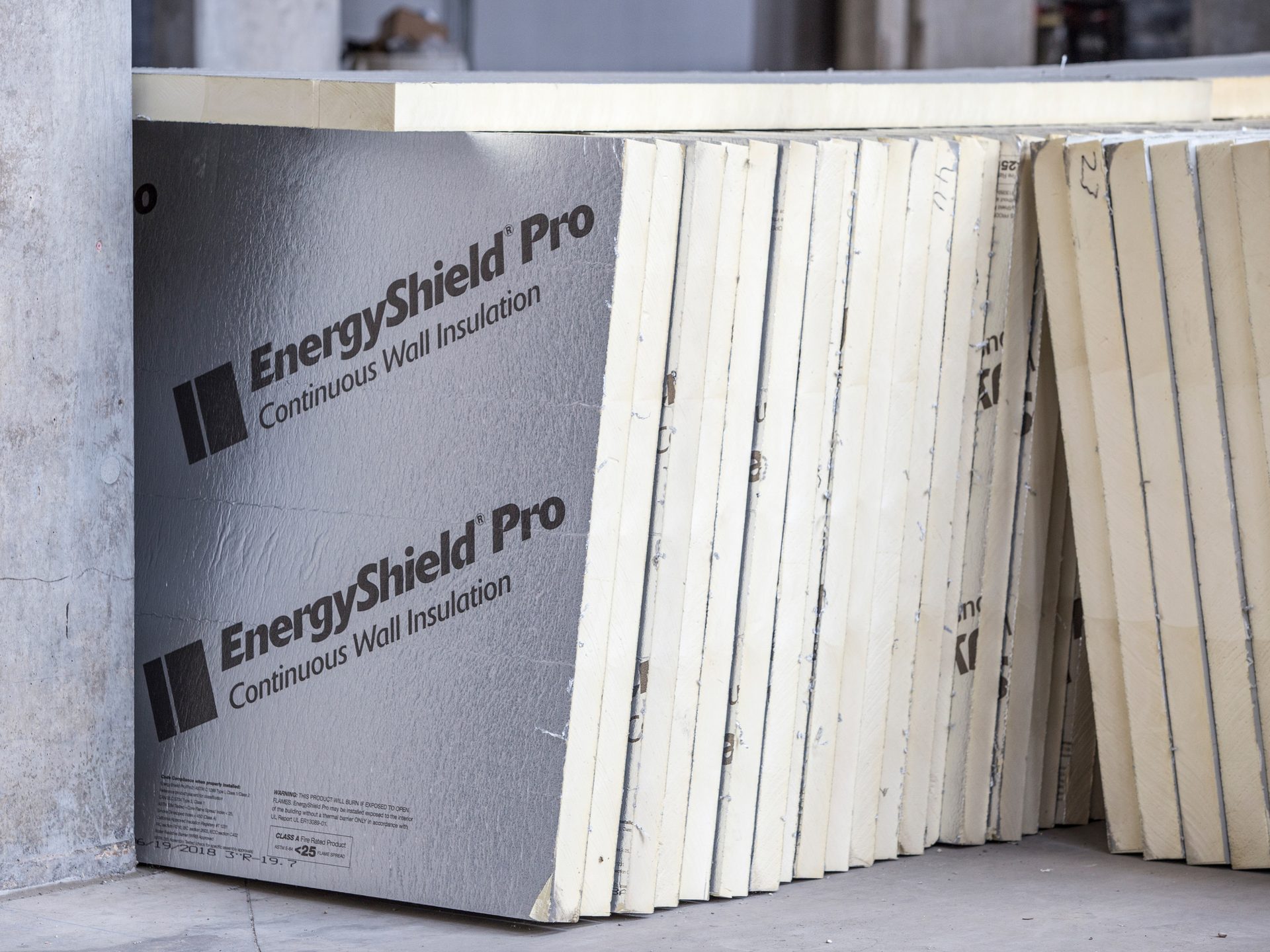
A GOOD WRB: Baseline Protection
Asphalt-saturated felt is called out explicitly in building codes because it’s a good water-resistive barrier that’s been around for over a century. It absorbs water that can breach the cladding and then slowly evaporates the moisture to the exterior. On the downside, it’s heavier to handle than other products on the market and each roll typically covers only 200 or 400 square feet, it requires mechanical attachment points that can theoretically create channels for water or easily tear away in wind events or as it dries out, it can easily rip if not handled carefully and it can get brittle with prolonged exposure to sunlight.
An innovative approach to asphalt-saturated felt introduced around the 1970s is what we refer to today as the ubiquitous “house wrap,” which is one of the most commonly used WRBs that contractors have become very familiar and comfortable installing. These sheet-applied WRBs conform to building codes as an alternative to asphalt-saturated felt. Made from lightweight, synthetic hydrophobic material, it can be either mechanically attached or self-adhered onto the wall and typically comes in rolls offering more square feet per roll, which helps installation efficiency and reduces seams.
Fastener penetrations can still be potential issues for moisture movement, and even though these materials have a better tear resistance than felt paper, we’ve all seen the occasional house wrap blowing in the wind, causing the sheathing to be exposed to the elements.
Self-adhered sheet-applied options are also available, which eliminate the need for mechanical fasteners. In most cases, it’s a good solution, but can often take two people to install. Wind can make installation challenging since it can stick to itself fairly easily. The benefit of the adhesive properties of these materials is that it allows them to seal easily at laps and provide a gasketing effect to protect against water migration from the cladding attachment.
It’s important that the substrate receiving the WRB is properly prepared according to manufacturer guidelines to ensure a strong bond is created. In addition, if not properly rolled following installation, since it is typically pressure-sensitive, or if installed onto a wet or cold substrate, the material won’t stick well and could fall before cladding is even ready.
Overall, house wraps provide good protection offered by a number of brands in a variety of options. Quick can also become a nemesis of good. While these materials are familiar to installers, improper installation can cause unintended consequences, which leads us to other, better options.
A BETTER WRB: 2-in-1 Continuous Barrier with Conditions
With some of the common issues noted with sheet-applied WRBs, an alternative to the traditional house wrap are fluid-applied WRBs. These options can provide a continuous water-resistive barrier and, at the same time, create an effective air barrier as a two-in-one solution. With various products available with different physical properties, fluid-applied WRBs can typically be sprayed or rolled onto the base wall or sheathing. It’s best to find an experienced installer that has been trained to properly apply, to achieve a consistent dry mil thickness that is critical to long-term performance. The benefit is the creation of a monolithic layer achieving immediate performance as a water-resistive barrier and an air barrier.
Like self-adhered membranes, installation can be impacted by weather, temperature or even substrate texture. Job site conditions not only can impact installation of the products, but most of these products can’t be allowed to freeze since they can’t be recovered, so heated storage on the job site may be necessary.
An overall benefit of these materials is their ability to perform more than one function upon installation – both as a WRB and an air barrier. This continuity creates a great protection layer for the building envelope, but can be impacted by installation and job site conditions.
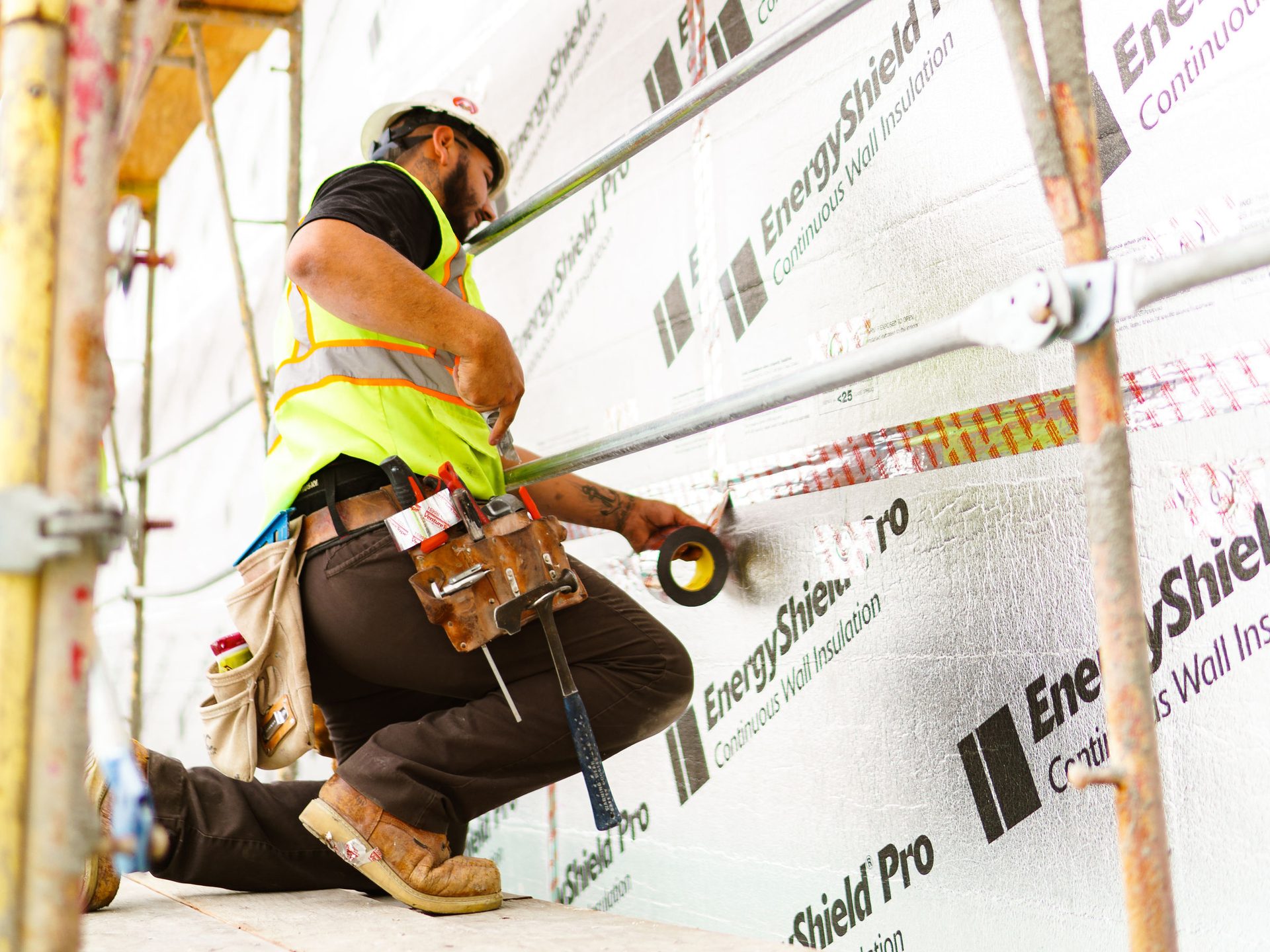
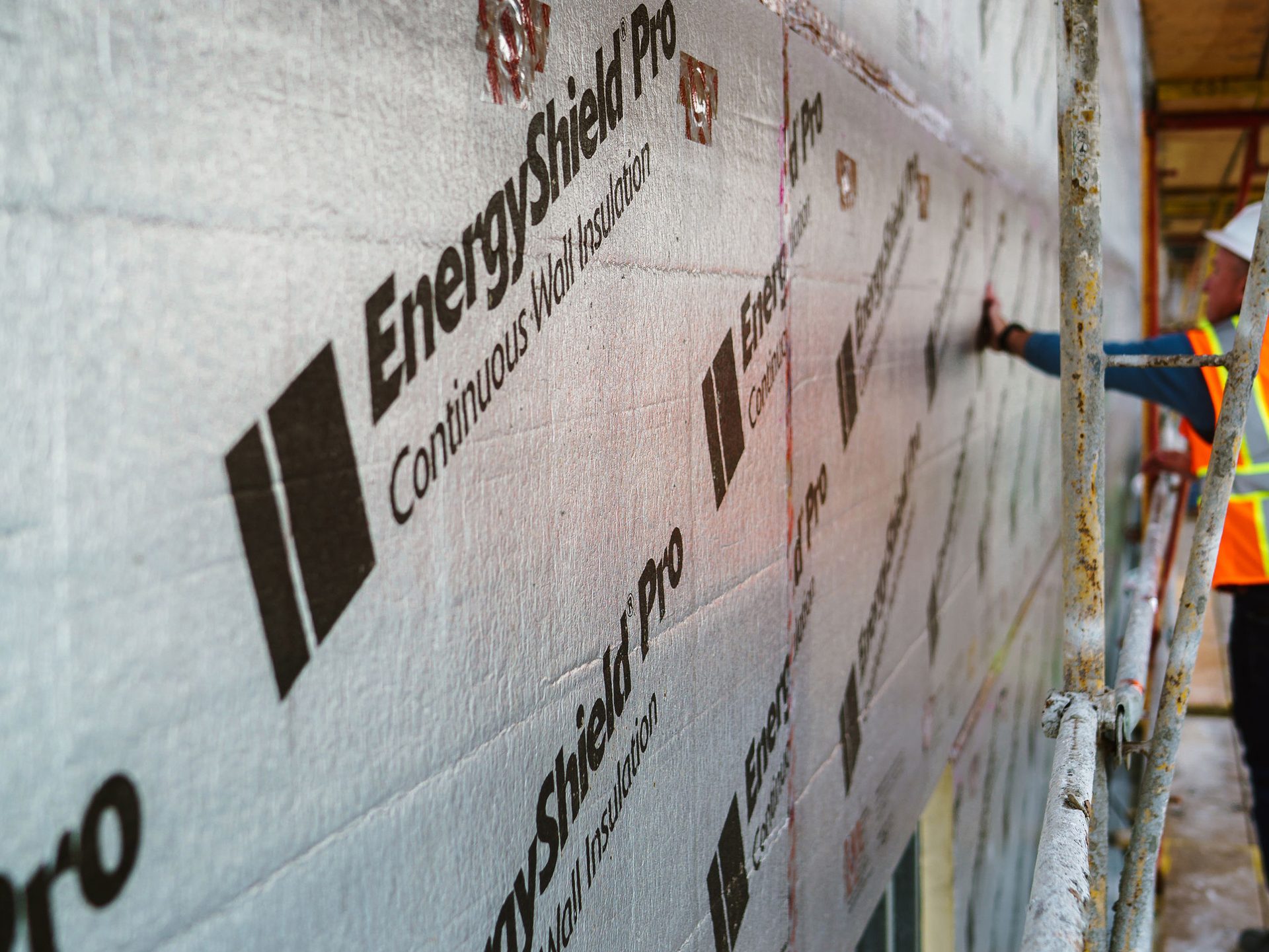
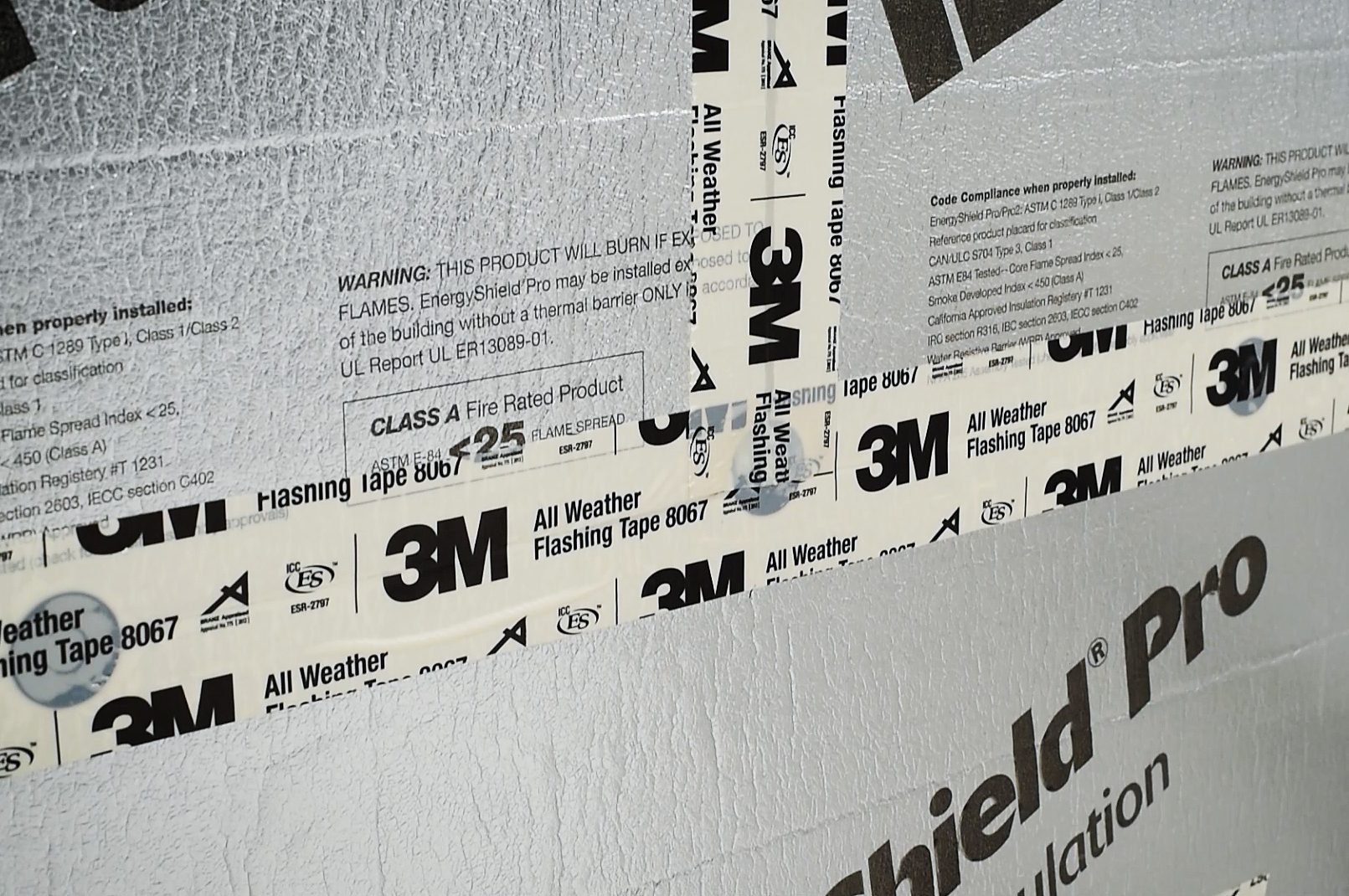
THE BEST WRB: 3-in-1 Protection Simplifies Overall Wall Design
With the evolution of energy codes and building efficiency, it’s likely a wall design will require exterior continuous insulation. As more and more builders are moving at least 50 percent of the structure’s needed thermal performance outbound, this material offers the best opportunity to create multiple control layers with a single material. Rigid board continuous insulation can easily provide three-in-one protection in the building envelope when installed with sealed joints.
Polyiso insulation, a high-performance rigid foam board material, has been tested to conform to building codes as an alternative option as a WRB and air barrier when the board joints and penetrations are sealed with a compatible flashing component. Installation as such eliminates the need for a separate WRB and/or air barrier and creates a continuous control layer to achieve protection against air and water. However, if redundancy is what a designer is after, polyiso insulation can also be used in conjunction with various types of WRBs for added peace of mind.
When considering rigid board continuous insulation for thermal performance, including reduction of thermal bridging, polyiso is a solid choice, having the highest R-value in a thinner profile than other insulation materials. In addition, its inherent water-resistive properties ensure long-term protection for the building structure. And perhaps more importantly, if continuous insulation isn’t top of mind, maybe now is the perfect time to consider it.
With rising energy costs and stress on improving the energy efficiency of our buildings, polyiso can offer greater benefits for the building owner and occupants, as well as provide strong differentiators for your business, by simplifying wall design without sacrificing performance. A high-performing three-in-one solution in today’s market can add value by reducing cost in material and labor, reduce complexity in coordination of trades and help avoid project delays. Polyiso insulation provides this best-in-class solution, so now may be the time to reconsider your expectation of water-resistive barriers.
Polyiso Insulation for all Project Sizes and Complexities
A 3-in-1 product solution, like polyiso insulation, provides valuable benefits for architects, installers and general contractors. For contractors and installers who are looking to save time and labor, polyiso continuous insulation can improve job site efficiency when installed as the building’s WRB and air barrier.
For architects, utilizing polyiso continuous insulation as the WRB and air barrier will simplify their wall assemblies, while giving them peace of mind in high performance without sacrificing design. In addition, simplification of the building envelope reduces the chances for installation errors that could lead to future problems or product failures—that can benefit everyone in the long run.
Polyiso continuous wall insulation has been used for decades on projects of all sizes and complexities. It combines the expected thermal efficiency with the added protection of weather resistance to increase building envelope performance, while simplifying design and installation requirements for both commercial and residential projects.
One example of polyiso being used as a WRB is in the construction of NoHo West, a multi-use complex in North Hollywood, California. Using polyiso insulation, the project complied with the 2020 code updates requiring continuous insulation in all new construction. Because the design team chose a solution that could serve as both continuous insulation and a WRB, they were able to decrease material costs while shortening the construction timeline. This multifunctional solution that followed WRB protocol to meet code additionally reduced the environmental impact caused by excess construction materials and waste.
Thanks to the high R-value and energy efficiency of the product selected, the exterior wall system had fewer thermal breaks, thereby saving on long-term energy costs. And with less pressure placed on the building’s HVAC system, the UL GREENGUARD Gold certified polyiso insulation also reduced the building’s overall carbon footprint due to reduced heating and cooling needs. All residents and visitors to the NoHo West development now enjoy a comfortable place to live, work and play in a revitalized and green neighborhood hub. For more information on this project, you can click here.
Images courtesy of Atlas Roofing Corp.
Jen Frey is the senior product manager for Atlas Roofing Corp's polyiso roof and wall insulation division. She has more than 15 years’ experience in the building materials industry, representing brand leaders in high growth product categories, including roofing and building envelope. Frey has successfully launched innovative product solutions meeting customer needs and has been co-named in six patents.